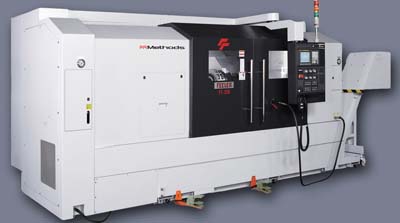
Methods Machine Tools Inc. has introduced FEELER FT-Series High Performance CNC Turning Centers featuring a new all-boxway design to significantly increase cutting capacity.
"For increased productivity, the new FT-Series design provides customers with exceptional cutting capacity," said Paul Hurtig, FEELER Product Manager, Methods Machine Tools Inc. "Methods' engineers have incorporated new features for unsurpassed performance and value."
The FEELER FT-Series includes four models: FT-200, FT-250, FT-350 and FT-350L. For rigidity when performing heavy duty cutting, each of the models has a single-piece structure with boxways, 45-degree slant bed and robust base. For maximum integrity, FEA analysis is used to ensure a solid machine base with excellent overall structural rigidity and stability.
Additional new design features include a more rigid Z-Axis and tailstock rail for maximum support and accurate tracking. The FT-Series includes a new spindle head stock with a FEELER sleeve-type spindle, and the latest high-rigidity servo turret including clamping with curvic coupling for stable and swift tool changes. For excellent multitasking capabilities, 7 ½ HP milling motor with 51.6ft-lb torque is provided.
FEELER FT-Series from Methods offer a reliable FANUC 0i-TD control and 12-station turret. Customers can choose from four different gear boxes and two spindle types. Spindles range from 2,500 rpm to 4,500 rpm and offer chuck diameter sizes from 8" (210mm) up to 15" (381mm). Bar capacity ranges from 2.6" (65mm) to 4.5" (115mm). Maximum turning diameter is offered from 13.0" (330mm) to 25.0" (620mm) and maximum turning length from 21" (530mm) to 60.2" (1,530mm). Machine weight ranges from 9,925 lbs (4,500 kg) to 21,500 lbs (9,750 kg), depending on the model. A BMT-65 tool system features a solid interface for tool holding. Servo programmable tailstock is standard.
For maximum machine component longevity, a fully enclosed CE cabinet prevents dust and fumes from entering. The Methods-FEELER CNC Lathes and Turning Centers include the HT-Series, FTC-Series and FT-Series. The full range of FEELER machines encompasses Vertical Machining Centers, Turning Centers, Bridge Mills and Boring Mills.
Contact Details
Related Glossary Terms
- boring
boring
Enlarging a hole that already has been drilled or cored. Generally, it is an operation of truing the previously drilled hole with a single-point, lathe-type tool. Boring is essentially internal turning, in that usually a single-point cutting tool forms the internal shape. Some tools are available with two cutting edges to balance cutting forces.
- centers
centers
Cone-shaped pins that support a workpiece by one or two ends during machining. The centers fit into holes drilled in the workpiece ends. Centers that turn with the workpiece are called “live” centers; those that do not are called “dead” centers.
- chuck
chuck
Workholding device that affixes to a mill, lathe or drill-press spindle. It holds a tool or workpiece by one end, allowing it to be rotated. May also be fitted to the machine table to hold a workpiece. Two or more adjustable jaws actually hold the tool or part. May be actuated manually, pneumatically, hydraulically or electrically. See collet.
- computer numerical control ( CNC)
computer numerical control ( CNC)
Microprocessor-based controller dedicated to a machine tool that permits the creation or modification of parts. Programmed numerical control activates the machine’s servos and spindle drives and controls the various machining operations. See DNC, direct numerical control; NC, numerical control.
- gang cutting ( milling)
gang cutting ( milling)
Machining with several cutters mounted on a single arbor, generally for simultaneous cutting.
- milling
milling
Machining operation in which metal or other material is removed by applying power to a rotating cutter. In vertical milling, the cutting tool is mounted vertically on the spindle. In horizontal milling, the cutting tool is mounted horizontally, either directly on the spindle or on an arbor. Horizontal milling is further broken down into conventional milling, where the cutter rotates opposite the direction of feed, or “up” into the workpiece; and climb milling, where the cutter rotates in the direction of feed, or “down” into the workpiece. Milling operations include plane or surface milling, endmilling, facemilling, angle milling, form milling and profiling.
- turning
turning
Workpiece is held in a chuck, mounted on a face plate or secured between centers and rotated while a cutting tool, normally a single-point tool, is fed into it along its periphery or across its end or face. Takes the form of straight turning (cutting along the periphery of the workpiece); taper turning (creating a taper); step turning (turning different-size diameters on the same work); chamfering (beveling an edge or shoulder); facing (cutting on an end); turning threads (usually external but can be internal); roughing (high-volume metal removal); and finishing (final light cuts). Performed on lathes, turning centers, chucking machines, automatic screw machines and similar machines.