Contact Details
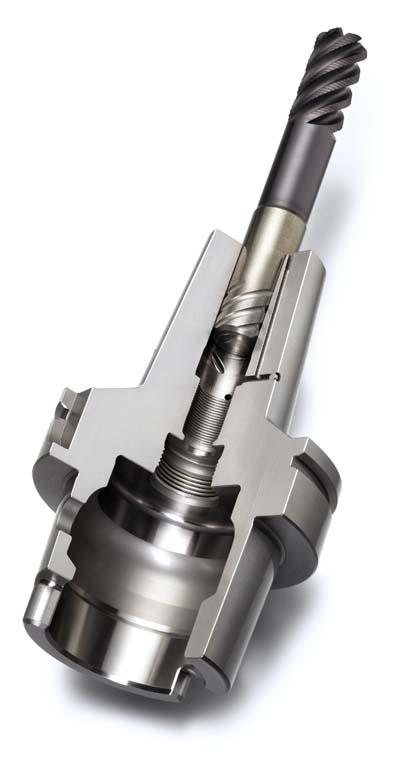
The axial forces created when machining in ISO S materials with a solid carbide end mill puts very high demands on the clamping mechanism. In some situations the tool can pull out from the chuck despite the chuck's high clamping force. Components that are produced in these materials are expensive with a large number of machining hours invested and the consequence of tool pull out is catastrophic.
The new iLock fixturing system from Sandvik Coromant solves this problem by securing the end mill without interfering with the runout precision of Shrink Fit. This is achieved by helical grooves that are ground into the shank of the tool. Pin drivers mounted in the chuck prevent the tool from being pulled out of the holder during extreme machining conditions. This solution provides maximum process security.
These new chucks and solid carbide end mills offer a combination of security of pull out prevention with high precision, providing optimized metal cutting efficiency.
The CoroMill Plura with iLock program will be focused towards titanium milling in aerospace frame components.
Related Glossary Terms
- chuck
chuck
Workholding device that affixes to a mill, lathe or drill-press spindle. It holds a tool or workpiece by one end, allowing it to be rotated. May also be fitted to the machine table to hold a workpiece. Two or more adjustable jaws actually hold the tool or part. May be actuated manually, pneumatically, hydraulically or electrically. See collet.
- gang cutting ( milling)
gang cutting ( milling)
Machining with several cutters mounted on a single arbor, generally for simultaneous cutting.
- milling
milling
Machining operation in which metal or other material is removed by applying power to a rotating cutter. In vertical milling, the cutting tool is mounted vertically on the spindle. In horizontal milling, the cutting tool is mounted horizontally, either directly on the spindle or on an arbor. Horizontal milling is further broken down into conventional milling, where the cutter rotates opposite the direction of feed, or “up” into the workpiece; and climb milling, where the cutter rotates in the direction of feed, or “down” into the workpiece. Milling operations include plane or surface milling, endmilling, facemilling, angle milling, form milling and profiling.
- milling machine ( mill)
milling machine ( mill)
Runs endmills and arbor-mounted milling cutters. Features include a head with a spindle that drives the cutters; a column, knee and table that provide motion in the three Cartesian axes; and a base that supports the components and houses the cutting-fluid pump and reservoir. The work is mounted on the table and fed into the rotating cutter or endmill to accomplish the milling steps; vertical milling machines also feed endmills into the work by means of a spindle-mounted quill. Models range from small manual machines to big bed-type and duplex mills. All take one of three basic forms: vertical, horizontal or convertible horizontal/vertical. Vertical machines may be knee-type (the table is mounted on a knee that can be elevated) or bed-type (the table is securely supported and only moves horizontally). In general, horizontal machines are bigger and more powerful, while vertical machines are lighter but more versatile and easier to set up and operate.
- shank
shank
Main body of a tool; the portion of a drill or similar end-held tool that fits into a collet, chuck or similar mounting device.
Additional Products from Sandvik Coromant Co.
Pagination
- First page
- Previous page
- …
- 5
- 6
- 7
- 8
- 9
- 10
- 11
- 12
- 13