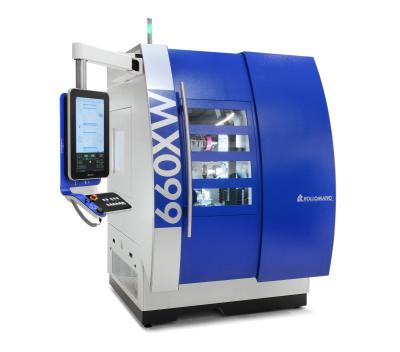
Rollomatic, a leading machine tool manufacturer based in Le Landeron, Switzerland, maintains its global leadership position in the field of multiaxis CNC grinding by launching a brand new hybrid model for combination grinding of tool geometries as well as peel grinding for neck, plunge and other blank prep operations.
The new GrindSmart 660XW is a 6-axis tool and peel grinding machine. It allows the user to utilize cost-effective and advanced lean manufacturing principles; termed as “Ultra-Lean Grinding Process.” The machine includes a 6•position wheel changer and linear motors on all axes.
Workhead: It features a traveling high-speed workhead. Peel grinding for blank prepara•on and neck grinding are included in the same chucking.
Peel grinding: Blank prepara•on for common-shank rotary cutting tools, neck grinding for long-reach mold & die endmills and plunge grinding operations can be performed.
Steady rest: This machine includes an innova•ve steady rest systems designed for grinding endmills as well as for drill point grinding.
Spindle motor: The grinding spindle is synchronous and is rated 20 hp.
Thermal stability and Cpk process capability index: The thermal stability is excep•onally good due to an innova•ve 6•axis de•sign and double-skin coolant enclosure. Field tests have demonstrated an unusually high Cpk process capability index for any tool grinding machine.
Grinding range: From micro•size range to 1/2” (12.7 mm). And many more new features.
Contact Details
Related Glossary Terms
- computer numerical control ( CNC)
computer numerical control ( CNC)
Microprocessor-based controller dedicated to a machine tool that permits the creation or modification of parts. Programmed numerical control activates the machine’s servos and spindle drives and controls the various machining operations. See DNC, direct numerical control; NC, numerical control.
- coolant
coolant
Fluid that reduces temperature buildup at the tool/workpiece interface during machining. Normally takes the form of a liquid such as soluble or chemical mixtures (semisynthetic, synthetic) but can be pressurized air or other gas. Because of water’s ability to absorb great quantities of heat, it is widely used as a coolant and vehicle for various cutting compounds, with the water-to-compound ratio varying with the machining task. See cutting fluid; semisynthetic cutting fluid; soluble-oil cutting fluid; synthetic cutting fluid.
- grinding
grinding
Machining operation in which material is removed from the workpiece by a powered abrasive wheel, stone, belt, paste, sheet, compound, slurry, etc. Takes various forms: surface grinding (creates flat and/or squared surfaces); cylindrical grinding (for external cylindrical and tapered shapes, fillets, undercuts, etc.); centerless grinding; chamfering; thread and form grinding; tool and cutter grinding; offhand grinding; lapping and polishing (grinding with extremely fine grits to create ultrasmooth surfaces); honing; and disc grinding.
- grinding machine
grinding machine
Powers a grinding wheel or other abrasive tool for the purpose of removing metal and finishing workpieces to close tolerances. Provides smooth, square, parallel and accurate workpiece surfaces. When ultrasmooth surfaces and finishes on the order of microns are required, lapping and honing machines (precision grinders that run abrasives with extremely fine, uniform grits) are used. In its “finishing” role, the grinder is perhaps the most widely used machine tool. Various styles are available: bench and pedestal grinders for sharpening lathe bits and drills; surface grinders for producing square, parallel, smooth and accurate parts; cylindrical and centerless grinders; center-hole grinders; form grinders; facemill and endmill grinders; gear-cutting grinders; jig grinders; abrasive belt (backstand, swing-frame, belt-roll) grinders; tool and cutter grinders for sharpening and resharpening cutting tools; carbide grinders; hand-held die grinders; and abrasive cutoff saws.
- lean manufacturing
lean manufacturing
Companywide culture of continuous improvement, waste reduction and minimal inventory as practiced by individuals in every aspect of the business.
- steady rest
steady rest
Supports long, thin or flexible work being turned on a lathe. Mounts on the bed’s ways and, unlike a follower rest, remains at the point where mounted. See follower rest.