Contact Details
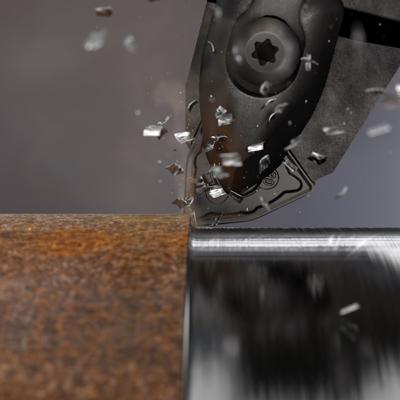
Sandvik Coromant has introduced two new grades for machining cast iron. GC3225 and GC3210 form a new insert grade chain covering all cast iron turning operations for both grey and nodular cast iron materials.
GC3225 is a first choice grade for the cast iron turning application area. It is designed to provide secure and trouble-free machining even in the most difficult conditions.
GC3210 is a grade with high flank wear resistance suitable for turning in all cast iron materials, in good to average machining conditions. It enhances reliability and productivity in intermittent cuts, high cutting speeds, wet or dry machining, machined surface or light cast skin.
To provide the edge-line security and wear resistance necessary to optimize performance, GC3225 and GC3210 feature a CVD coating combined with a fine-grained hard substrate. Additionally, their innovative design utilizes optimized micro-geometries to facilitate light cutting action, hence reducing cutting forces and improving tool life.
The results of tests conducted at customers have shown remarkable results. GC3225 has more to give when other inserts reach the end of their life. By using the insert in machining of nodular cast iron it was possible to increase tool life by 70 percent compared to a competitor grade. GC3210 has been tested in the machining of differential case covers with some outstanding results. After changing to GC3210 instead of a competitor grade, it was possible to increase tool life by 38 percent.
Related Glossary Terms
- chemical vapor deposition ( CVD)
chemical vapor deposition ( CVD)
High-temperature (1,000° C or higher), atmosphere-controlled process in which a chemical reaction is induced for the purpose of depositing a coating 2µm to 12µm thick on a tool’s surface. See coated tools; PVD, physical vapor deposition.
- flank wear
flank wear
Reduction in clearance on the tool’s flank caused by contact with the workpiece. Ultimately causes tool failure.
- turning
turning
Workpiece is held in a chuck, mounted on a face plate or secured between centers and rotated while a cutting tool, normally a single-point tool, is fed into it along its periphery or across its end or face. Takes the form of straight turning (cutting along the periphery of the workpiece); taper turning (creating a taper); step turning (turning different-size diameters on the same work); chamfering (beveling an edge or shoulder); facing (cutting on an end); turning threads (usually external but can be internal); roughing (high-volume metal removal); and finishing (final light cuts). Performed on lathes, turning centers, chucking machines, automatic screw machines and similar machines.
- wear resistance
wear resistance
Ability of the tool to withstand stresses that cause it to wear during cutting; an attribute linked to alloy composition, base material, thermal conditions, type of tooling and operation and other variables.