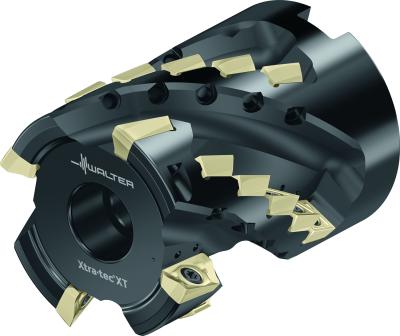
Walter has introduced the XTRA∙TEC® XT M5250 helical milling cutter, which is available in 2", 3", 50 mm, 63 mm and 80 mm diameters and is being offered with two different depths of cut per cutting diameter.
The full-effective design enables a high metal removal rate and delivers a smooth milling operation for the indexable inserts which are available either ground or sintered. Walter uses proven, double-edge BC 1605 system inserts on the face of the M5250. These inserts allow users to choose between various corner radii, cutting tool grades and six geometries. The milling cutter-specific SC 1105 inserts with four cutting edges serve as circumference, or peripheral inserts and provide excellent operational smoothness.
The G51 geometry, labeled “The quiet one” is ideal for tools with long overhangs or applications that are likely to involve vibration. When machining a high volume of titanium, the G55W WaveCut geometry is the first choice.
Walter’s latest generation of indexable insert milling cutters is distinguished by high performance combined with a high level of process reliability due to the optimized insert pocket design. In addition, each individual tool on the XTRA∙TEC® XT M5250 is cooled separately.
The M5250 cutter is effective for milling steel, cast iron, stainless steel, aluminum and other non-ferrous metals (ISO P, K, M and N workpiece groups), as well as materials with difficult cutting properties. Unlike other full-effective helical milling cutters, the XTRA∙TEC® XT M5250 can also be used for full slotting, shoulder milling, pocket milling and ramping. The positive rhombic basic shape of the face insert makes ramping possible.
The tool reduces process costs because of the two or four cutting edges per indexable insert and the use of the latest wear-resistant Tiger∙tec® cutting tool materials. In addition to machining aerospace components, applications include producing energy parts and general mechanical engineering.
Contact Details
Related Glossary Terms
- cutting tool materials
cutting tool materials
Cutting tool materials include cemented carbides, ceramics, cermets, polycrystalline diamond, polycrystalline cubic boron nitride, some grades of tool steels and high-speed steels. See HSS, high-speed steels; PCBN, polycrystalline cubic boron nitride; PCD, polycrystalline diamond.
- gang cutting ( milling)
gang cutting ( milling)
Machining with several cutters mounted on a single arbor, generally for simultaneous cutting.
- indexable insert
indexable insert
Replaceable tool that clamps into a tool body, drill, mill or other cutter body designed to accommodate inserts. Most inserts are made of cemented carbide. Often they are coated with a hard material. Other insert materials are ceramic, cermet, polycrystalline cubic boron nitride and polycrystalline diamond. The insert is used until dull, then indexed, or turned, to expose a fresh cutting edge. When the entire insert is dull, it is usually discarded. Some inserts can be resharpened.
- milling
milling
Machining operation in which metal or other material is removed by applying power to a rotating cutter. In vertical milling, the cutting tool is mounted vertically on the spindle. In horizontal milling, the cutting tool is mounted horizontally, either directly on the spindle or on an arbor. Horizontal milling is further broken down into conventional milling, where the cutter rotates opposite the direction of feed, or “up” into the workpiece; and climb milling, where the cutter rotates in the direction of feed, or “down” into the workpiece. Milling operations include plane or surface milling, endmilling, facemilling, angle milling, form milling and profiling.
- milling cutter
milling cutter
Loosely, any milling tool. Horizontal cutters take the form of plain milling cutters, plain spiral-tooth cutters, helical cutters, side-milling cutters, staggered-tooth side-milling cutters, facemilling cutters, angular cutters, double-angle cutters, convex and concave form-milling cutters, straddle-sprocket cutters, spur-gear cutters, corner-rounding cutters and slitting saws. Vertical cutters use shank-mounted cutting tools, including endmills, T-slot cutters, Woodruff keyseat cutters and dovetail cutters; these may also be used on horizontal mills. See milling.
- slotting
slotting
Machining, normally milling, that creates slots, grooves and similar recesses in workpieces, including T-slots and dovetails.