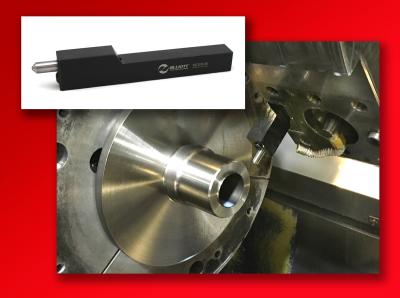
Diamond Burnishing Tools by Elliott Tool Technology produce an ultrasmooth, mirror-like surface finish on linear surfaces in a single pass. This cost-effective, easy-to-use tooling from Monaghan Tooling Group improves surface irregularities and tool marks, producing optimum surface finishes of 4-8 Ra. This proven technique can eliminate secondary processes such as grinding, honing and polishing by automating those processes in the primary CNC machine. Doing so saves setup and processing time and labor costs and also enhances machinery utilization and shop floor productivity.
Diamond burnishing is ideal for a variety of parts and ductile metals under 40 HRC, including steel, stainless steel, aluminum and cast iron. A cast iron shaft which started at a preburnished 67 Ra microinch surface finish yielded a 10 Ra microinch finish with a 0.0005” material compression in a single pass at 750 sfm. This was particularly helpful as the abrasive material was wearing inserts rapidly and attaining the desired part print was proving difficult.
Elliott diamond tools increase the surface hardness through the cold working process and compressive forces, and increase metal’s resistance to fatigue and failure at stress points while producing a dense and uniform surface. They are available in inch and metric slim-line, square, offset, on-center, stick and boring bar styles.
With cycle times that are measured in seconds rather than minutes, diamond burnishing allows companies to achieve a consistent mirror-like finish and replace hand polishing. Economical, long-lasting and replaceable wear parts reduce the total cost over the life of the tool. Wear parts are easy to replace, with common tooling available from stock. Their operation and maintenance requires minimal training.
Contact Details
Related Glossary Terms
- abrasive
abrasive
Substance used for grinding, honing, lapping, superfinishing and polishing. Examples include garnet, emery, corundum, silicon carbide, cubic boron nitride and diamond in various grit sizes.
- boring
boring
Enlarging a hole that already has been drilled or cored. Generally, it is an operation of truing the previously drilled hole with a single-point, lathe-type tool. Boring is essentially internal turning, in that usually a single-point cutting tool forms the internal shape. Some tools are available with two cutting edges to balance cutting forces.
- boring bar
boring bar
Essentially a cantilever beam that holds one or more cutting tools in position during a boring operation. Can be held stationary and moved axially while the workpiece revolves around it, or revolved and moved axially while the workpiece is held stationary, or a combination of these actions. Installed on milling, drilling and boring machines, as well as lathes and machining centers.
- burnishing
burnishing
Finishing method by means of compressing or cold-working the workpiece surface with carbide rollers called burnishing rolls or burnishers.
- cold working
cold working
Deforming metal plastically under conditions of temperature and strain rate that induce strain hardening. Working below the recrystallization temperature, which is usually, but not necessarily, above room temperature.
- computer numerical control ( CNC)
computer numerical control ( CNC)
Microprocessor-based controller dedicated to a machine tool that permits the creation or modification of parts. Programmed numerical control activates the machine’s servos and spindle drives and controls the various machining operations. See DNC, direct numerical control; NC, numerical control.
- fatigue
fatigue
Phenomenon leading to fracture under repeated or fluctuating stresses having a maximum value less than the tensile strength of the material. Fatigue fractures are progressive, beginning as minute cracks that grow under the action of the fluctuating stress.
- grinding
grinding
Machining operation in which material is removed from the workpiece by a powered abrasive wheel, stone, belt, paste, sheet, compound, slurry, etc. Takes various forms: surface grinding (creates flat and/or squared surfaces); cylindrical grinding (for external cylindrical and tapered shapes, fillets, undercuts, etc.); centerless grinding; chamfering; thread and form grinding; tool and cutter grinding; offhand grinding; lapping and polishing (grinding with extremely fine grits to create ultrasmooth surfaces); honing; and disc grinding.
- hardness
hardness
Hardness is a measure of the resistance of a material to surface indentation or abrasion. There is no absolute scale for hardness. In order to express hardness quantitatively, each type of test has its own scale, which defines hardness. Indentation hardness obtained through static methods is measured by Brinell, Rockwell, Vickers and Knoop tests. Hardness without indentation is measured by a dynamic method, known as the Scleroscope test.
- polishing
polishing
Abrasive process that improves surface finish and blends contours. Abrasive particles attached to a flexible backing abrade the workpiece.