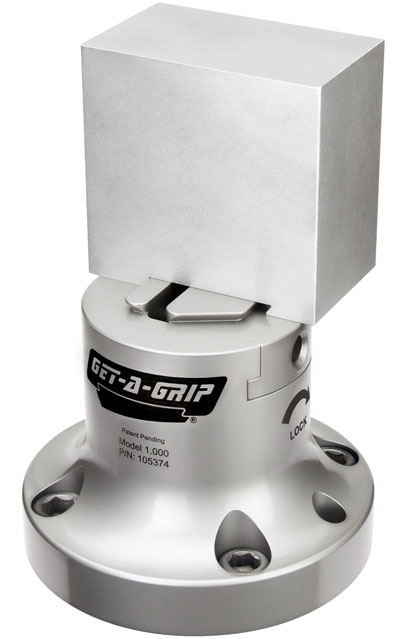
AMT Innovations offers a state-of-the-art workholding product, Get-A-Grip. The new cutting-edge triangular dovetail will never distort or deform the workpiece. The dovetail provides three evenly spaced, radial force vectors for superior gripping. Through carefully thought out triangular contact geometry, this product eliminates the need for an indexing pen. The pioneering internal clamping geometry reduces material preparation area and can be strategically placed where the finished part may have a pocket, which greatly reduces secondary operations.
The use of robust materials and innovative design elements bring flexibility and time-saving benefits to the company’s customers, which will reportedly result in a dramatic increase in production and profits.
Multiple product options allow users to apply this technology to palletized 4-axis horizontal CNC mills with tombstones, 5-axis CNC machines as well as CMM fixtures. Although many shops may not have 4 or 5 axis capabilities, AMT's Get-A-Grip also offers many advantages for common 3-axis CNC machining work and even 2-axis CNC turning. The recommended maximum workpiece is 5″ x 5″ x 5″ for Get-A-Grip Size 1.000 when using a single fixture. It is possible to hold a larger workpiece when using multiple fixtures.
Contact Details
Related Glossary Terms
- computer numerical control ( CNC)
computer numerical control ( CNC)
Microprocessor-based controller dedicated to a machine tool that permits the creation or modification of parts. Programmed numerical control activates the machine’s servos and spindle drives and controls the various machining operations. See DNC, direct numerical control; NC, numerical control.
- fixture
fixture
Device, often made in-house, that holds a specific workpiece. See jig; modular fixturing.
- turning
turning
Workpiece is held in a chuck, mounted on a face plate or secured between centers and rotated while a cutting tool, normally a single-point tool, is fed into it along its periphery or across its end or face. Takes the form of straight turning (cutting along the periphery of the workpiece); taper turning (creating a taper); step turning (turning different-size diameters on the same work); chamfering (beveling an edge or shoulder); facing (cutting on an end); turning threads (usually external but can be internal); roughing (high-volume metal removal); and finishing (final light cuts). Performed on lathes, turning centers, chucking machines, automatic screw machines and similar machines.