Contact Details
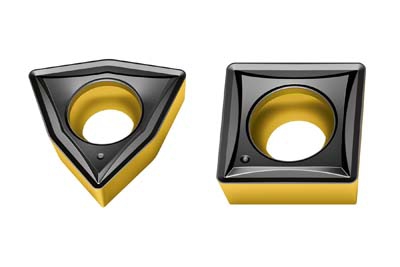
Walter has introduced E47, the versatile new counterboring insert geometry designed for use with the Walter BoringMEDIUM and Walter BoringMAXI tooling systems. Key to E47's high precision, process reliability and longer tool life is its excellent chip breaking and removal properties that result from its universal chip groove, positive rake angle, and strong cutting edge with zero°Chamfer, according to the company. Depending on the shape of the insert and its size, depths of cut from 2.5mm up to 6.3mm are no problem.
Chip forming and removal are important in any metalcutting operation but are particularly essential in counterboring, where excellent chip breaking is essential for ensuring the precise cylindricity and accurately formed steps required by subsequent finish machining operations. Though indexable inserts not specifically designed for this operation are often used when counterboring, precision and process reliability tend to suffer. For example, their curved cutting edges can quickly lead to shape deformations when step drilling. However, the straight cutting edge of the new E47 geometry produces precise dimensional accuracy even when step drilling. T
ooling costs are also reduced by the versatility of the new inserts. Aimed mainly at material groups ISO P and K, it also produces superior results with ISO M, ISO S, and with the PVD grades. In addition, though designed primarily for use with the Walter BoringMEDIUM system for drilled holes of 20 to 153mm and the Walter BoringMAXI tooling system for drilled holes of 150 to 640mm, the E47 indexable inserts can also be used in turning operations. This wide range of materials and applications allows users to reduce the number of insert geometries in their inventory, thus reducing costs.
Shapes CC, WC and SC are available in a variety of sizes and with different corner radii. As for grades, users can choose from WSM20 and WSM30 for ISO S, M and P applications, as well as WPP20 for ISO P and K applications.
Related Glossary Terms
- counterboring
counterboring
Enlarging one end of a drilled hole. The enlarged hole, which is concentric with the original hole, is flat on the bottom. Counterboring is used primarily to set bolt heads and nuts below the workpiece surface.
- metalcutting ( material cutting)
metalcutting ( material cutting)
Any machining process used to part metal or other material or give a workpiece a new configuration. Conventionally applies to machining operations in which a cutting tool mechanically removes material in the form of chips; applies to any process in which metal or material is removed to create new shapes. See metalforming.
- physical vapor deposition ( PVD)
physical vapor deposition ( PVD)
Tool-coating process performed at low temperature (500° C), compared to chemical vapor deposition (1,000° C). Employs electric field to generate necessary heat for depositing coating on a tool’s surface. See CVD, chemical vapor deposition.
- rake
rake
Angle of inclination between the face of the cutting tool and the workpiece. If the face of the tool lies in a plane through the axis of the workpiece, the tool is said to have a neutral, or zero, rake. If the inclination of the tool face makes the cutting edge more acute than when the rake angle is zero, the rake is positive. If the inclination of the tool face makes the cutting edge less acute or more blunt than when the rake angle is zero, the rake is negative.
- tungsten carbide ( WC)
tungsten carbide ( WC)
Intermetallic compound consisting of equal parts, by atomic weight, of tungsten and carbon. Sometimes tungsten carbide is used in reference to the cemented tungsten carbide material with cobalt added and/or with titanium carbide or tantalum carbide added. Thus, the tungsten carbide may be used to refer to pure tungsten carbide as well as co-bonded tungsten carbide, which may or may not contain added titanium carbide and/or tantalum carbide.
- turning
turning
Workpiece is held in a chuck, mounted on a face plate or secured between centers and rotated while a cutting tool, normally a single-point tool, is fed into it along its periphery or across its end or face. Takes the form of straight turning (cutting along the periphery of the workpiece); taper turning (creating a taper); step turning (turning different-size diameters on the same work); chamfering (beveling an edge or shoulder); facing (cutting on an end); turning threads (usually external but can be internal); roughing (high-volume metal removal); and finishing (final light cuts). Performed on lathes, turning centers, chucking machines, automatic screw machines and similar machines.