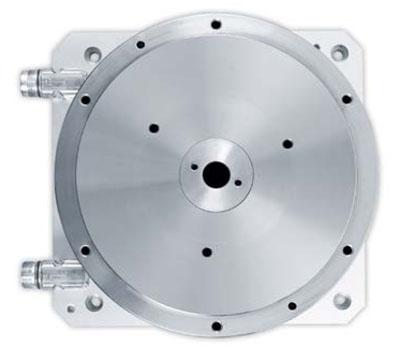
Werner Geissler GmbH has been producing precision turned parts for 40 years predominantly for the automobile and automotive supply industry. Where as speed is the name of the game in automotive suppliers market, Geissler recently sought out a solution to accellerate cycle times for a test bench that performed the final inspection of precision turned parts. At the heart of the system was a pneumatic rotary indexing table which had reached its limits and was no longer able to produce the desired shorter cycles.
The goal of Geissler's custom machine building department was to replace the existing pneumatic table with a more efficient electrical solution as the automotive industry demands that final inspection results need to be 100 percent.
WEISS and its' subsidiary WEISS North America Inc. reviewed Geissler's test system situation and recommended a conversion to its directly driven TO series rotary indexing table to drastically cut the cycle time.
At issue was the case for tension screws for the common rail injection systems for a specialist automotive supplier. The production from 25 CNC automatic lathes runs through a single test bench. A rotary indexing table feeds the components to the test stations, where cameras, lasers, and spreading fingers check the dimensions in 2.6-second cycles. If the machine fails, inspections need to be performed by hand, which is costly, time-consuming, and occurs approximately every four weeks.
This is when regular maintenance of the pneumatic rotary indexing table takes place as the short cycle times push the table to its mechanical limits. Additionally, after one month the shock absorbers and parts of the mechanics need to be replaced by Geissler's in-house custom machine building department; which also designed and built the test bench. This frequent maintenance was taken into account during the development as the rotary indexing table was kept easily accessible so that the shock absorber unit could be replaced quickly.
These collective factors lead Geissler to realize it was time to replace the entire rotary table. To achieve the required cycle times, the whole thing needed to be operated electronically, which is where WEISS came"
Initial WEISS consultation suggested a fixed-cycle, electro-mechanical rotary indexing table from their TC series. This would have easily halved the previous switching time of one second. Upon further investigation, the parties discovered that the direct drive, user programmable TO220C torque rotary indexing table with a switching time of just 0.3 seconds under current conditions was an optimal solution. This would cut the cycle time of the test bench from 2.6 seconds to 1.9, generating time-and-cost savings which would recoup the cost of the somewhat more expensive direct drive rotary indexing table within just three months.
Saving valuable cycle time wasn't the only benefit the TO delivered as fast indexing times, simple integration, and easy programming are all benchmarks. The TO direct drive rotary indexing table is also virtually maintenance free which eliminated the need to regularly replace the shock absorbers of the pneumatic rotary indexing table. Notably, as an electrical solution, savings would be achieved by eliminating time-consuming compressed air processing.
Installation of the TO presented advantages as the rotary indexing table is easily accessible and not the core element of the whole system, as often is the case. Although the programmable, gentle approach ramps of the TO eliminate the hard impacts caused by the pneumatics, some unpleasant oscillating motions did occur. The cause of this was quickly identified and remedied. The external arrangement of the rotary indexing table means that the whole construction acts like a torsion spring, which leads to unpleasant undulations because of the direct drive's larger dynamics. Bracing the substructure solves the problem.
Finally, Geissler's master electrician leveraged the WEISS Application Software (WAS) which enabled simple and intuitive commissioning of the system's most important parameters. The graphic user interface series also provided clear and in-depth programming with a faster (approximately 15 minutes) setup, and smooth operation, saving valuable time and cost. Additionally, it only took a few minutes to connect the inverter to the control system via the Profibus. The WAS also made it possible to optimise the approach ramps and further cut switching times.
The sum of these elements means that the test machine can get back to checking quality on schedule. For the test machines, the TO220C direct drive torque rotary indexing tables from WEISS proved to be far superior to the existing pneumatic tables when it came to the critical variables of speed, running costs, and absence of maintenance. Ultimately, the highly dynamic TO provided simple integration into the existing equipment, the shortest indexing times and the highest precision.
According to Christian Nemeth, Geissler's head of custom machine building, "The extremely fast cycle times and, in particular, the absence of maintenance of the direct drive WEISS rotary indexing tables were the reason for the conversion. The good service and active support during start-up also impressed us." Nemeth also noted that he's already decided that a test bench, which is still under construction, will be converted to a direct drive rotary indexing table. Additionally, he plans to design the next test bench on the basis of a TO from WEISS right from the outset.
Contact Details
Related Glossary Terms
- computer numerical control ( CNC)
computer numerical control ( CNC)
Microprocessor-based controller dedicated to a machine tool that permits the creation or modification of parts. Programmed numerical control activates the machine’s servos and spindle drives and controls the various machining operations. See DNC, direct numerical control; NC, numerical control.