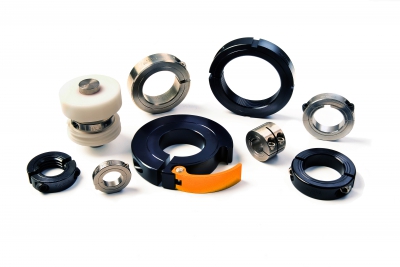
To match the varied needs of machine tool manufacturers, Ruland Manufacturing Co. Inc. offers more than 2,500 standard shaft collars. Machine tool manufacturers require round bore, threaded and bearing locknut-type shaft collars to meet the diverse needs of mills, lathes, bar feeders, coilers and other CNC equipment. Ruland says its clamp-style shaft collars are manufactured from select materials, have fine finishes, high holding power and precise face to bore perpendicularity, making them suitable for the demands of machine tools.
Clamp-style shaft collars can be used for guiding, spacing, stopping, mounting and component alignment. They are superior to set screw shaft collars as they do not mar the shaft, are easy to install and adjust and have significantly higher holding power. Ruland two-piece, clamp-style collars can be serviced in-place, offer increased holding power, and are mated throughout the manufacturing process for proper fit and alignment. Machine tool manufacturers benefit from the tightly controlled face to bore perpendicularity of Ruland shaft collars (TIR ≤ 0.002 inch or 0.05 mm), which is critical when they are used as a load bearing face or for aligning components such as bearings or gears. Ruland identifies this work surface with one or two circular grooves on the face of the shaft collar to assist in installation and design.
Threaded-shaft collars and clamp-type bearing locknuts are common on lathes, mills and other equipment that require higher axial holding power. Ruland manufactures them with double-tapped burr-free threads, allowing for smooth installation and removal, proper fit and extended shaft life. Bearing locknuts are designed to fit AFBMA standard shafting and utilize a clamp style design for high holding power. They have more precise face to bore perpendicularity of (TIR ≤ 0.0005 inch) to accommodate the needs of precision spindle bearings.
Contact Details
Related Glossary Terms
- computer numerical control ( CNC)
computer numerical control ( CNC)
Microprocessor-based controller dedicated to a machine tool that permits the creation or modification of parts. Programmed numerical control activates the machine’s servos and spindle drives and controls the various machining operations. See DNC, direct numerical control; NC, numerical control.