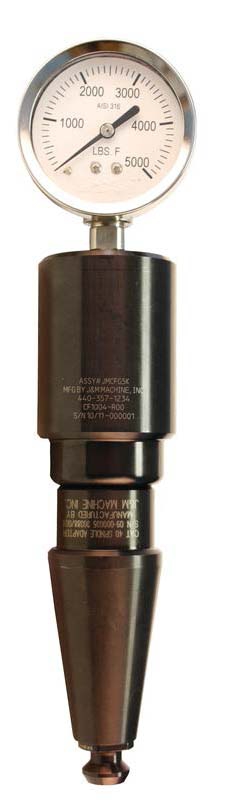
Keeping heavy investment machines running while increasing tool life to optimize production rates is the Holy Grail of today’s CNC machining center operations. Just because a CNC machine is clamping doesn’t mean it’s functioning properly. Often you’ll realize that you can't run the same job on different machines, or tool life is better on one machine than another. Whether it’s a new or old machine, the answer can often be found in the diminished clamping force of the drawbar.
Drawbar force is the measure of force being applied to a toolholder to keep it in full contact with the spindle. If the clamping force is diminished, it can cause serious issues such as decreased tool life, chatter, vibration, and poor finishes. In extreme cases, the tool can pull out of the spindle during the cut, causing damage to the work piece, tools, and spindle.
Ultimately, fixing the spindle can result in costly downtime ranging anywhere from 2-3 days or 2-4 weeks.
JM Performance Products Inc. has engineered its patented hydraulic Clamp Force Gage to provide a quick and inexpensive method to regularly check and measure the clamping/pulling force of the spindle drawbar. The hydraulic gage instantly reads in ft/lbs the amount of pull force being applied to the toolholder. Once drawbar force drops below 80 percent of the original manufacturer's setting, it is time to schedule maintenance.
The innovative engineering design of two main parts makes it the first universal gage on the market−allowing it to be used anywhere in the shop to check all types of V-flange spindles. These key advancements have also allowed JMPP to reduce the price of the product by approximately one-half ($400-$600) vs. competing products, based on the size of the gage head and taper(s). For long-term value, the Clamp Force Gage can be cost-efficiently recalibrated by JMPP.
Clamp Force Gage hydraulic heads are available in 3,000, 5,000, 10,000, and 15,000 pound configurations. It is the perfect solution for the smaller shop that is looking for a quick and inexpensive method to check drawbar force. The hydraulic gage head comes with a toolbox and protective packaging for easy storage. One gage head will work in multiple size spindles with easy-change taper adapters available.
Notable design benefits of JMPP’s Clamp Force Gage include:
▪ Prevents expensive machine downtime by scheduling machine maintenance and avoiding machine crashes.
▪ Increases tool life and eliminates scrapped parts due to poor tolerance.
▪ Operator safety−a loose toolholder is dangerous.
▪ Adapters are available in many sizes and fit the universal gage heads.
The drawbar works by using Belleville washer stacks or gas systems to generate the drawbar force. As the Belleville washers begin to collapse and gas systems begin to leak, the drawbar loses force. Because the drawbar is located out of sight and not easily accessed, it is often left unmonitored. If the Belleville washer stack is not rebuilt or the gas system recharged, the toolholder will fall out during cutting, potentially causing catastrophic damage. Typically, operators can only tell when fatigue starts to set in, that’s why JMPP’s Clamp Force Gage is an optimal solution for frequent monitoring which is key for preventative maintenance.
According to JMPP President, John Stoneback, “If left alone, this out-of-sight/out-of-mind philosophy may result in the machine reaching zero draw force and you can lose the toolholder, work piece, and potentially damage the machine. Therefore, it’s essential to implement a frequent monitoring system that operators should conduct at least once per week.”
Contact Details
Related Glossary Terms
- chatter
chatter
Condition of vibration involving the machine, workpiece and cutting tool. Once this condition arises, it is often self-sustaining until the problem is corrected. Chatter can be identified when lines or grooves appear at regular intervals in the workpiece. These lines or grooves are caused by the teeth of the cutter as they vibrate in and out of the workpiece and their spacing depends on the frequency of vibration.
- computer numerical control ( CNC)
computer numerical control ( CNC)
Microprocessor-based controller dedicated to a machine tool that permits the creation or modification of parts. Programmed numerical control activates the machine’s servos and spindle drives and controls the various machining operations. See DNC, direct numerical control; NC, numerical control.
- fatigue
fatigue
Phenomenon leading to fracture under repeated or fluctuating stresses having a maximum value less than the tensile strength of the material. Fatigue fractures are progressive, beginning as minute cracks that grow under the action of the fluctuating stress.
- machining center
machining center
CNC machine tool capable of drilling, reaming, tapping, milling and boring. Normally comes with an automatic toolchanger. See automatic toolchanger.
- tolerance
tolerance
Minimum and maximum amount a workpiece dimension is allowed to vary from a set standard and still be acceptable.
- toolholder
toolholder
Secures a cutting tool during a machining operation. Basic types include block, cartridge, chuck, collet, fixed, modular, quick-change and rotating.