Contact Details
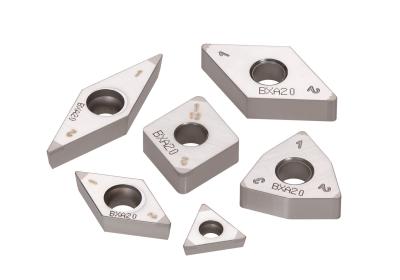
Tungaloy adds a substantial number of new geometries and shapes to its BXA20 line, a successful grade of coated T-CBN inserts, designed to deliver efficient solutions to hard turning operations.
The BXA20 insert boasts a nano-multilayered PVD coating which is twice as thick as conventional grades and coated on a dedicated PCBN substrate with enhanced toughness. This adds both wear and fracture resistance to the grade, promising long and predictable tool life in continuous to interrupted cuts of hardened parts.
Twenty two items are being added in this expansion, including inserts with wiper geometries and WavyJoint technology, to address a broader range of hard part turning needs.
Related Glossary Terms
- hard turning
hard turning
Single-point cutting of a workpiece that has a hardness value higher than 45 HRC.
- physical vapor deposition ( PVD)
physical vapor deposition ( PVD)
Tool-coating process performed at low temperature (500° C), compared to chemical vapor deposition (1,000° C). Employs electric field to generate necessary heat for depositing coating on a tool’s surface. See CVD, chemical vapor deposition.
- polycrystalline cubic boron nitride ( PCBN)
polycrystalline cubic boron nitride ( PCBN)
Cutting tool material consisting of polycrystalline cubic boron nitride with a metallic or ceramic binder. PCBN is available either as a tip brazed to a carbide insert carrier or as a solid insert. Primarily used for cutting hardened ferrous alloys.
- turning
turning
Workpiece is held in a chuck, mounted on a face plate or secured between centers and rotated while a cutting tool, normally a single-point tool, is fed into it along its periphery or across its end or face. Takes the form of straight turning (cutting along the periphery of the workpiece); taper turning (creating a taper); step turning (turning different-size diameters on the same work); chamfering (beveling an edge or shoulder); facing (cutting on an end); turning threads (usually external but can be internal); roughing (high-volume metal removal); and finishing (final light cuts). Performed on lathes, turning centers, chucking machines, automatic screw machines and similar machines.
- wiper
wiper
Metal-removing edge on the face of a cutter that travels in a plane perpendicular to the axis. It is the edge that sweeps the machined surface. The flat should be as wide as the feed per revolution of the cutter. This allows any given insert to wipe the entire workpiece surface and impart a fine surface finish at a high feed rate.