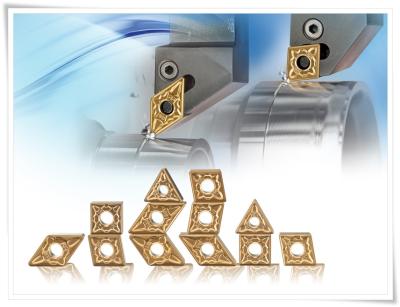
KORLOY has launched new chipbreakers “ MM ” (Medium Machining) and “ RM ” (Rough Machining) for stainless steel materials. Stainless steel can be classified into three groups: austenite, martensite and ferrite. In principle, the surface of stainless steel materials generally tends to be very smooth and coupled with a very strong corrosion resistance.
Thanks to these positive features, it can be used for various purposes without painting and surface treatment. 13Cr, 18Cr and 18Cr-8Ni are typical high-alloy steel of stainless steel.
Stainless steel has a strong tendency for workhardening and built-up edge, and has a strong resistance force. Due to these features, stainless steel is classified as a difficult-to-cut material, which shortens tool life by causing damage on the cutting edge and built-up edge. Because stainless steel and difficult-to-cut materials are tough and hard, it is important to choose the right geometry and grade.
MM chip breaker for (medium operation), the first recommendation for stainless steel has a dual-angle land and reinforced toughness, which leads to stable tool life as well as less cutting load thereby minimizing built-up edge.
In the range of high feed and high depth of cut, its wide chip pocket prevents chips from curving toward the minor cutting edge, then evacuates chips to prevent plastic deformation and excessive wear on minor cutting edge.
RM chip breaker for (roughing operation), has a low resistance-type chipbreaker characterized by wide land and rake angle. It is recommended for rough cutting or when burr occurs due to flank wear. It evacuates chips and heat caused by tough cutting parameters such as high feed and deep depth of cut through its gradual rake angle. RM chipbreaker ensures stable tool life, along with its effective chip evacuation and cutting heat dispersion.
Contact Details
Related Glossary Terms
- austenite
austenite
Solid solution of one or more elements in face-centered cubic iron. Unless otherwise designated (such as nickel austenite), the solute is generally assumed to be carbon. Austenite can dissolve up to 2 percent carbon. Austenite is relatively soft, ductile and nonmagnetic.
- built-up edge ( BUE)
built-up edge ( BUE)
1. Permanently damaging a metal by heating to cause either incipient melting or intergranular oxidation. 2. In grinding, getting the workpiece hot enough to cause discoloration or to change the microstructure by tempering or hardening.
- burr
burr
Stringy portions of material formed on workpiece edges during machining. Often sharp. Can be removed with hand files, abrasive wheels or belts, wire wheels, abrasive-fiber brushes, waterjet equipment or other methods.
- chipbreaker
chipbreaker
Groove or other tool geometry that breaks chips into small fragments as they come off the workpiece. Designed to prevent chips from becoming so long that they are difficult to control, catch in turning parts and cause safety problems.
- corrosion resistance
corrosion resistance
Ability of an alloy or material to withstand rust and corrosion. These are properties fostered by nickel and chromium in alloys such as stainless steel.
- depth of cut
depth of cut
Distance between the bottom of the cut and the uncut surface of the workpiece, measured in a direction at right angles to the machined surface of the workpiece.
- feed
feed
Rate of change of position of the tool as a whole, relative to the workpiece while cutting.
- ferrite
ferrite
Solid solution of one or more elements in body-centered cubic iron. Unless otherwise designated, for instance, as chromium ferrite, the solute is generally assumed to be carbon. On an equilibrium diagram, there are two ferrite regions separated by an austenite area. The lower area is alpha ferrite and the upper area is delta ferrite. If there is no designation, alpha ferrite is assumed. Not more than 0.04 percent carbon can be dissolved in alpha iron. Ferrite is stable below 1,670º F (910º C); it is soft, highly ductile, and magnetic. Ferrite loses its magnetic property above 1,414º F (768º C).
- flank wear
flank wear
Reduction in clearance on the tool’s flank caused by contact with the workpiece. Ultimately causes tool failure.
- land
land
Part of the tool body that remains after the flutes are cut.
- martensite
martensite
Formed during rapid cooling of austenite at the temperature rate higher than 500º F (260º C) per second. Such rapid cooling causes restructuring of crystalline lattice of gamma iron into crystalline lattice of alpha iron in which carbon is fully dissolved. Because only 0.04 percent carbon can be dissolved in alpha iron, the excessive amount of carbon transforms into supersaturated solution of carbon in alpha iron. This type of solution is called martensite, which is characterized by an angular needlelike brittle structure and high hardness (greater than 60 HRC).
- plastic deformation
plastic deformation
Permanent (inelastic) distortion of metals under applied stresses that strain the material beyond its elastic limit.
- rake
rake
Angle of inclination between the face of the cutting tool and the workpiece. If the face of the tool lies in a plane through the axis of the workpiece, the tool is said to have a neutral, or zero, rake. If the inclination of the tool face makes the cutting edge more acute than when the rake angle is zero, the rake is positive. If the inclination of the tool face makes the cutting edge less acute or more blunt than when the rake angle is zero, the rake is negative.
- workhardening
workhardening
Tendency of all metals to become harder when they are machined or subjected to other stresses and strains. This trait is particularly pronounced in soft, low-carbon steel or alloys containing nickel and manganese—nonmagnetic stainless steel, high-manganese steel and the superalloys Inconel and Monel.