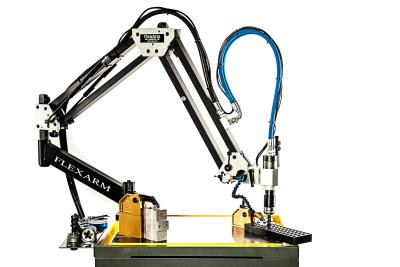
FlexArm Inc. introduces a mobile tapping package which yields mobility, productivity and efficiency by allowing operators to tap holes offline while the machining center works on the next part. This comprehensive package includes the FlexArm GH-18-1 tapping arm with a tap capacity of #6 to 5/8”, a reach from 17”-72”, variable speed from 100-420 rpm, 360-degree movement, and a semiautomatic tap lubricator.
Additionally, with a caster cart, power pack, tap stand and five tap holders, this hydraulic tool can be used wherever there is 110V available – with no air needed. With fast set up times and significantly reduced tap breakage, FlexArm tapping arms are an alternative to tapping holes manually or via CNC.
FlexArm provides a more efficient way to tap holes. They allow machining centers to do what they do best – milling, drilling and boring. When operators load a machining center and start its cycle, they can use that cycle time to tap previously machined parts with the FlexArm – yielding more productivity per shift. Tap breakage rates are significantly reduced with the FlexArm due to its purpose-centered approach. With a tap breakage rate of 1 per 3,000 holes versus 1 per 300 holes on a CNC, FlexArm tapping arms can significantly reduce setup time, cost and scrap rates.
In addition to the GH-18-1 model detailed above, other hydraulic and pneumatic versions of the FlexArm are available to suit varied tapping requirements. Engineers are available to discuss unique project parameters and offer solutions based on decades of experience. A 30-day free trial period allows FlexArm products to be proven in-plant under actual production conditions. They stock an extensive array of tap holders and repair parts in their Wapakoneta factory, for fast shipment, often same-day.
Contact Details
Related Glossary Terms
- boring
boring
Enlarging a hole that already has been drilled or cored. Generally, it is an operation of truing the previously drilled hole with a single-point, lathe-type tool. Boring is essentially internal turning, in that usually a single-point cutting tool forms the internal shape. Some tools are available with two cutting edges to balance cutting forces.
- centers
centers
Cone-shaped pins that support a workpiece by one or two ends during machining. The centers fit into holes drilled in the workpiece ends. Centers that turn with the workpiece are called “live” centers; those that do not are called “dead” centers.
- computer numerical control ( CNC)
computer numerical control ( CNC)
Microprocessor-based controller dedicated to a machine tool that permits the creation or modification of parts. Programmed numerical control activates the machine’s servos and spindle drives and controls the various machining operations. See DNC, direct numerical control; NC, numerical control.
- gang cutting ( milling)
gang cutting ( milling)
Machining with several cutters mounted on a single arbor, generally for simultaneous cutting.
- machining center
machining center
CNC machine tool capable of drilling, reaming, tapping, milling and boring. Normally comes with an automatic toolchanger. See automatic toolchanger.
- milling
milling
Machining operation in which metal or other material is removed by applying power to a rotating cutter. In vertical milling, the cutting tool is mounted vertically on the spindle. In horizontal milling, the cutting tool is mounted horizontally, either directly on the spindle or on an arbor. Horizontal milling is further broken down into conventional milling, where the cutter rotates opposite the direction of feed, or “up” into the workpiece; and climb milling, where the cutter rotates in the direction of feed, or “down” into the workpiece. Milling operations include plane or surface milling, endmilling, facemilling, angle milling, form milling and profiling.
- tap
tap
Cylindrical tool that cuts internal threads and has flutes to remove chips and carry tapping fluid to the point of cut. Normally used on a drill press or tapping machine but also may be operated manually. See tapping.
- tapping
tapping
Machining operation in which a tap, with teeth on its periphery, cuts internal threads in a predrilled hole having a smaller diameter than the tap diameter. Threads are formed by a combined rotary and axial-relative motion between tap and workpiece. See tap.