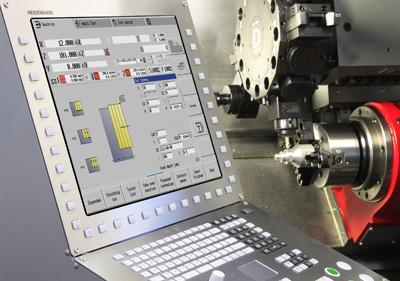
HEIDENHAIN's top-of-the-line lathe control, the CNC PILOT 640, now offers enhanced functions and new hardware for both the machine operator and builder. HEIDENHAIN lathe controls distinguish themselves by their convenient and simple programming, as well as their high-quality, ergonomic operating panel.
With the CNC PILOT 640, operators are working with a HEIDENHAIN lathe control of the latest generation. It has been conceived for universal lathes, fully automatic turning centers, combined turning-milling machines, vertical lathes and vertical boring and turning mills up to 5-axis machining with X, Y, Z, B and C axes.
For the end user, the new software offers high-resolution, finely 3-D graphic simulation. The results of turning, drilling and milling processes can be evaluated before the machining (e.g. in regard to material cuts). The Rotational View allows inspection of the part from all angles. It can be zoomed in and out on the cylindrical surface and in the tilted plane. Even the tool and the tool holder geometry can be displayed.
As an option, CNC PILOT 640 now offers Load Monitoring where a multi-colored bar graph displays the load of both the spindle and the motor. Simple parameterization is available to define utilization threshold values of a reference operation. Exceeding the first threshold triggers the exchange of a replacement tool. If the second threshold is exceeded, the machine stops. In this way, tool breakage can be avoided, process reliability can be enhanced and unattended shifts can be extended.
Additionally, eccentric turning and non-circular turning is now possible. This allows the machining of oval and polygonal parts, as well as cams without any additional machine elements. Further improvements include better oversight in the file manager and in the technology data display as well as the possibility to include or exclude the tool selection to generate automatic programs (TURN PLUS, automatically generates a program from created contours).
New generation HEIDENHAIN touch probes are now supported with the CNC PILOT 640.
For the machine builder, synchronizing functions and real-time coupling functions have been developed that allow the actual and nominal calculation of complex simultaneous movements of several axes. Up to 20 controls loops are now available, and control loop groups can be enabled. Worth mentioning is the "Copy default data" function that allows the creation of a back-up file in an easy and save way. Finally, commissioning has been made easier and new ways to design OEM-specific buttons have been created.
Contact Details
Related Glossary Terms
- 3-D
3-D
Way of displaying real-world objects in a natural way by showing depth, height and width. This system uses the X, Y and Z axes.
- boring
boring
Enlarging a hole that already has been drilled or cored. Generally, it is an operation of truing the previously drilled hole with a single-point, lathe-type tool. Boring is essentially internal turning, in that usually a single-point cutting tool forms the internal shape. Some tools are available with two cutting edges to balance cutting forces.
- centers
centers
Cone-shaped pins that support a workpiece by one or two ends during machining. The centers fit into holes drilled in the workpiece ends. Centers that turn with the workpiece are called “live” centers; those that do not are called “dead” centers.
- computer numerical control ( CNC)
computer numerical control ( CNC)
Microprocessor-based controller dedicated to a machine tool that permits the creation or modification of parts. Programmed numerical control activates the machine’s servos and spindle drives and controls the various machining operations. See DNC, direct numerical control; NC, numerical control.
- gang cutting ( milling)
gang cutting ( milling)
Machining with several cutters mounted on a single arbor, generally for simultaneous cutting.
- lathe
lathe
Turning machine capable of sawing, milling, grinding, gear-cutting, drilling, reaming, boring, threading, facing, chamfering, grooving, knurling, spinning, parting, necking, taper-cutting, and cam- and eccentric-cutting, as well as step- and straight-turning. Comes in a variety of forms, ranging from manual to semiautomatic to fully automatic, with major types being engine lathes, turning and contouring lathes, turret lathes and numerical-control lathes. The engine lathe consists of a headstock and spindle, tailstock, bed, carriage (complete with apron) and cross slides. Features include gear- (speed) and feed-selector levers, toolpost, compound rest, lead screw and reversing lead screw, threading dial and rapid-traverse lever. Special lathe types include through-the-spindle, camshaft and crankshaft, brake drum and rotor, spinning and gun-barrel machines. Toolroom and bench lathes are used for precision work; the former for tool-and-die work and similar tasks, the latter for small workpieces (instruments, watches), normally without a power feed. Models are typically designated according to their “swing,” or the largest-diameter workpiece that can be rotated; bed length, or the distance between centers; and horsepower generated. See turning machine.
- milling
milling
Machining operation in which metal or other material is removed by applying power to a rotating cutter. In vertical milling, the cutting tool is mounted vertically on the spindle. In horizontal milling, the cutting tool is mounted horizontally, either directly on the spindle or on an arbor. Horizontal milling is further broken down into conventional milling, where the cutter rotates opposite the direction of feed, or “up” into the workpiece; and climb milling, where the cutter rotates in the direction of feed, or “down” into the workpiece. Milling operations include plane or surface milling, endmilling, facemilling, angle milling, form milling and profiling.
- turning
turning
Workpiece is held in a chuck, mounted on a face plate or secured between centers and rotated while a cutting tool, normally a single-point tool, is fed into it along its periphery or across its end or face. Takes the form of straight turning (cutting along the periphery of the workpiece); taper turning (creating a taper); step turning (turning different-size diameters on the same work); chamfering (beveling an edge or shoulder); facing (cutting on an end); turning threads (usually external but can be internal); roughing (high-volume metal removal); and finishing (final light cuts). Performed on lathes, turning centers, chucking machines, automatic screw machines and similar machines.