Contact Details
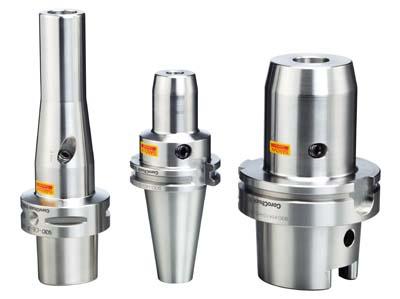
February 2013 — The CoroChuck 930 is a high precision hydraulic chuck from Sandvik Coromant that brings secure tooling performance to milling and drilling operations. CoroChuck 930 is for meeting the demands of high runout precision, and extensive tests have shown it to provide the best pull-out security available, according to the company.
The secret behind the high precision and pull-out security is in the optimized design of the brazed membrane, which allows for maximum secure clamping with two supports on each side (fulcrums).
This design ensures excellent torque transmission to improve the performance of solid carbide end mills, drills and reaming tools. This performance is repeated over multiple clamping cycles to retain high quality component surfaces and extend tool life. Additionally, the CoroChuck 930 is designed with dampening features that minimize vibrations during the machining process.
Based on a hydraulic tool clamping system, the CoroChuck 930 can be quickly tightened or released with a dedicated torque wrench, improving efficiency through quick and easy set-ups and changes. No external equipment is required to clamp or unclamp the system.
The chuck holds tolerances withinµm to improve tool precision, surface finish and productivity. The precision runout can be measured at less than 4µm (157 microinch) at 2.5 times DC.
CoroChuck 930 is suitable for all types of machine tools that either have a rotating spindle or workpiece; Lathes, Multi-Task machines, Machining Centers and driven tools in Turning Centers, and Vertical Turning Lathes.
Available in pencil, slender and heavy duty design, CoroChuck 930 is balanced according to DIN 69888.
Related Glossary Terms
- centers
centers
Cone-shaped pins that support a workpiece by one or two ends during machining. The centers fit into holes drilled in the workpiece ends. Centers that turn with the workpiece are called “live” centers; those that do not are called “dead” centers.
- chuck
chuck
Workholding device that affixes to a mill, lathe or drill-press spindle. It holds a tool or workpiece by one end, allowing it to be rotated. May also be fitted to the machine table to hold a workpiece. Two or more adjustable jaws actually hold the tool or part. May be actuated manually, pneumatically, hydraulically or electrically. See collet.
- gang cutting ( milling)
gang cutting ( milling)
Machining with several cutters mounted on a single arbor, generally for simultaneous cutting.
- milling
milling
Machining operation in which metal or other material is removed by applying power to a rotating cutter. In vertical milling, the cutting tool is mounted vertically on the spindle. In horizontal milling, the cutting tool is mounted horizontally, either directly on the spindle or on an arbor. Horizontal milling is further broken down into conventional milling, where the cutter rotates opposite the direction of feed, or “up” into the workpiece; and climb milling, where the cutter rotates in the direction of feed, or “down” into the workpiece. Milling operations include plane or surface milling, endmilling, facemilling, angle milling, form milling and profiling.
- turning
turning
Workpiece is held in a chuck, mounted on a face plate or secured between centers and rotated while a cutting tool, normally a single-point tool, is fed into it along its periphery or across its end or face. Takes the form of straight turning (cutting along the periphery of the workpiece); taper turning (creating a taper); step turning (turning different-size diameters on the same work); chamfering (beveling an edge or shoulder); facing (cutting on an end); turning threads (usually external but can be internal); roughing (high-volume metal removal); and finishing (final light cuts). Performed on lathes, turning centers, chucking machines, automatic screw machines and similar machines.
Additional Products from Sandvik Coromant Co.
Pagination
- First page
- Previous page
- …
- 5
- 6
- 7
- 8
- 9
- 10
- 11
- 12
- 13