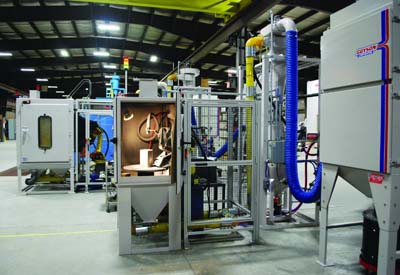
Guyson Corp. has extended its range of robotic surface treatment equipment to include a 7-axis direct pressure blast machine with a work envelope of 30 x 40 x 30 inches and a small overall footprint for lean, cell-based component processing.
A 6-axis robot is securely mounted on a rigidly welded pedestal attached to the rear of the blasting cabinet, so that the range of motion of the articulated arm can be used for manipulation of the pressure-blast nozzle. A sturdy safety barrier with an interlocked access door surrounds the back of the machine to exclude workers from the vicinity of the moving robot. The 24-inch diameter turntable of the rotary blast machine is servomotor driven and controlled as an auxiliary axis of robotic motion.
To isolate the robot from the potentially abrasive environment of the blast chamber, the rear wall opening in the blast enclosure is sealed by a custom-tailored skirt made from coated and laminated fabric, with a snug-fitting collar at the end of the arm. Side-hinged swing doors with safety interlocks are provided on the side and front of the robotic blast machine for the loading of parts and to allow inspection and maintenance access.
In operation, the precision robotic blast system is capable of constantly and accurately maintaining the correct blasting angle, stand-off distance and surface speed, even as it follows the contours of intricate-shaped components. This enables repeatable production of identical surface conditions from one area of the part to another and from part to part.
Part-holding fixtures can be quickly interchanged, positively located and locked in position by utilizing T-slots and guide pins in the rotary table. No other set-up or adjustment is normally required, because specific component orientation is included in the coordinated motion program for each different part, and other blasting process parameters, such as blast duration and pressure, can be stored and automatically recalled at will. The size and elaboration of the media reclamation and delivery elements of the robotic blast system depend on the requirements of the impact treatment application.
The smallest pressure-blast module is less than four feet in height and is hung on the blasting cabinet itself. For technical surface preparation, a 15-foot tall reclaim stack-up may be needed that includes a cyclone separator, a vibratory screen classifier and a pressure pot with the capacity to hold extra blast media. To maintain negative pressure in the blasting enclosure and balance the air flow for media reclamation, the robotic pressure-blast system is completed by a reverse pulsing cartridge-type dust collector with an extraction capacity of 1,000 cubic feet of air per minute.
Prospective users of automated or robotic blasting equipment are encouraged to submit sample components for free laboratory testing and application engineering evaluation at the blast machine builder's factory in northeastern New York State.
Contact Details
Related Glossary Terms
- abrasive
abrasive
Substance used for grinding, honing, lapping, superfinishing and polishing. Examples include garnet, emery, corundum, silicon carbide, cubic boron nitride and diamond in various grit sizes.
- work envelope
work envelope
Cube, sphere, cylinder or other physical space within which the cutting tool is capable of reaching.