Contact Details
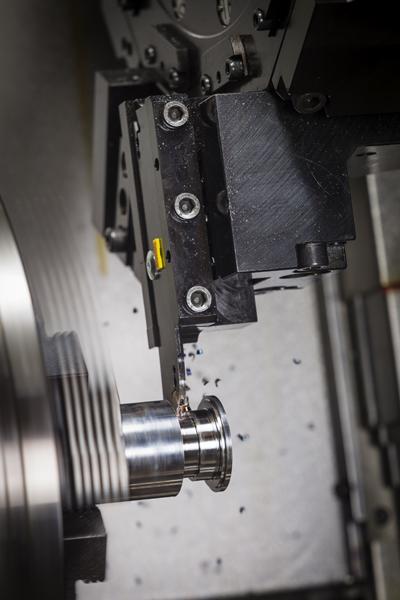
Sandvik Coromant introduces a parting off concept for deep grooves and long overhangs.
For volume bar-fed parts manufacturing, producers are continually seeking solutions that offer more efficient material usage to control their overall costs and support increased bar feed capacity. Ensuring process security through a predictable and consistent tool life is also important to ensure reproducible parts quality, particularly for parting off.
With the introduction of CoroCut QD, a range of solutions covering parting and SL blades, adaptors, shank and Swiss tools and a new generation of inserts for parting off, these aspirations can be met. CoroCut QD builds on the well-proven Q-Cut and CoroCut ranges, and expands the options for these processes with a flexible, simple-to-use and easy-to-select tooling range.
The focus areas in developing this new concept have been new tool material and a tooling design for greater process stability. The tool attachment is achieved via a smart, yet simple, user-friendly clamping mechanism. The tool tip seat is tilted 20 degrees and incorporates a back stop to withstand high cutting forces. For insert widths 0.078" (2mm) and wider, the insert interface has a rail to increase stability.
In developing CoroCut QD, attention has been paid to the development of new and upgraded parting geometries. When parting off a component, minimized cutting forces and efficient material removal are important. An insert should be as narrow as possible and have a geometry that makes the chip narrower than the groove to provide a parting off operation with good chip control and surface finish. Within the CoroCut QD concept are inserts with five parting geometries and one turning geometry as well as options for "do-it-yourself" grinding and tailor-made options for a broad range of material types. The PVD insert coating offers better adhesion, improved edge-line qualities and better ER tolerance.
Related Glossary Terms
- feed
feed
Rate of change of position of the tool as a whole, relative to the workpiece while cutting.
- grinding
grinding
Machining operation in which material is removed from the workpiece by a powered abrasive wheel, stone, belt, paste, sheet, compound, slurry, etc. Takes various forms: surface grinding (creates flat and/or squared surfaces); cylindrical grinding (for external cylindrical and tapered shapes, fillets, undercuts, etc.); centerless grinding; chamfering; thread and form grinding; tool and cutter grinding; offhand grinding; lapping and polishing (grinding with extremely fine grits to create ultrasmooth surfaces); honing; and disc grinding.
- parting
parting
When used in lathe or screw-machine operations, this process separates a completed part from chuck-held or collet-fed stock by means of a very narrow, flat-end cutting, or parting, tool.
- physical vapor deposition ( PVD)
physical vapor deposition ( PVD)
Tool-coating process performed at low temperature (500° C), compared to chemical vapor deposition (1,000° C). Employs electric field to generate necessary heat for depositing coating on a tool’s surface. See CVD, chemical vapor deposition.
- shank
shank
Main body of a tool; the portion of a drill or similar end-held tool that fits into a collet, chuck or similar mounting device.
- tolerance
tolerance
Minimum and maximum amount a workpiece dimension is allowed to vary from a set standard and still be acceptable.
- turning
turning
Workpiece is held in a chuck, mounted on a face plate or secured between centers and rotated while a cutting tool, normally a single-point tool, is fed into it along its periphery or across its end or face. Takes the form of straight turning (cutting along the periphery of the workpiece); taper turning (creating a taper); step turning (turning different-size diameters on the same work); chamfering (beveling an edge or shoulder); facing (cutting on an end); turning threads (usually external but can be internal); roughing (high-volume metal removal); and finishing (final light cuts). Performed on lathes, turning centers, chucking machines, automatic screw machines and similar machines.