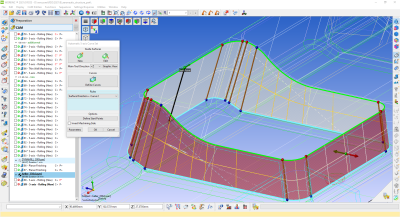
“On average, twice as fast. For some projects, four times faster.”
Those figures have been recorded for the enhanced Parallel Finishing toolpath in WORKNC 2021, which lets manufacturers use high-speed cutters of any shape, especially circle-segment tools such as barrel, lens and oval cutters.
WORKNC International Technical Manager Jean-Louis Humbert says, “This strategy is now on average twice as fast as the previous equivalents, Planar Finishing and Z-Level finishing. In certain projects, the calculation time difference was four times faster.”
Another important feature in the latest release of the software is the New Part centering/probing function, which generates pointset nodes for any inspection machine or direct CNC part inspection on a milling machine. Additionally, a new Probe Inspect command creates and exports control points in the CAM project to feed a probing system. There are also specific improvements to part centering tailored for CNC machines with table palletization.
The latest release builds on the popular fully-automatic 5-axis curve creation by splitting the steps when more complex curves are required. It also enhances the synchronization capabilities between each curve’s bottom and top limits.
Improvements to corner finishing with 5-axis rolling include being able to improve surface quality by using a cutting tool’s larger circle segment. “This 5-axis strategy can now change the contact point on the tool, ensuring optimal corner finishing with the tip of an oval tool,” Humbert says.
A new strategy – 5-Axis ISO Guiding – not only guides the toolpath by curves, but also by an underlying drive surface. It supports profiled cutters with advanced toolform technology, and new 5-axis blade finishing functionality allows profile cutter management based on new algorithms.
New items of functionality in WORKNC Designer – the specialist CAD-for-CAM 3D modelling module – include eight dedicated advanced analysis functions for interrogating, analyzing and validating CAD models: Compare, Draft Analysis, Edge Analysis, Altitude Analysis, Curvature Analysis, Face area Analysis, Thickness and Face type.
WORKNC Designer’s Reverse Engineering module allows imported scan data, either from files or directly by connecting to Hexagon scanners, to be converted into a refined mesh. The mesh data can then be used as it is, or as a reference for curve and surface creation, enabling mesh models to be fully reverse engineered to complete CAD or convergent models.
Contact Details
Related Glossary Terms
- centering
centering
1. Process of locating the center of a workpiece to be mounted on centers. 2. Process of mounting the workpiece concentric to the machine spindle. See centers.
- computer numerical control ( CNC)
computer numerical control ( CNC)
Microprocessor-based controller dedicated to a machine tool that permits the creation or modification of parts. Programmed numerical control activates the machine’s servos and spindle drives and controls the various machining operations. See DNC, direct numerical control; NC, numerical control.
- computer-aided design ( CAD)
computer-aided design ( CAD)
Product-design functions performed with the help of computers and special software.
- computer-aided manufacturing ( CAM)
computer-aided manufacturing ( CAM)
Use of computers to control machining and manufacturing processes.
- feed
feed
Rate of change of position of the tool as a whole, relative to the workpiece while cutting.
- gang cutting ( milling)
gang cutting ( milling)
Machining with several cutters mounted on a single arbor, generally for simultaneous cutting.
- milling
milling
Machining operation in which metal or other material is removed by applying power to a rotating cutter. In vertical milling, the cutting tool is mounted vertically on the spindle. In horizontal milling, the cutting tool is mounted horizontally, either directly on the spindle or on an arbor. Horizontal milling is further broken down into conventional milling, where the cutter rotates opposite the direction of feed, or “up” into the workpiece; and climb milling, where the cutter rotates in the direction of feed, or “down” into the workpiece. Milling operations include plane or surface milling, endmilling, facemilling, angle milling, form milling and profiling.
- milling machine ( mill)
milling machine ( mill)
Runs endmills and arbor-mounted milling cutters. Features include a head with a spindle that drives the cutters; a column, knee and table that provide motion in the three Cartesian axes; and a base that supports the components and houses the cutting-fluid pump and reservoir. The work is mounted on the table and fed into the rotating cutter or endmill to accomplish the milling steps; vertical milling machines also feed endmills into the work by means of a spindle-mounted quill. Models range from small manual machines to big bed-type and duplex mills. All take one of three basic forms: vertical, horizontal or convertible horizontal/vertical. Vertical machines may be knee-type (the table is mounted on a knee that can be elevated) or bed-type (the table is securely supported and only moves horizontally). In general, horizontal machines are bigger and more powerful, while vertical machines are lighter but more versatile and easier to set up and operate.
- parallel
parallel
Strip or block of precision-ground stock used to elevate a workpiece, while keeping it parallel to the worktable, to prevent cutter/table contact.
- toolpath( cutter path)
toolpath( cutter path)
2-D or 3-D path generated by program code or a CAM system and followed by tool when machining a part.