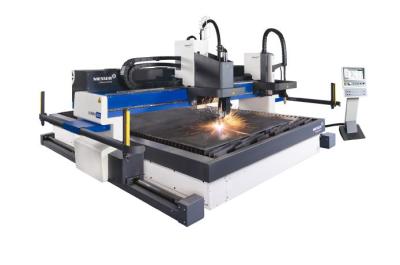
Versatility is also valued and demanded in an industrial setting, to be able to meet current and future requirements. Messer Cutting Systems GmbH from Groß-Umstadt has now created a truly all-inclusive package and the first cutting solution to meet this concept with their new ELEMENT platform. It shines not only in new design but, above all, with tempo, precision and productivity.
There are many suppliers of cutting systems in the market. However, only those who can present innovative concepts can succeed in winning customers. For this reason, Messer Cutting Systems GmbH, as solution supplier, continuously spotlights the market requirements in the search for ever better solutions which offer customers better value. This has resulted in the flexible machine platform ELEMENT: It combines high productivity and precision with individual configuration and updates. Thus, users are also able to take on future requirements and achieve a competitive edge.
“We have developed the new ELEMENT platform to offer our customers even more possibilities and flexibility, to configure all varieties of cutting process exactly to their individual requirements”, stresses John Emholz, President & CEO of Messer Cutting Systems Group. On top of that, the newest technology is incorporated in all components – for increased productivity, improved cut quality and shorter cycle times.
Machine control of the smart type
Today we can use a Smartphone almost in our sleep. So why not transfer what we have learned to value in daily life onto the control of a cutting machine? This was the thinking of the developers of the new CNC control Global Connect, so they integrated up to date touch operation and a modern interface into the current Human-Machine-Interface (HMI).
On this, Ingo Göller, CTO Global at Messer Cutting Systems: “Our vision was to make the complete operating procedure easier, faster, and above all, more reproducible. To achieve this, many innovations were integrated which makes the entire operation, and especially the preparation of the processing run, more intuitive, capable of automation and reliable, which means even first time users can start quickly. Naturally, we have also taken care that users of the conventional Global Control can still find their way around the new Global Connect at once.”
Although the operation and preparation of the operating process are very important and decisive phases, the operating process itself is most important in a machine. It is in just this area that Messer Cutting Systems places emphasis on fully automatic cycles and minimisation of non-productive times. To achieve this, almost all processes were thoroughly examined during the new development, reconsidered and drastically optimised.
To pave the way for a further networking, the Global Connect can now directly process production orders and achieve maximum productivity, especially when working with the products of the OmniFab family. The fact that the user interface stays clear and simply structured for this helps the user to call and operate all features without any problems.
Modular platform for individual solutions
A large selection of cutting and marking tools can be integrated here. “Is a solution with oxyfuel cutting and marking called for? Or rather the plasma process with a bevel head for fast cuts? With the ELEMENT our customer gets a previously non-existent flexibility to be able to configure their system exactly to their individual requirements”, says Jörg Mosser, Director Sales, Service & Marketing, Europe.
Tempo and precision perfectly united
When designing the new ELEMENT the developers did not just increase the performance of the machine but also went a step further: not only did they use the extensive engineering resources and experience of Messer Cutting Systems, to profit from their many years of successful machine development but also looked forwards to incorporate the latest technologies available now and predict future trends.
“The use of special components makes possible high accelerations and travel speeds in all axes. What is more, we have renewed the lifter, which speeds up the cutting process even more. With the intelligent torch sensing, processes can be optimised and unnecessary movements eliminated. This shortens cycle times and thus increases the overall productivity”, says Abraham Balendran, Product Manager at Messer Cutting Systems, Europe. And as good brakes belong to fast driving, the SureStop Sensor ensures that even at high speeds collisions are avoided.
However, speed is not the only area where the new ELEMENT can score points: Whether for complex contours, holes, or bevels for weld seam preparation – the new plasma bevel head which Messer Cutting Systems have developed especially for the ELEMENT platform can be used very flexibly. The torch permits accurate bevel cuts over a significant range of angles. The rotation with high acceleration ensures an efficient utilisation of the machine. The arc voltage automatically and precisely controls the torch height during the entire cut – for perfect results. For the new development of the bevel head the focus was also on function and low material wear.
The precision helical rack and pinion drive system of the ELEMENT also ensures even, vibration free motion, which improves the cut quality even more. Installation is quite simple, too: the rails are either mounted directly onto the floor of the production hall or on steel beams. This makes it flexible and saves costs.
Well networked
Alongside the high quality, robust system technology, it is also especially important that the machine can be smoothly integrated into the customer’s workflow. For this Messer offer a modular software solution which can be configured targeted on the varied requirements. “Our Software portfolio with the product families OmniWin and OmniFab model a complete digitalised production process right up to the machine and back”, states Roger Kilian-Kehr, CDO Global at Messer Cutting Systems.
The close networking of ERP systems and the Messer cutting unit makes it easier for the user to increase his overall productivity through a gain in transparency. “And, thanks to data which can be evaluated, allows the overall productivity to be evaluated objectively instead of having to rely on pure gut feeling. Thus, if necessary, the correct adjustments can be made to keep production continuously at the highest level”, adds Roger Kilian-Kehr.
The complete package brings the added value.
The ELEMENT cannot just do many things, but can also do them really well. “However, it is the interaction of all of our technologies, software and hardware solutions as well as our services which make the difference. With this total package our customers get the decisive added value and can establish a firm position in the fiercely contested market”, concludes John Emholz.
Contact Details
Related Glossary Terms
- computer numerical control ( CNC)
computer numerical control ( CNC)
Microprocessor-based controller dedicated to a machine tool that permits the creation or modification of parts. Programmed numerical control activates the machine’s servos and spindle drives and controls the various machining operations. See DNC, direct numerical control; NC, numerical control.