Contact Details
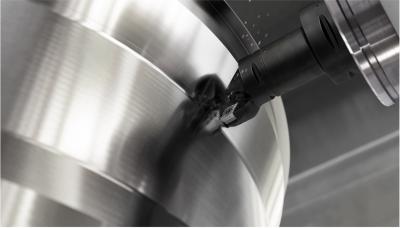
Global metal cutting leader Sandvik Coromant has introduced two new PVD insert grades, GC1205 and GC1210. Both grades enable secure, high-precision turning of aged nickel-based HRSA.
When turning aero-engine components, the surface requirements are high but no longer difficult to achieve, thanks to the new insert grades GC1205 and GC1210. Together, they cover a large application area within last-stage machining (LSM) and intermediate-stage machining (ISM).
There are several key features that help in working with the high-level performance of heat-resistant superalloy (HRSA) materials. A hard, fine-grained new substrate, the latest physical vapor deposition (PVD) coating technology and optimized edge-line integrity provide increased flank wear and secondary notch wear resistance, superior edge-line security and reduced flaking.
“For our customers, this translates into possibilities to run the inserts at higher cutting speeds with GC1205 and increased tool life with GC1210. Additionally, it ensures consistent and predictable tool life while reaching the required surface integrity demands for critical aerospace components,” said Martin Saunders, global product application specialist for turning at Sandvik Coromant.
Typical aero-engine components that the grades can machine are gas turbine discs, casings, blisks, spools, shafts and blades. But these grades also prove to be a great choice in demanding applications such as power generation turbines and medical implants made of cobalt-chrome. Martin Saunders continues: “The release of these two new grades offers the opportunity to increase cutting data while also prolonging tool life predominantly in last-stage machining and intermediate-stage machining of aerospace and medical components.”
The grades complement each other thanks to an overlap in the assortment. GC1205 is a finishing grade for machined surfaces in LSM and ISM applications. GC1210 complements GC1205 when more toughness is required and is mainly used in ISM applications for non-machined surfaces.
Related Glossary Terms
- flank wear
flank wear
Reduction in clearance on the tool’s flank caused by contact with the workpiece. Ultimately causes tool failure.
- physical vapor deposition ( PVD)
physical vapor deposition ( PVD)
Tool-coating process performed at low temperature (500° C), compared to chemical vapor deposition (1,000° C). Employs electric field to generate necessary heat for depositing coating on a tool’s surface. See CVD, chemical vapor deposition.
- physical vapor deposition ( PVD)2
physical vapor deposition ( PVD)
Tool-coating process performed at low temperature (500° C), compared to chemical vapor deposition (1,000° C). Employs electric field to generate necessary heat for depositing coating on a tool’s surface. See CVD, chemical vapor deposition.
- turning
turning
Workpiece is held in a chuck, mounted on a face plate or secured between centers and rotated while a cutting tool, normally a single-point tool, is fed into it along its periphery or across its end or face. Takes the form of straight turning (cutting along the periphery of the workpiece); taper turning (creating a taper); step turning (turning different-size diameters on the same work); chamfering (beveling an edge or shoulder); facing (cutting on an end); turning threads (usually external but can be internal); roughing (high-volume metal removal); and finishing (final light cuts). Performed on lathes, turning centers, chucking machines, automatic screw machines and similar machines.
- wear resistance
wear resistance
Ability of the tool to withstand stresses that cause it to wear during cutting; an attribute linked to alloy composition, base material, thermal conditions, type of tooling and operation and other variables.
Additional Products from Sandvik Coromant Co.
Pagination
- First page
- Previous page
- …
- 5
- 6
- 7
- 8
- 9
- 10
- 11
- 12
- 13