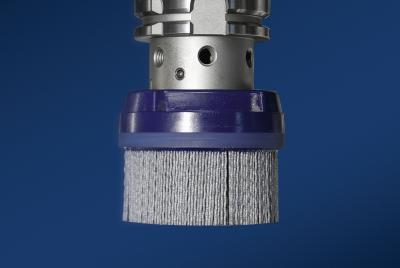
The new GARANT disc brushes from the Hoffmann Group are designed to boost efficiency and enhance precision during the finishing process. These high-tech brushes are suitable for direct application in a CNC machine or a robot cell, providing an automated way of finishing workpieces immediately after the machining process – with reproducible, reliable results. That means less time spent on setup and improved throughput.
The Hoffmann Group has designed its new GARANT disc brushes for precise deburring, edge filleting and surface finishing of milled, flat precision parts. Applied immediately after the machining process, they reliably remove unwanted burrs and fine milling marks. The tools are also suitable for precisely brushing down workpieces that have been produced using a sintering, punching, die casting or pressing process, and for creating smooth surfaces.
With GARANT disc brushes, even finishing valve plates with internal labyrinths is reportedly a breeze. And thanks to their maximum-density yet flexible bristles, they are able to deburr complex components without manipulating their shape. The nylon bristles, which are firmly cast in place and impregnated with abrasive grit, will not break off even at high speeds and produce a strong, consistent brushing effect due to the high proportion of abrasive grit they contain. That means burr-free, smoothly ground surfaces plus an exceptionally long service life and controllable wear behavior.
GARANT disc brushes are particularly well suited to wet machining and are compatible with all measuring head and combination face mill adapters. If required, the Hoffmann Group can also provide customers with disc brushes adapted specifically to suit their needs. The existing range of GARANT disc brushes will soon be expanded to include circular brushes for deburring work on outer surfaces.
Contact Details
Related Glossary Terms
- abrasive
abrasive
Substance used for grinding, honing, lapping, superfinishing and polishing. Examples include garnet, emery, corundum, silicon carbide, cubic boron nitride and diamond in various grit sizes.
- brushing
brushing
Generic term for a curve whose shape is controlled by a combination of its control points and knots (parameter values). The placement of the control points is controlled by an application-specific combination of order, tangency constraints and curvature requirements. See NURBS, nonuniform rational B-splines.
- computer numerical control ( CNC)
computer numerical control ( CNC)
Microprocessor-based controller dedicated to a machine tool that permits the creation or modification of parts. Programmed numerical control activates the machine’s servos and spindle drives and controls the various machining operations. See DNC, direct numerical control; NC, numerical control.
- die casting
die casting
Casting process wherein molten metal is forced under high pressure into the cavity of a metal mold.
- flat ( screw flat)
flat ( screw flat)
Flat surface machined into the shank of a cutting tool for enhanced holding of the tool.
- gang cutting ( milling)
gang cutting ( milling)
Machining with several cutters mounted on a single arbor, generally for simultaneous cutting.
- milling
milling
Machining operation in which metal or other material is removed by applying power to a rotating cutter. In vertical milling, the cutting tool is mounted vertically on the spindle. In horizontal milling, the cutting tool is mounted horizontally, either directly on the spindle or on an arbor. Horizontal milling is further broken down into conventional milling, where the cutter rotates opposite the direction of feed, or “up” into the workpiece; and climb milling, where the cutter rotates in the direction of feed, or “down” into the workpiece. Milling operations include plane or surface milling, endmilling, facemilling, angle milling, form milling and profiling.
- milling machine ( mill)
milling machine ( mill)
Runs endmills and arbor-mounted milling cutters. Features include a head with a spindle that drives the cutters; a column, knee and table that provide motion in the three Cartesian axes; and a base that supports the components and houses the cutting-fluid pump and reservoir. The work is mounted on the table and fed into the rotating cutter or endmill to accomplish the milling steps; vertical milling machines also feed endmills into the work by means of a spindle-mounted quill. Models range from small manual machines to big bed-type and duplex mills. All take one of three basic forms: vertical, horizontal or convertible horizontal/vertical. Vertical machines may be knee-type (the table is mounted on a knee that can be elevated) or bed-type (the table is securely supported and only moves horizontally). In general, horizontal machines are bigger and more powerful, while vertical machines are lighter but more versatile and easier to set up and operate.
- sintering
sintering
Bonding of adjacent surfaces in a mass of particles by molecular or atomic attraction on heating at high temperatures below the melting temperature of any constituent in the material. Sintering strengthens and increases the density of a powder mass and recrystallizes powder metals.