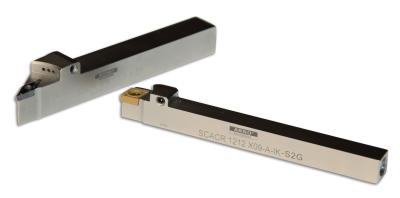
Arno Werkzeuge USA has expanded its Swiss-style program of cutting tools, holders, inserts and through-coolant systems for Swiss CNC auto lathes. Applications for Swiss auto lathes are known for their unique machining requirements for extremely long, thin, small parts with great precision and accuracy and, therefore, require very specific tooling.
ARNO Werkzeuge has designed and manufactured cutting tools specifically for CNC Swiss auto lathes. Its offering of Swiss-style tooling extends across its entire family of products for grooving, turning, milling and drilling operations.
Arno USA’s SA holders and inserts features a modular grooving system with a single basic toolholder, which turns into different tool variants by simply changing the support blade and clamp and is popular for grooving and parting-off operations. The Arno Swiss program applies to specific area of the SA line with its HSA-U holder range. Typically, with most holders, the clamping screw is on the top of the unit. However, with HSA-U the clamp features a clamp and screw that mounts on the bottom of the holders. This offers easy handling and clamping for the tighter spacing and machining requirements of Swiss-style auto lathes. The SA range also includes the standard HSA monoblock holder with the clamp on top.
Typically, Swiss-style lathes have smaller machining requirements and utilize bar sizes of no larger than 1¼” in diameter. For ARNO’s SA Swiss-style program, insert widths starting from 0.059” (1.5 mm). Shank sizes ranging from 3/8” (8 mm) up to ¾” (20 mm). Another unique feature of ARNO’s Swiss-style program for the SA range includes through-coolant tooling capabilities with sizes starting from 0.079” (2 mm).
Contact Details
Related Glossary Terms
- computer numerical control ( CNC)
computer numerical control ( CNC)
Microprocessor-based controller dedicated to a machine tool that permits the creation or modification of parts. Programmed numerical control activates the machine’s servos and spindle drives and controls the various machining operations. See DNC, direct numerical control; NC, numerical control.
- gang cutting ( milling)
gang cutting ( milling)
Machining with several cutters mounted on a single arbor, generally for simultaneous cutting.
- grooving
grooving
Machining grooves and shallow channels. Example: grooving ball-bearing raceways. Typically performed by tools that are capable of light cuts at high feed rates. Imparts high-quality finish.
- milling
milling
Machining operation in which metal or other material is removed by applying power to a rotating cutter. In vertical milling, the cutting tool is mounted vertically on the spindle. In horizontal milling, the cutting tool is mounted horizontally, either directly on the spindle or on an arbor. Horizontal milling is further broken down into conventional milling, where the cutter rotates opposite the direction of feed, or “up” into the workpiece; and climb milling, where the cutter rotates in the direction of feed, or “down” into the workpiece. Milling operations include plane or surface milling, endmilling, facemilling, angle milling, form milling and profiling.
- shank
shank
Main body of a tool; the portion of a drill or similar end-held tool that fits into a collet, chuck or similar mounting device.
- toolholder
toolholder
Secures a cutting tool during a machining operation. Basic types include block, cartridge, chuck, collet, fixed, modular, quick-change and rotating.
- turning
turning
Workpiece is held in a chuck, mounted on a face plate or secured between centers and rotated while a cutting tool, normally a single-point tool, is fed into it along its periphery or across its end or face. Takes the form of straight turning (cutting along the periphery of the workpiece); taper turning (creating a taper); step turning (turning different-size diameters on the same work); chamfering (beveling an edge or shoulder); facing (cutting on an end); turning threads (usually external but can be internal); roughing (high-volume metal removal); and finishing (final light cuts). Performed on lathes, turning centers, chucking machines, automatic screw machines and similar machines.