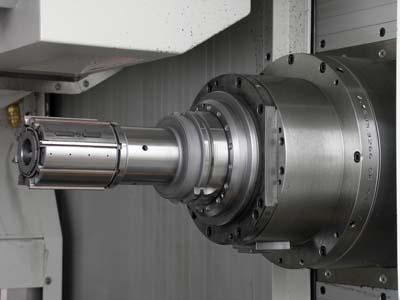
"One Source — Many Solutions" takes on added meaning at MAG with the addition of honing capability on MAG's automotive industry machines, according to the company. This new machining center solution provides a complete process, potentially eliminating secondary honing machines for the manufacture of engine cylinder and crankshaft bores.
MAG says it is one of the leading providers of systems for high-volume production of engine and powertrain components, and has always approached this business emphasizing complete, customized solutions. Those solutions are now even more complete with the addition of honing capability on MAG machining centers. This means that every process, from the machining of castings to the finishing of cylinder and crankshaft bores, can now be conducted on CNC machining centers. The new process uses a combination of fine-drilling and honing on a single machine. The optimization and interlinking of the two operations brings about a significant reduction in cycle time.
"During the past few months, our experts have been working on finding a solution to the specific requirements for machine kinematics, the machining spindle, tools and the control and regulation concept," explained Dr. Tobias Abeln, Engineering Manager at MAG's Eislingen operation. "We have now reached the point where we can produce bore geometries and surface finishes to the same quality as when using conventional honing machines, and we can do so in a distinctly shorter period of time with significantly lower costs."
Honing is always required when bores must meet high-end requirements for size, cylinder form and specific surface parameters. One of the primary application areas is the finishing of cylinder and crank bores made of cast iron, aluminum alloys and ferrous layers. In volume production, these features are typically finish machined on special honing machines in a secondary operation.
MAG's goal, of course, was to integrate this bore finishing operation on a single machine, which required overcoming the hurdles of adding the honing process management functions to a machining center. By executing fine-drilling and honing operations on a clamped workpiece, the universal-jointed honing tool connection required for compensating any differences in positioning can be dispensed with. This eliminates high-cost hinged tool connections, and tools can be changed quickly and automatically with tool orientation unaffected by position and gravitational force.
The necessary modifications on the basic machining center are relatively few. These included integration of in-process air gaging technology and an electromechanical actuation system for the spindle, using a push-pull rod, needed to actuate the honing tool. This spindle is also designed for other applications that require a geometrically-specific cutting edge, such as valve-seat machining (e.g., turning of valve seats on CNC machines) and the machining of bores with defined contours (e.g., boring of 3-D contours).
Honing capability adds a small cost premium to the machining center, but it is comparatively small when taking into account that separate honing machines and their coolant supplies are eliminated from the manufacturing line. That's not all. Because of the energy-optimization features of the new Specht generation, savings up to US$76,000 can be achieved over a comparable system with separate honing machine, at an annual production volume of 500,000 units.
Contact Details
Related Glossary Terms
- 3-D
3-D
Way of displaying real-world objects in a natural way by showing depth, height and width. This system uses the X, Y and Z axes.
- alloys
alloys
Substances having metallic properties and being composed of two or more chemical elements of which at least one is a metal.
- aluminum alloys
aluminum alloys
Aluminum containing specified quantities of alloying elements added to obtain the necessary mechanical and physical properties. Aluminum alloys are divided into two categories: wrought compositions and casting compositions. Some compositions may contain up to 10 alloying elements, but only one or two are the main alloying elements, such as copper, manganese, silicon, magnesium, zinc or tin.
- boring
boring
Enlarging a hole that already has been drilled or cored. Generally, it is an operation of truing the previously drilled hole with a single-point, lathe-type tool. Boring is essentially internal turning, in that usually a single-point cutting tool forms the internal shape. Some tools are available with two cutting edges to balance cutting forces.
- centers
centers
Cone-shaped pins that support a workpiece by one or two ends during machining. The centers fit into holes drilled in the workpiece ends. Centers that turn with the workpiece are called “live” centers; those that do not are called “dead” centers.
- computer numerical control ( CNC)
computer numerical control ( CNC)
Microprocessor-based controller dedicated to a machine tool that permits the creation or modification of parts. Programmed numerical control activates the machine’s servos and spindle drives and controls the various machining operations. See DNC, direct numerical control; NC, numerical control.
- coolant
coolant
Fluid that reduces temperature buildup at the tool/workpiece interface during machining. Normally takes the form of a liquid such as soluble or chemical mixtures (semisynthetic, synthetic) but can be pressurized air or other gas. Because of water’s ability to absorb great quantities of heat, it is widely used as a coolant and vehicle for various cutting compounds, with the water-to-compound ratio varying with the machining task. See cutting fluid; semisynthetic cutting fluid; soluble-oil cutting fluid; synthetic cutting fluid.
- machining center
machining center
CNC machine tool capable of drilling, reaming, tapping, milling and boring. Normally comes with an automatic toolchanger. See automatic toolchanger.
- turning
turning
Workpiece is held in a chuck, mounted on a face plate or secured between centers and rotated while a cutting tool, normally a single-point tool, is fed into it along its periphery or across its end or face. Takes the form of straight turning (cutting along the periphery of the workpiece); taper turning (creating a taper); step turning (turning different-size diameters on the same work); chamfering (beveling an edge or shoulder); facing (cutting on an end); turning threads (usually external but can be internal); roughing (high-volume metal removal); and finishing (final light cuts). Performed on lathes, turning centers, chucking machines, automatic screw machines and similar machines.