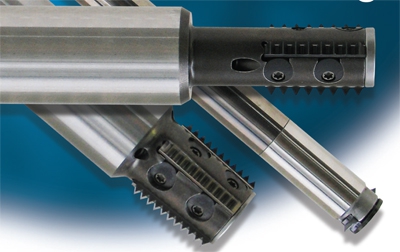
Advent Tool and Manufacturing Inc.'s GT (Generation Two) Tooling is its new line of replaceable inserts and holders for threadmilling. Single-point tools have a carbide shank, hardened tool steel replaceable head, through-coolant capability and are for deep holes (8 times the shank diameter and deeper).
The GT indexable tooling with double-sided inserts are for producing UNC threads. The tools are fully hardened and CNC ground, have through-body coolant capability, can be run without an end plate for threading blind-holes and are suitable for small-diameter and corse-pitch internal threading applications.
The GT indexable tooling with single-sided inserts are for producing NPT/API threads. They are suitable for external and internal threading applications. The tools are fully hardened and CNC ground, have through-body coolant capability and a removable end cap for threading blind-holes.
Contact Details
Related Glossary Terms
- computer numerical control ( CNC)
computer numerical control ( CNC)
Microprocessor-based controller dedicated to a machine tool that permits the creation or modification of parts. Programmed numerical control activates the machine’s servos and spindle drives and controls the various machining operations. See DNC, direct numerical control; NC, numerical control.
- coolant
coolant
Fluid that reduces temperature buildup at the tool/workpiece interface during machining. Normally takes the form of a liquid such as soluble or chemical mixtures (semisynthetic, synthetic) but can be pressurized air or other gas. Because of water’s ability to absorb great quantities of heat, it is widely used as a coolant and vehicle for various cutting compounds, with the water-to-compound ratio varying with the machining task. See cutting fluid; semisynthetic cutting fluid; soluble-oil cutting fluid; synthetic cutting fluid.
- shank
shank
Main body of a tool; the portion of a drill or similar end-held tool that fits into a collet, chuck or similar mounting device.
- threading
threading
Process of both external (e.g., thread milling) and internal (e.g., tapping, thread milling) cutting, turning and rolling of threads into particular material. Standardized specifications are available to determine the desired results of the threading process. Numerous thread-series designations are written for specific applications. Threading often is performed on a lathe. Specifications such as thread height are critical in determining the strength of the threads. The material used is taken into consideration in determining the expected results of any particular application for that threaded piece. In external threading, a calculated depth is required as well as a particular angle to the cut. To perform internal threading, the exact diameter to bore the hole is critical before threading. The threads are distinguished from one another by the amount of tolerance and/or allowance that is specified. See turning.