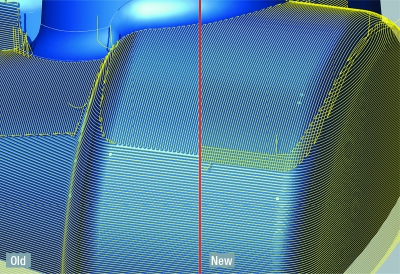
OPEN MIND Technologies AG has introduced hyperMILL 2018.1, a new version of its advanced, comprehensive CAM software. hyperMILL 2018.1 has a range of new features and enhancements including greater blending capabilities, 3D-optimized roughing, global fitting, rotational abilities for CAD electrode applications and virtual machining simulation.
"hyperMILL 2018.1 demonstrates our commitment to innovation when providing CAM users with the tools they need to be successful," said Alan Levine, managing director of OPEN MIND Technologies USA Inc. "We continue to advance functionality in the hyperMILL suite to keep it at the forefront of CAM technology."
New hyperMILL 2018.1 functionality includes an enhancement to the "soft overlap" feature (pictured) for blending machining marks found between steep and flat areas, or located at the boundaries of rest machining regions. Using this enhanced feature, the milling tool is briefly lifted to blend milling paths into another, preventing visible transitions from being generated, resulting in better surface quality.
In hyperMILL 2018.1, the 3D-optimized roughing cycle has been enhanced for applications with high-feed cutters. The step-over distance can be calculated from the scallop height measured against the high-feed cutter geometry. A special toolpath movement removes rest material from corners when there is a very large step-over. Intelligent cut division and optimized toolpaths provide greater process safety for the remaining thin ridges.
A new "global fitting" feature can simplify the definition of complex surfaces or patches of surfaces. Many hyperMILL CAM strategies will recognize and follow the ISO u-v orientation of the surface patch. hyperMILL MAXX Machining finishing is one technique that benefits from having a simplified surface definition.
hyperCAD-S Electrode automates the construction and manufacturing of electrodes for die sinking. Users can simply choose their electrodes from the face to be die-sunk within the component geometry, with no special expertise required. To save users time during milling and eroding, hyperCAD-S in hyperMILL 2018.1 includes an easy-to-use "rotational electrode" feature, which facilitates the circular placement of multiple electrode geometries with different spark gaps on a holder.
Developed with Industry 4.0 in mind, an early release of hyperMILL VIRTUAL Machining simulation is available in version 2018.1, which enables constant real time bidirectional communication between the machine tool controller and a remote hyperMILL VIRTUAL Machining simulation, significantly improving manufacturing workflow. Machining operations can be reliably evaluated, checked and optimized before running a job by using process networking and virtual mapping found in hyperMILL VIRTUAL Machining. The hyperMILL VIRTUAL Machining NC Optimizer can enhance computed NC instructions to optimize available workspace, manage limited axes and select the best approach for asymmetric machine heads. Safety, reliability, speed and process control optimization from CAD/CAM to machine are all improved with hyperMILL VIRTUAL Machining.
Contact Details
Related Glossary Terms
- computer-aided design ( CAD)
computer-aided design ( CAD)
Product-design functions performed with the help of computers and special software.
- computer-aided manufacturing ( CAM)
computer-aided manufacturing ( CAM)
Use of computers to control machining and manufacturing processes.
- flat ( screw flat)
flat ( screw flat)
Flat surface machined into the shank of a cutting tool for enhanced holding of the tool.
- gang cutting ( milling)
gang cutting ( milling)
Machining with several cutters mounted on a single arbor, generally for simultaneous cutting.
- milling
milling
Machining operation in which metal or other material is removed by applying power to a rotating cutter. In vertical milling, the cutting tool is mounted vertically on the spindle. In horizontal milling, the cutting tool is mounted horizontally, either directly on the spindle or on an arbor. Horizontal milling is further broken down into conventional milling, where the cutter rotates opposite the direction of feed, or “up” into the workpiece; and climb milling, where the cutter rotates in the direction of feed, or “down” into the workpiece. Milling operations include plane or surface milling, endmilling, facemilling, angle milling, form milling and profiling.
- numerical control ( NC)
numerical control ( NC)
Any controlled equipment that allows an operator to program its movement by entering a series of coded numbers and symbols. See CNC, computer numerical control; DNC, direct numerical control.
- process control
process control
Method of monitoring a process. Relates to electronic hardware and instrumentation used in automated process control. See in-process gaging, inspection; SPC, statistical process control.
- step-over
step-over
Distance between the passes of the toolpath; the path spacing. The distance the tool will move horizontally when making the next pass. Too great of a step-over will cause difficulty machining because there will be too much pressure on the tool as it is trying to cut with too much of its surface area.
- toolpath( cutter path)
toolpath( cutter path)
2-D or 3-D path generated by program code or a CAM system and followed by tool when machining a part.