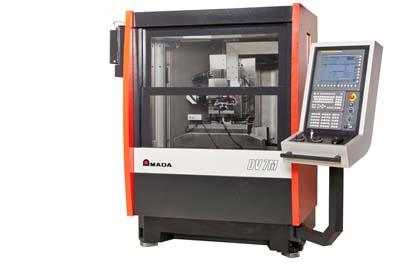
Amada Machine Tool America says its new DV-7M pulls no punches in exploiting advanced CNC, digital vision, mechanical accuracy, and versatility to produce tools at the extremes of quality and productivity. Exhaustively automated, with digital inspection, seven control axes and autoloading for both workpieces and grinding wheels, the modular machine automates grinding of the most complex and subtle tool profiles, moving, positioning and loading without human intervention or hesitation.
The DV-7M brings together several technologies used in the company's CNC profile grinders and surface grinders, and then adds some new ones. It's built on a vibration-damping polymer/mineral base, with active cooling, hydrostatic ways, linear motors and optional, modular tilt/swing/rotate machine elements for additional axes of simultaneous control. The range of possible workpieces extends from form-cutting tools to gear hobs; from cylindrical crush rolls to punches and dies. It will profile-grind, creep grind, or cylindrical-grind, with complex relief angles including logarithmic relief for hobs and other complex cutting tools.
Workpiece materials range from tool steel to graphite, from copper to carbides and ceramics. It's designed to use both CBN abrasive and diamond grinding wheels.
On the control end, the DV-7M is reportedly a tour-de-force of CNC, vision, and self-compensating technologies. A Fanuc 31 i-Model A (Panel i) provides control and CAM functions. After downloading a CAD file, the operator applies reliefs and related geometry to the basic part profile, using a Windows-interface, built-in CAM program at the machine tool CNC. Then, bringing optical profiling into the 21st century, the vision system eliminates the cumbersome charts, compares downloaded CAD files with the actual part profile, sets the swiveling wheel pivot point to the workpiece edge, then enables in-machine digital inspection of all components. As it is grinding, identifying departures from the nominal profile at high magnification and with digital precision, allowing wheel-wear compensation.
Workpieces have smooth, blended reliefs and rakes – overcoming a limitation of conventional CNC profile grinders. Where an EDM finish not satisfactory, this reciprocating CNC profile grinder will produce a superior tool with a smooth finish and sharp edges.
Contact Details
Related Glossary Terms
- abrasive
abrasive
Substance used for grinding, honing, lapping, superfinishing and polishing. Examples include garnet, emery, corundum, silicon carbide, cubic boron nitride and diamond in various grit sizes.
- ceramics
ceramics
Cutting tool materials based on aluminum oxide and silicon nitride. Ceramic tools can withstand higher cutting speeds than cemented carbide tools when machining hardened steels, cast irons and high-temperature alloys.
- computer numerical control ( CNC)
computer numerical control ( CNC)
Microprocessor-based controller dedicated to a machine tool that permits the creation or modification of parts. Programmed numerical control activates the machine’s servos and spindle drives and controls the various machining operations. See DNC, direct numerical control; NC, numerical control.
- computer-aided design ( CAD)
computer-aided design ( CAD)
Product-design functions performed with the help of computers and special software.
- computer-aided manufacturing ( CAM)
computer-aided manufacturing ( CAM)
Use of computers to control machining and manufacturing processes.
- cubic boron nitride ( CBN)
cubic boron nitride ( CBN)
Crystal manufactured from boron nitride under high pressure and temperature. Used to cut hard-to-machine ferrous and nickel-base materials up to 70 HRC. Second hardest material after diamond. See superabrasive tools.
- electrical-discharge machining ( EDM)
electrical-discharge machining ( EDM)
Process that vaporizes conductive materials by controlled application of pulsed electrical current that flows between a workpiece and electrode (tool) in a dielectric fluid. Permits machining shapes to tight accuracies without the internal stresses conventional machining often generates. Useful in diemaking.
- grinding
grinding
Machining operation in which material is removed from the workpiece by a powered abrasive wheel, stone, belt, paste, sheet, compound, slurry, etc. Takes various forms: surface grinding (creates flat and/or squared surfaces); cylindrical grinding (for external cylindrical and tapered shapes, fillets, undercuts, etc.); centerless grinding; chamfering; thread and form grinding; tool and cutter grinding; offhand grinding; lapping and polishing (grinding with extremely fine grits to create ultrasmooth surfaces); honing; and disc grinding.
- profiling
profiling
Machining vertical edges of workpieces having irregular contours; normally performed with an endmill in a vertical spindle on a milling machine or with a profiler, following a pattern. See mill, milling machine.
- relief
relief
Space provided behind the cutting edges to prevent rubbing. Sometimes called primary relief. Secondary relief provides additional space behind primary relief. Relief on end teeth is axial relief; relief on side teeth is peripheral relief.
- vision system
vision system
System in which information is extracted from visual sensors to allow machines to react to changes in the manufacturing process.