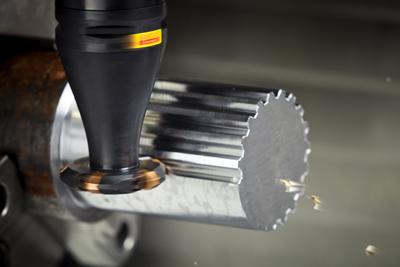
The CoroMill 172 and 171 disc cutting concepts adapted for gears, splines and racks enables gear profile manufacturing on most types of CNC machines. A primary benefit of the cutter is single setup machining: using one machine for many operations and one cutter body for different insert types. This significantly reduces setup time, machine down times or the need to outsource the gear profiling operation due to lack of dedicated machines.
CoroMill 172 and 171 disc cutters offer an easy-to-program, versatile and time saving solution for milling of high-quality gear profiles. Thanks to indexable carbide insert technology and powerful iLock interface (on CoroMill 172), components can be machined in flexible, non-dedicated machines, such as multi-task machines and machining centers, as well as in hobbing machines.
Both concepts are particularly cost-effective for small-to-medium batches of internal and external gears and splines, as well as racks and pinions. They can be used to generate straight flank or involute profiles, and are designed to be able to hold a range of inserts, offering flexibility for customers producing gears and splines of close module size and similar tooth profiles.
CoroMill 172 is available in module 3-10 (DP 8 — 2.6), CoroMill 171 in module 0.8-4 (DP 32 — 8) with gear profiles in accordance with DIN 867 for gears and DIN 5480 for splines. Diameters range from 2.5-10" (63-254mm) for the CoroMill 172 and 1.5 to 3" (39-70mm) for CoroMill 171. Machining using ground carbide inserts can take place dry, further reducing costs.
Contact Details
Related Glossary Terms
- centers
centers
Cone-shaped pins that support a workpiece by one or two ends during machining. The centers fit into holes drilled in the workpiece ends. Centers that turn with the workpiece are called “live” centers; those that do not are called “dead” centers.
- computer numerical control ( CNC)
computer numerical control ( CNC)
Microprocessor-based controller dedicated to a machine tool that permits the creation or modification of parts. Programmed numerical control activates the machine’s servos and spindle drives and controls the various machining operations. See DNC, direct numerical control; NC, numerical control.
- gang cutting ( milling)
gang cutting ( milling)
Machining with several cutters mounted on a single arbor, generally for simultaneous cutting.
- milling
milling
Machining operation in which metal or other material is removed by applying power to a rotating cutter. In vertical milling, the cutting tool is mounted vertically on the spindle. In horizontal milling, the cutting tool is mounted horizontally, either directly on the spindle or on an arbor. Horizontal milling is further broken down into conventional milling, where the cutter rotates opposite the direction of feed, or “up” into the workpiece; and climb milling, where the cutter rotates in the direction of feed, or “down” into the workpiece. Milling operations include plane or surface milling, endmilling, facemilling, angle milling, form milling and profiling.
- profiling
profiling
Machining vertical edges of workpieces having irregular contours; normally performed with an endmill in a vertical spindle on a milling machine or with a profiler, following a pattern. See mill, milling machine.