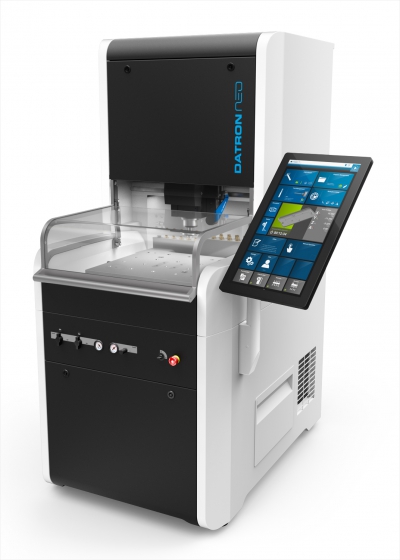
DATRON Dynamics Inc. offers the DATRON neo compact CNC milling machine – the latest addition to the company’s line of high-speed machining systems. Designed from the ground up to deliver a productive, in-office machining solution that improves and accelerates today’s engineering workflow, the DATRON neo reportedly offers simple, clean operation and easy post-processing. The affordable-yet-powerful neo enables design professionals to create precision models, prototypes and 3D metal parts without leaving the workplace.
With its intuitive operation terminal featuring DATRON’s own “next” software, this compact milling machine appeals to machining beginners. The neo combines an interior camera and a multifunction touch screen interface for intuitive operation. The neo’s integrated camera and 3D touch probe is designed to eliminate the time-consuming task of setting up jobs by using automatic recognition of the workpiece location which is drawn by the operator directly onto the touch screen. The interface quickly guides users through the milling process much like a smartphone or tablet app. Beginners benefit from the simple user interface and graphics.
“The DATRON neo’s compact design and friendly interface resemble that of a 3D printer,” said Robert Murphy, vice president of DATRON Dynamics. “The ergonomic design of the machine allows operators to load a workpiece from a position above the machining table while the height and angle of the workpiece is automatically setup at the operating terminal. The clean design and innovative enclosure give the operator a perfect view of and easy access to the machining area, which is quite ample in relation to the machine’s very small footprint. In fact, the machine fits through a standard doorway and can be easily installed within a few hours."
Ideal for rapid tooling, design communication, and short-run manufacturing the DATRON neo is capable of milling a variety of materials up to 20” x 16.5” x 9” in size with its robust 40,000-rpm spindle and 24-station automatic toolchanger.
“The DATRON neo brings easy-to-use, professional quality high-speed milling capabilities into any workspace, at an exceptional price” said Bill King, president of DATRON Dynamics. “We are thrilled to offer this powerful new product to help our wide range of customers innovate faster and mill perfect quality parts.”
Contact Details
Related Glossary Terms
- automatic toolchanger
automatic toolchanger
Mechanism typically included in a machining center that, on the appropriate command, removes one cutting tool from the spindle nose and replaces it with another. The changer restores the used tool to the magazine and selects and withdraws the next desired tool from the storage magazine. The changer is controlled by a set of prerecorded/predetermined instructions associated with the part(s) to be produced.
- computer numerical control ( CNC)
computer numerical control ( CNC)
Microprocessor-based controller dedicated to a machine tool that permits the creation or modification of parts. Programmed numerical control activates the machine’s servos and spindle drives and controls the various machining operations. See DNC, direct numerical control; NC, numerical control.
- gang cutting ( milling)
gang cutting ( milling)
Machining with several cutters mounted on a single arbor, generally for simultaneous cutting.
- milling
milling
Machining operation in which metal or other material is removed by applying power to a rotating cutter. In vertical milling, the cutting tool is mounted vertically on the spindle. In horizontal milling, the cutting tool is mounted horizontally, either directly on the spindle or on an arbor. Horizontal milling is further broken down into conventional milling, where the cutter rotates opposite the direction of feed, or “up” into the workpiece; and climb milling, where the cutter rotates in the direction of feed, or “down” into the workpiece. Milling operations include plane or surface milling, endmilling, facemilling, angle milling, form milling and profiling.
- milling machine ( mill)
milling machine ( mill)
Runs endmills and arbor-mounted milling cutters. Features include a head with a spindle that drives the cutters; a column, knee and table that provide motion in the three Cartesian axes; and a base that supports the components and houses the cutting-fluid pump and reservoir. The work is mounted on the table and fed into the rotating cutter or endmill to accomplish the milling steps; vertical milling machines also feed endmills into the work by means of a spindle-mounted quill. Models range from small manual machines to big bed-type and duplex mills. All take one of three basic forms: vertical, horizontal or convertible horizontal/vertical. Vertical machines may be knee-type (the table is mounted on a knee that can be elevated) or bed-type (the table is securely supported and only moves horizontally). In general, horizontal machines are bigger and more powerful, while vertical machines are lighter but more versatile and easier to set up and operate.
- milling machine ( mill)2
milling machine ( mill)
Runs endmills and arbor-mounted milling cutters. Features include a head with a spindle that drives the cutters; a column, knee and table that provide motion in the three Cartesian axes; and a base that supports the components and houses the cutting-fluid pump and reservoir. The work is mounted on the table and fed into the rotating cutter or endmill to accomplish the milling steps; vertical milling machines also feed endmills into the work by means of a spindle-mounted quill. Models range from small manual machines to big bed-type and duplex mills. All take one of three basic forms: vertical, horizontal or convertible horizontal/vertical. Vertical machines may be knee-type (the table is mounted on a knee that can be elevated) or bed-type (the table is securely supported and only moves horizontally). In general, horizontal machines are bigger and more powerful, while vertical machines are lighter but more versatile and easier to set up and operate.
- toolchanger
toolchanger
Carriage or drum attached to a machining center that holds tools until needed; when a tool is needed, the toolchanger inserts the tool into the machine spindle. See automatic toolchanger.