Contact Details
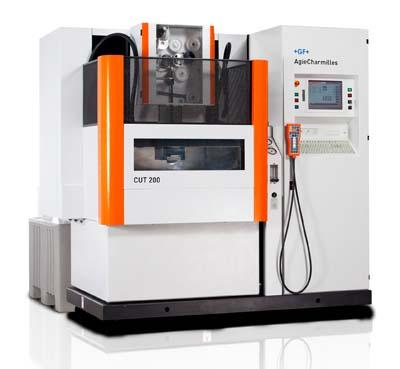
GF AgieCharmilles says its CUT 200 Wire EDM provides faster spark-to-spark wire threading, increases energy efficiency and boosts productivity when cutting parts of variable heights. The machine also offers higher flexibility through its ability to reliably hold tolerances measured inµm over a wide range of part sizes.
The CUT 200 integrates GF AgieCharmilles' Power Expert smart module, which continuously calculates part thickness, checking flushing pressure and adjusting machine power accordingly. This prevents wire breakage when changing the part thickness being machined. The machine also offers an optional Renishaw touch probe that allows users to inspect finished parts while still on the worktable in the machine, eliminating the need for part inspection with a CMM.
The CUT 200 accommodates wire diameters ranging from 0.07mm to 0.33mm and can handle part tapers of up to 45 degrees, regardless of part thickness. The machine's digital CC generator enables surface finishes as fine as Ra 0.1µm and an optional power module can boost cutting speed to 37.2 in2/hr. Additionally, the Econowatt 2 smart module provides energy savings by allowing operators to define conditions in which the machine will automatically shut down or awaken to complete thermal stabilization prior to production.
Related Glossary Terms
- cutting speed
cutting speed
Tangential velocity on the surface of the tool or workpiece at the cutting interface. The formula for cutting speed (sfm) is tool diameter 5 0.26 5 spindle speed (rpm). The formula for feed per tooth (fpt) is table feed (ipm)/number of flutes/spindle speed (rpm). The formula for spindle speed (rpm) is cutting speed (sfm) 5 3.82/tool diameter. The formula for table feed (ipm) is feed per tooth (ftp) 5 number of tool flutes 5 spindle speed (rpm).
- electrical-discharge machining ( EDM)
electrical-discharge machining ( EDM)
Process that vaporizes conductive materials by controlled application of pulsed electrical current that flows between a workpiece and electrode (tool) in a dielectric fluid. Permits machining shapes to tight accuracies without the internal stresses conventional machining often generates. Useful in diemaking.
- threading
threading
Process of both external (e.g., thread milling) and internal (e.g., tapping, thread milling) cutting, turning and rolling of threads into particular material. Standardized specifications are available to determine the desired results of the threading process. Numerous thread-series designations are written for specific applications. Threading often is performed on a lathe. Specifications such as thread height are critical in determining the strength of the threads. The material used is taken into consideration in determining the expected results of any particular application for that threaded piece. In external threading, a calculated depth is required as well as a particular angle to the cut. To perform internal threading, the exact diameter to bore the hole is critical before threading. The threads are distinguished from one another by the amount of tolerance and/or allowance that is specified. See turning.
- wire EDM
wire EDM
Process similar to ram electrical-discharge machining except a small-diameter copper or brass wire is used as a traveling electrode. Usually used in conjunction with a CNC and only works when a part is to be cut completely through. A common analogy is wire electrical-discharge machining is like an ultraprecise, electrical, contour-sawing operation.
Additional Products from GF Machining Solutions
Pagination
- First page
- Previous page
- 1
- 2
- 3
- 4
- 5
- 6