Contact Details
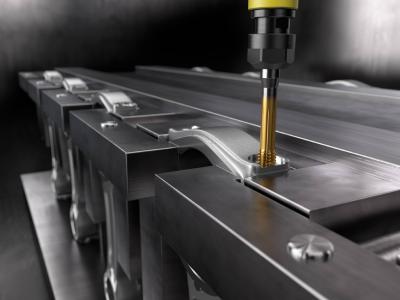
Sandvik Coromant has launched a new thread forming tap optimized for ISO P steel machining, which is designed to boost productivity, particularly in the automotive industry. The CoroTap 400 offers chip-free tapping, as well as faster machining times and stronger threads through reduced torque and an optimized geometry.
The automotive industry has extremely high requirements when it comes to safeguarding quality and has implemented robust and rigorous processes for this reason. The new tap has been created to meet those exacting demands by ensuring superior thread quality, improved process security and longer tool life, resulting in a combination of greater efficiency and reduced costs. In comparison tests, the CoroTap 400 delivered a significantly more secure and stable tap than its competitors while achieving cutting speeds up to 50 percent faster.
Among the main features of the new tap is an optimized lobe profile designed specifically for ISO P applications. By increasing the number of lobes on the tap and giving it a shorter thread length, Sandvik Coromant has reduced torque at the machine tool spindle which facilitates increased cutting speeds and, in turn, improves productivity. As a result, the CoroTap 400 offers the customer key benefits such as greater process security, fewer machine stoppages, reduced cost per hole and improved tool life for better process planning.
Made with a new grade of substrate and coating, the new thread forming tap provides machine tool operators peace of mind through its high-level reliability and adaptability for use with lower torque spindle machines. For senior managers in the automotive industry, the tap satisfies their green light machining demands while extremely high levels of repeatability and predictability afford them extra confidence in relation to maintaining the highest possible production standards.
Offering a more consistent and reliable threading process, the CoroTap 400 has been designed with a geometry that can reduce the force required for machining a steel component by up to 30 percent. At the same time, the working life of the tap can be up to twice as long as similar thread forming tools.
Designed to be used on steels up to 330 HB in conjunction with such drills as Sandvik Coromant’s CoroDrill 860, the new tap is ideal for machining automotive components such as connecting rods, wheel hubs, crank shafts, axles, gears and transmissions. Not restricted to the automotive industry, however, the CoroTap 400 is also suited to rail or general engineering applications, where it can improve productivity and cut costs when forming threads in rail wheels, flanges, rivets, housings, boom cylinders, tubes and a range of other components.
Related Glossary Terms
- Brinell hardness number ( HB)
Brinell hardness number ( HB)
Number related to the applied load (usually, 500 kgf and 3,000 kgf) and to the surface area of the permanent impression made by a 10mm ball indenter. The Brinell hardness number is a calculated value of the applied load (kgf) divided by the surface area of the indentation (mm2). Therefore, the unit of measure of a Brinell hardness number is kgf/mm2, but it is always omitted.
- tap
tap
Cylindrical tool that cuts internal threads and has flutes to remove chips and carry tapping fluid to the point of cut. Normally used on a drill press or tapping machine but also may be operated manually. See tapping.
- tapping
tapping
Machining operation in which a tap, with teeth on its periphery, cuts internal threads in a predrilled hole having a smaller diameter than the tap diameter. Threads are formed by a combined rotary and axial-relative motion between tap and workpiece. See tap.
- threading
threading
Process of both external (e.g., thread milling) and internal (e.g., tapping, thread milling) cutting, turning and rolling of threads into particular material. Standardized specifications are available to determine the desired results of the threading process. Numerous thread-series designations are written for specific applications. Threading often is performed on a lathe. Specifications such as thread height are critical in determining the strength of the threads. The material used is taken into consideration in determining the expected results of any particular application for that threaded piece. In external threading, a calculated depth is required as well as a particular angle to the cut. To perform internal threading, the exact diameter to bore the hole is critical before threading. The threads are distinguished from one another by the amount of tolerance and/or allowance that is specified. See turning.