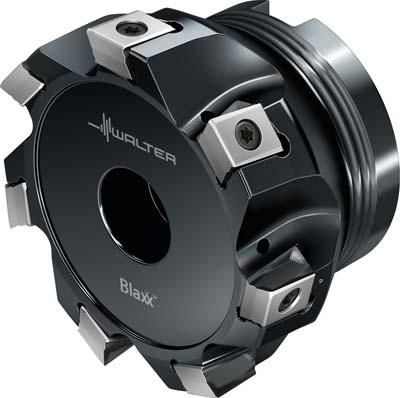
Walter USA LLC has introduced Blaxx, a new shoulder mill that reportedly combines precision, high metal removal rates and process reliability in a single tool, with a high-gloss black finish that is both wear and corrosion resistant.
The F5041 and F5141 shoulder mills, now available, feature highly precise indexable insert pockets that position the inserts accurately and securely. Add to this the fact that these tools are also fitted with tangential inserts that can not only increase the insert area presented to the workpiece but also enhance tool body stability, and you have a productive and highly robust tool characterized by quiet, low-vibration operation and exceptional process reliability.
These advantages are magnified by Walter's precision inserts. Manufactured in sizes LNHU0904 and LNHU1306, they have four cutting edges per insert that allow for low horsepower consumption and high metal removal rate. The highly controlled runout and concentricity of the body, and their precise 90 degree perpendicularity to the workpiece, ensure a high degree of accuracy.
Cutting depths of up to 12mm are possible with the larger LNHU1306 indexable insert. Since the insert pockets and chip clearances for the tangential inserts demand less material in the tool body, smaller tool diameters can be achieved, with higher density capabilities than with other mill designs.
The new Blaxx shoulder mills are available with diameters starting at 25mm. The higher density design enables up to 30 per cent higher feed rates.
Blaxx performance is further enhanced by the use of Tiger-tec Silver, Walter's new high performance coating. Tiger-tec Silver delivers both superior tool life and increased productivity thanks to its advanced properties, according to the company. These include increased high-temperature wear resistance with no loss of toughness. This combination of toughness and high wear resistance permits higher cutting speeds while also lengthening tool life.
Contact Details
Related Glossary Terms
- feed
feed
Rate of change of position of the tool as a whole, relative to the workpiece while cutting.
- indexable insert
indexable insert
Replaceable tool that clamps into a tool body, drill, mill or other cutter body designed to accommodate inserts. Most inserts are made of cemented carbide. Often they are coated with a hard material. Other insert materials are ceramic, cermet, polycrystalline cubic boron nitride and polycrystalline diamond. The insert is used until dull, then indexed, or turned, to expose a fresh cutting edge. When the entire insert is dull, it is usually discarded. Some inserts can be resharpened.
- milling machine ( mill)
milling machine ( mill)
Runs endmills and arbor-mounted milling cutters. Features include a head with a spindle that drives the cutters; a column, knee and table that provide motion in the three Cartesian axes; and a base that supports the components and houses the cutting-fluid pump and reservoir. The work is mounted on the table and fed into the rotating cutter or endmill to accomplish the milling steps; vertical milling machines also feed endmills into the work by means of a spindle-mounted quill. Models range from small manual machines to big bed-type and duplex mills. All take one of three basic forms: vertical, horizontal or convertible horizontal/vertical. Vertical machines may be knee-type (the table is mounted on a knee that can be elevated) or bed-type (the table is securely supported and only moves horizontally). In general, horizontal machines are bigger and more powerful, while vertical machines are lighter but more versatile and easier to set up and operate.
- wear resistance
wear resistance
Ability of the tool to withstand stresses that cause it to wear during cutting; an attribute linked to alloy composition, base material, thermal conditions, type of tooling and operation and other variables.