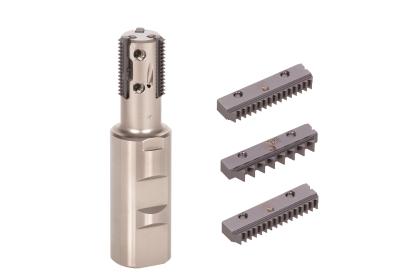
Tungaloy is introducing the ETTL model for ThreadMilling, an indexable thread milling tool series for efficient thread milling operations.
ThreadMilling incorporates cost-effective, double-sided inserts with two cutting edges. The tool allows efficient and precision production of various standard threads, such as ISO metric threads, Unified threads, and Whitworth parallel pipe threads, on modern CNC milling machines and machining centers, using helical interpolation programs. ThreadMilling provides a high level of security thanks to the light cutting load generated when the tool breaks the chip in smaller pieces, preventing chip from being jammed, which typically occurs during tapping.
New ETTL are available in tool diameters, ranging from 17 mm to 30 mm with flute counts of 2, 3 and 5. The insert clamping screws are embedded in the tool body so that the screws will not come loose when exchanging the inserts, eliminating the concerns of dismantling or losing the screws. In addition, the clamping force of the insert screws are enhanced over that of the existing ETLN style, allowing higher feed rates to be applied with improved cutting performance. Customers can continue to use the same CNC programs that are being used for the existing ETLN style.
At a Glance:
Able to thread mill ISO metric threads, Unified threads, and Whitworth parallel pipe threads
Double-sided insert with two cutting edges
Embedded insert clamping screws to facilitate insert exchanges, which prevents from losing the screws
Higher insert clamping design allows applications of high feed rates for improved cutting performance
Same CNC programs can be used as with ETLN-style ThreadMilling
Nine cutter bodies and nine inserts to be introduced
Contact Details
Related Glossary Terms
- centers
centers
Cone-shaped pins that support a workpiece by one or two ends during machining. The centers fit into holes drilled in the workpiece ends. Centers that turn with the workpiece are called “live” centers; those that do not are called “dead” centers.
- computer numerical control ( CNC)
computer numerical control ( CNC)
Microprocessor-based controller dedicated to a machine tool that permits the creation or modification of parts. Programmed numerical control activates the machine’s servos and spindle drives and controls the various machining operations. See DNC, direct numerical control; NC, numerical control.
- feed
feed
Rate of change of position of the tool as a whole, relative to the workpiece while cutting.
- gang cutting ( milling)
gang cutting ( milling)
Machining with several cutters mounted on a single arbor, generally for simultaneous cutting.
- interpolation
interpolation
Process of generating a sufficient number of positioning commands for the servomotors driving the machine tool so the path of the tool closely approximates the ideal path. See CNC, computer numerical control; NC, numerical control.
- milling
milling
Machining operation in which metal or other material is removed by applying power to a rotating cutter. In vertical milling, the cutting tool is mounted vertically on the spindle. In horizontal milling, the cutting tool is mounted horizontally, either directly on the spindle or on an arbor. Horizontal milling is further broken down into conventional milling, where the cutter rotates opposite the direction of feed, or “up” into the workpiece; and climb milling, where the cutter rotates in the direction of feed, or “down” into the workpiece. Milling operations include plane or surface milling, endmilling, facemilling, angle milling, form milling and profiling.
- milling machine ( mill)
milling machine ( mill)
Runs endmills and arbor-mounted milling cutters. Features include a head with a spindle that drives the cutters; a column, knee and table that provide motion in the three Cartesian axes; and a base that supports the components and houses the cutting-fluid pump and reservoir. The work is mounted on the table and fed into the rotating cutter or endmill to accomplish the milling steps; vertical milling machines also feed endmills into the work by means of a spindle-mounted quill. Models range from small manual machines to big bed-type and duplex mills. All take one of three basic forms: vertical, horizontal or convertible horizontal/vertical. Vertical machines may be knee-type (the table is mounted on a knee that can be elevated) or bed-type (the table is securely supported and only moves horizontally). In general, horizontal machines are bigger and more powerful, while vertical machines are lighter but more versatile and easier to set up and operate.
- parallel
parallel
Strip or block of precision-ground stock used to elevate a workpiece, while keeping it parallel to the worktable, to prevent cutter/table contact.
- tapping
tapping
Machining operation in which a tap, with teeth on its periphery, cuts internal threads in a predrilled hole having a smaller diameter than the tap diameter. Threads are formed by a combined rotary and axial-relative motion between tap and workpiece. See tap.