Contact Details
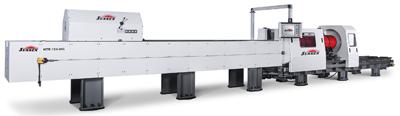
Sunnen's new HTR all-electric job-shop tube hone combines servo precision and cycle-automation features with constant spindle power and 0.1mm (0.004") stroke repeatability to efficiently hone blind bores or correct tight spots in a bore without operator intervention. Designed and equipped to hone the wide variety of parts encountered in a job shop, the machine handles bore I.D.'s up to 900mm (35.41"). Its modular design can be configured for stroke lengths from 2.5 m to 14 m (8' to 46.2').
Critical for job-shop versatility and productivity, the HTR's 12 kW (16-hp) spindle motor, combined with a four-step gearbox, produces a constant power band through the entire speed range of 10-470 rpm for fast metal removal. The standard servo rotary tool feed can also function as a push-feed system with an optional drive shaft that converts rotary to linear motion, allowing the machine to handle the full range of Sunnen heavy-duty and two-stage tools. Tool overload monitoring ensures optimal stock removal rates, while protecting the tool and workpiece. Precision stroke position and repeatability are ensured with a servo rack-and-pinion stroking system. It drives the spindle carriage at speeds of 0.1 to 48 m/min. (4 to 157 sfm) on hardened and ground ways with a 10.2 kW (13.6 hp) servomotor, giving the machine plenty of power to handle superabrasives for fast material removal.
The HTR's design eliminates all hydraulics to vastly reduce maintenance, noise, leakage and heat, as well as system hysteresis due to hydraulic oil heating up. The machine's 305-mm (12") Windows touchscreen PC control manages all machine functions, including stroke speed/position, tool feed, spindle speed, stone wear compensation and cutting pressure. Standard control features include size lock, automatic bore geometry correction, recommended setups, tool overload protection, spark out, spindle jog and short stroke. The control can store up to 900 different part programs and be configured for 13 languages.
The HTR's optional easy-to-setup fixturing is available in two ranges for parts 40 to 600mm (1.6" to 31.8"), and parts 50 to 810mm (2" to 31.8"). Part weight capacity is 6,000 kg (13,230 lb) and 8,000 kg (17,640 lb) respectively. The fixtures ride on a linear bearing system to allow easy positioning. Multiple coolant system configurations are available to tailor for process requirements. Other options include in-process gaging, tapered-bore capability, various coolant systems, part rotation device, moving steady rests for 2-m and 4-m models, two-stage honing, air conditioned electrical cabinet and CE compliant safety system.
Related Glossary Terms
- bandsaw blade ( band)
bandsaw blade ( band)
Endless band, normally with serrated teeth, that serves as the cutting tool for cutoff or contour band machines.
- coolant
coolant
Fluid that reduces temperature buildup at the tool/workpiece interface during machining. Normally takes the form of a liquid such as soluble or chemical mixtures (semisynthetic, synthetic) but can be pressurized air or other gas. Because of water’s ability to absorb great quantities of heat, it is widely used as a coolant and vehicle for various cutting compounds, with the water-to-compound ratio varying with the machining task. See cutting fluid; semisynthetic cutting fluid; soluble-oil cutting fluid; synthetic cutting fluid.
- feed
feed
Rate of change of position of the tool as a whole, relative to the workpiece while cutting.
- in-process gaging ( in-process inspection)
in-process gaging ( in-process inspection)
Quality-control approach that monitors work in progress, rather than inspecting parts after the run has been completed. May be done manually on a spot-check basis but often involves automatic sensors that provide 100 percent inspection.
- modular design ( modular construction)
modular design ( modular construction)
Manufacturing of a product in subassemblies that permits fast and simple replacement of defective assemblies and tailoring of the product for different purposes. See interchangeable parts.