Contact Details
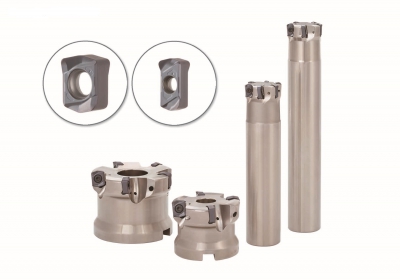
Tungaloy Corp. is continuously expanding its DoFeed series. The latest addition includes inserts in grade AH8015.
DoFeed is a high-feed milling cutter series with a close-pitched insert alignment, intended for various applications where an efficient removal of large stock is required, such as profiling and pocketing processes in die and mold shops. The double-sided insert geometry brings benefits in tool economy and productivity and has been earning customers’ confidence in recent years, according to the company.
The series already has an ample lineup of inserts and cutter bodies, intended for milling various materials including steel, stainless steel, cast iron, and heat-resistant superalloys. Backed by market requests for machining hard materials over HRC 50, a new insert line of the AH8015 grade now joins the product family.
AH8015 is a PVD grade with a coating composition of AlTiN. The multiple-layered coating configuration with high aluminum content improves resistance to chipping and built-up edge, improving machinability for smearing materials typically used in the die and mold industry. An extremely hard submicron carbide grade is used for the substrate for improved wear resistance.
Related Glossary Terms
- built-up edge ( BUE)
built-up edge ( BUE)
1. Permanently damaging a metal by heating to cause either incipient melting or intergranular oxidation. 2. In grinding, getting the workpiece hot enough to cause discoloration or to change the microstructure by tempering or hardening.
- gang cutting ( milling)
gang cutting ( milling)
Machining with several cutters mounted on a single arbor, generally for simultaneous cutting.
- machinability
machinability
The relative ease of machining metals and alloys.
- milling
milling
Machining operation in which metal or other material is removed by applying power to a rotating cutter. In vertical milling, the cutting tool is mounted vertically on the spindle. In horizontal milling, the cutting tool is mounted horizontally, either directly on the spindle or on an arbor. Horizontal milling is further broken down into conventional milling, where the cutter rotates opposite the direction of feed, or “up” into the workpiece; and climb milling, where the cutter rotates in the direction of feed, or “down” into the workpiece. Milling operations include plane or surface milling, endmilling, facemilling, angle milling, form milling and profiling.
- milling cutter
milling cutter
Loosely, any milling tool. Horizontal cutters take the form of plain milling cutters, plain spiral-tooth cutters, helical cutters, side-milling cutters, staggered-tooth side-milling cutters, facemilling cutters, angular cutters, double-angle cutters, convex and concave form-milling cutters, straddle-sprocket cutters, spur-gear cutters, corner-rounding cutters and slitting saws. Vertical cutters use shank-mounted cutting tools, including endmills, T-slot cutters, Woodruff keyseat cutters and dovetail cutters; these may also be used on horizontal mills. See milling.
- physical vapor deposition ( PVD)
physical vapor deposition ( PVD)
Tool-coating process performed at low temperature (500° C), compared to chemical vapor deposition (1,000° C). Employs electric field to generate necessary heat for depositing coating on a tool’s surface. See CVD, chemical vapor deposition.
- profiling
profiling
Machining vertical edges of workpieces having irregular contours; normally performed with an endmill in a vertical spindle on a milling machine or with a profiler, following a pattern. See mill, milling machine.
- superalloys
superalloys
Tough, difficult-to-machine alloys; includes Hastelloy, Inconel and Monel. Many are nickel-base metals.
- wear resistance
wear resistance
Ability of the tool to withstand stresses that cause it to wear during cutting; an attribute linked to alloy composition, base material, thermal conditions, type of tooling and operation and other variables.