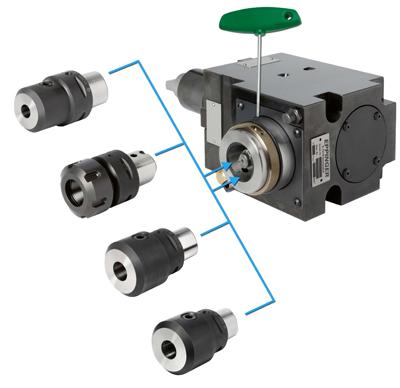
EXSYS Tool Inc. has introduced the EPPINGER CAPTO base holder, referring to it as "the world's smallest CAPTO interface with the fastest tool changeover times for enhancing efficiency and productivity in CNC turning operations."
When compared to traditional designs, the compact size of the EXSYS/EPPINGER CAPTO base holder provides more space for machining larger workpieces as well as offers improved torque transmission and rigidity for increased tool accuracy. The interface's cone-style shape further adds to the solution's precision and stiffness.
A special built-in release mechanism on the outer diameter if the EXSYS/EPPINGER CAPTO base holder's spindle provides optimal operator accessibility as well as makes it easy to lock and unlock the CAPTO adapters with a small Allen key for fast and virtually effortless tool changes. The automatic ejection of the CAPTO adapters also guarantees quick tool exchanges.
Available for bolt-on and VDI-style turrets, the EPPINGER/EXSYS CAPTO base holder accommodates fixed and rotary tools, including the EXSYS/EPPINGER PRECI-FLEX system, and accepts all standard CAPTO/PSC adapters. The same CAPTO adapters used in milling applications will now work in turning operations thanks to the versatility of the solution.
According to Scott Leitch, a representative for EXSYS Tool, for decades the EPPINGER name has been synonymous with innovation, precision and reliability, and its new CAPTO interface maintains the brand's premium legacy. "With the products superb rigidity, short tool changeover times and high accuracy, users will definitely experience enhanced productivity, profitability and an overall better machined component."
Contact Details
Related Glossary Terms
- computer numerical control ( CNC)
computer numerical control ( CNC)
Microprocessor-based controller dedicated to a machine tool that permits the creation or modification of parts. Programmed numerical control activates the machine’s servos and spindle drives and controls the various machining operations. See DNC, direct numerical control; NC, numerical control.
- gang cutting ( milling)
gang cutting ( milling)
Machining with several cutters mounted on a single arbor, generally for simultaneous cutting.
- milling
milling
Machining operation in which metal or other material is removed by applying power to a rotating cutter. In vertical milling, the cutting tool is mounted vertically on the spindle. In horizontal milling, the cutting tool is mounted horizontally, either directly on the spindle or on an arbor. Horizontal milling is further broken down into conventional milling, where the cutter rotates opposite the direction of feed, or “up” into the workpiece; and climb milling, where the cutter rotates in the direction of feed, or “down” into the workpiece. Milling operations include plane or surface milling, endmilling, facemilling, angle milling, form milling and profiling.
- outer diameter ( OD)
outer diameter ( OD)
Dimension that defines the exterior diameter of a cylindrical or round part. See ID, inner diameter.
- stiffness
stiffness
1. Ability of a material or part to resist elastic deflection. 2. The rate of stress with respect to strain; the greater the stress required to produce a given strain, the stiffer the material is said to be. See dynamic stiffness; static stiffness.
- turning
turning
Workpiece is held in a chuck, mounted on a face plate or secured between centers and rotated while a cutting tool, normally a single-point tool, is fed into it along its periphery or across its end or face. Takes the form of straight turning (cutting along the periphery of the workpiece); taper turning (creating a taper); step turning (turning different-size diameters on the same work); chamfering (beveling an edge or shoulder); facing (cutting on an end); turning threads (usually external but can be internal); roughing (high-volume metal removal); and finishing (final light cuts). Performed on lathes, turning centers, chucking machines, automatic screw machines and similar machines.