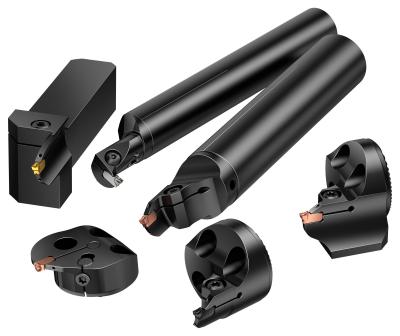
Sandvik Coromant, a leader in metal cutting, has launched CoroCut® QI, a range of internal and face grooving inserts designed for smaller diameters. Optimized to enable a lighter cutting action and reduced cutting forces, CoroCut® QI ensures high process security, reliable grooving operations and precise chip evacuation, resulting in high surface quality grooves.
The addition of CoroCut® QI completes the CoroCut® Q platform, which already consists of CoroCut® QD for parting off and CoroCut® QF for secure face grooving. CoroCut® QI provides a comprehensive selection of optimized tools for numerous parting and grooving applications, designed specifically for smaller diameters. All inserts fit both internal and face grooving tool holders, making it easier for users to select the right tool.
CoroCut® QI is divided into internal grooving and face grooving application areas, and is an upgrade of the T-max Q-Cut® 151.3 program. The improved design allows for greater chip control, a 10% productivity increase, 20% improved tool life aided by tighter edge-rounding tolerances and internal coolant for both internal and face grooving tools.
Key features of the CoroCut® QI include an optimized tip seat angle for lighter cutting action and cutting forces that aid vibration-free machining, a rail insert seat for a stable and precise insert position ensuring minimal insert movement. In addition, screw-clamped tool holders ensure stability and high process security, and inserts with high edge line quality increase tool life and surface quality.
“Grooving can be a difficult technique to master,” said Angélica González, Product Manager of the CoroCut® Q platform at Sandvik Coromant. “Long overhangs, difficult chip evacuation and stuck chips are frequent problems when machining internal and face grooves. CoroCut® QI has been developed to tackle these challenges to help achieve optimal results. Besides this, most CoroCut® QI tools have internal coolant channels that deliver coolant directly to the cutting zone to enable efficient chip evacuation with minimum damage to the surface.
“The smaller the groove, the harder it is to machine. To combat this issue, CoroCut® QI inserts are specifically designed for small diameters that require great precision. For example, the minimum hole diameter for internal grooving is between 12 and 60 millimeters (mm) with a cutting depth of two and eleven millimeters. Face grooving inserts can be used in a first cut diameter between 16 and 102 mm, with a cutting depth of 5.5 to 20 mm.”
The insert geometries include -GF, a ground sharp insert for internal grooving, -TF with direct pressed geometry for face grooving and internal grooving and turning, and -RM, ideal for non-linear turning such as internal and face profiling.
“CoroCut® QI is the upgrade to our previous grooving system,” continued González. “In fact, performance tests compared with competing tools have demonstrated better process security and chip evacuation for a higher quality surface finish.”
Contact Details
Related Glossary Terms
- coolant
coolant
Fluid that reduces temperature buildup at the tool/workpiece interface during machining. Normally takes the form of a liquid such as soluble or chemical mixtures (semisynthetic, synthetic) but can be pressurized air or other gas. Because of water’s ability to absorb great quantities of heat, it is widely used as a coolant and vehicle for various cutting compounds, with the water-to-compound ratio varying with the machining task. See cutting fluid; semisynthetic cutting fluid; soluble-oil cutting fluid; synthetic cutting fluid.
- grooving
grooving
Machining grooves and shallow channels. Example: grooving ball-bearing raceways. Typically performed by tools that are capable of light cuts at high feed rates. Imparts high-quality finish.
- parting
parting
When used in lathe or screw-machine operations, this process separates a completed part from chuck-held or collet-fed stock by means of a very narrow, flat-end cutting, or parting, tool.
- profiling
profiling
Machining vertical edges of workpieces having irregular contours; normally performed with an endmill in a vertical spindle on a milling machine or with a profiler, following a pattern. See mill, milling machine.
- turning
turning
Workpiece is held in a chuck, mounted on a face plate or secured between centers and rotated while a cutting tool, normally a single-point tool, is fed into it along its periphery or across its end or face. Takes the form of straight turning (cutting along the periphery of the workpiece); taper turning (creating a taper); step turning (turning different-size diameters on the same work); chamfering (beveling an edge or shoulder); facing (cutting on an end); turning threads (usually external but can be internal); roughing (high-volume metal removal); and finishing (final light cuts). Performed on lathes, turning centers, chucking machines, automatic screw machines and similar machines.