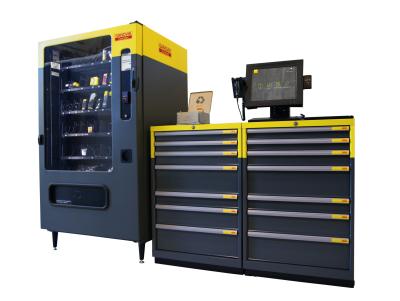
Global leader in metal cutting, Sandvik Coromant has extended its CoroPlus® range of digital solutions with its new CoroPlus® Tool Supply service. Users of the new solution can unite tool inventory management with tool logistics, helping operators to pick and return tools, manage restocking and maintain inventory control using the same interface.
Keeping track of cutting tools can be a difficult and time consuming process, especially on a busy machine shop floor that requires multiple versions of the same tool. To help maintain control over tool inventory, the CoroPlus® Tool Supply combines hardware, software and service solutions to form a user-friendly tool restocking and inventory management system.
The tool supply consists of software, hardware and supporting service elements. Using the CoroPlus® Tool Supply hardware, manufacturers can easily store and keep track of tools. Storage options can be tailor made according to facility demands, with tool vending solutions ranging from open stock, drawers and lids to full tool cabinets. Each hardware option allows tools to be securely stored, without the risk of loss or damage.
As well as physically storing tools, manufacturers can collect and manage a wealth of tool data using the CoroPlus® Tool Supply cloud-based interface, which can be used with or without a vending cabinet.
Tool use on the shop floor feeds data into the administration and management side of the system, helping engineers, purchasing and management teams to keep track of tool usage, costs, purchasing and inventory. Connecting to multiple suppliers’ tool databases, CoroPlus® Tool Supply can store correct tool information, including ISO parameters, bill of material (BOM), spare parts, product images and computer aided design (CAD) file types, in a single area.
For machine operators, this means a greater insight into tool availability, easy access to technical data and the ability to source the right tool for the job. However, this is not the only benefit of the system. The interface can unite several areas of inventory management to streamline restocking. Using CoroPlus® Tool Supply, purchase orders for new tools can be raised directly from the shop floor, reducing administration costs. Because inventory can be replenished automatically, plant managers have greater control of their inventory and instant knowledge of their tools’ status.
“The CoroPlus® range exists to make manufacturing companies more profitable, streamlined and prepared for the digitalization of industry,” explains Markus Eriksson, Business Development Manager for Digital Machining at Sandvik Coromant. “CoroPlus® Tool Supply complements the existing components of our CoroPlus® service, helping to streamline operations even further and bring a new perspective on tool inventory through its integration into the CoroPlus® family.
“Although cutting tools aren’t manufacturing’s greatest expense, total tool inventory costs quickly amount if large numbers of tools are not handled correctly. The CoroPlus® Tool Supply interface removes the hassle of tracking down and re-ordering tools, while delivering measurable productivity benefits.”
Integrating CoroPlus® Tool Supply doesn’t only benefit those operating machine tools. “Because users of the tool management software and hardware can automatically raise orders for new tools from the shop floor, finance teams will be less burdened with the administration of reordering new parts,” explained Eriksson. “Elsewhere, operations teams will find overall tool consumption is reduced, because the exact status of each tool can be instantly discovered — there’s no risk of tools being discarded because it’s assumed they’ve surpassed their lifecycle.
“Additional services are available alongside the tool supply, such as customer specific training, ERP interfacing and interactive system optimization support. Through these services, Sandvik Coromant helps customers customize reporting, review their specific product data needs and assess inventory levels to make the most of the CoroPlus® Tool Supply.”
The potential of the tool supply extends beyond its current capabilities. Future ambitions involve connecting it to other areas of the CoroPlus® range, such as the CoroPlus® Tool Guide and CoroPlus® Tool Library. Then, users will not only benefit from information on the location and status of their tools, but they will also have the opportunity to access full recommendations on tool use, such as advised cutting speeds and data, all taken from the same cloud source.
You can request a software demo or access a trial for the CoroPlus® Tool Supply by contacting your local Sandvik Coromant representative.