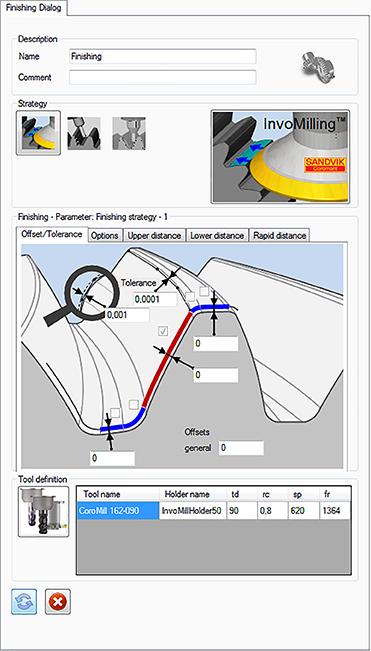
Sandvik Coromant has extended the functionality of its InvoMilling software. The latest version of this user-friendly CAD/CAM solution for fast and simple NC programming offers even more possibilities when manufacturing gears on universal 5-axis machining centers. The software also enables customers to produce straight bevel gears and herringbone gears.
InvoMilling exploits machine tool kinetics for the effective and flexible manufacturing of high-quality gears and splines in quality level 6 or better, according to DIN 3962. After entering the required gear data, the intuitive CAD/CAM software defines the optimum machining strategies and generates a CNC program that allows the production of different gear profiles using just a few standard precision tools. The software also offers excellent graphics, as well as features to create and simulate milling paths.
As well as options for herringbone, double helical (with and without gap), and straight bevel gears, an additional new function available in the latest version of InvoMilling is flank correction. This applies to tip relief and crowning in both the flank and profile directions as well as helix and pressure angle corrections. Numerous improvements have also been made to the tools. For instance, adapted tools have been introduced to the tool library.
"With the new software functionalities and tool optimizations, we are offering our customers additional options for gear cutting in small and medium batch sizes—making the process even more flexible, fast, and efficient," says Jochen Sapparth, product manager InvoMilling CAD/CAM at Sandvik Coromant. "At the same time, we are expanding the range of applications that can be performed using five-axis machining centers."
Contact Details
Related Glossary Terms
- centers
centers
Cone-shaped pins that support a workpiece by one or two ends during machining. The centers fit into holes drilled in the workpiece ends. Centers that turn with the workpiece are called “live” centers; those that do not are called “dead” centers.
- computer numerical control ( CNC)
computer numerical control ( CNC)
Microprocessor-based controller dedicated to a machine tool that permits the creation or modification of parts. Programmed numerical control activates the machine’s servos and spindle drives and controls the various machining operations. See DNC, direct numerical control; NC, numerical control.
- gang cutting ( milling)
gang cutting ( milling)
Machining with several cutters mounted on a single arbor, generally for simultaneous cutting.
- milling
milling
Machining operation in which metal or other material is removed by applying power to a rotating cutter. In vertical milling, the cutting tool is mounted vertically on the spindle. In horizontal milling, the cutting tool is mounted horizontally, either directly on the spindle or on an arbor. Horizontal milling is further broken down into conventional milling, where the cutter rotates opposite the direction of feed, or “up” into the workpiece; and climb milling, where the cutter rotates in the direction of feed, or “down” into the workpiece. Milling operations include plane or surface milling, endmilling, facemilling, angle milling, form milling and profiling.
- numerical control ( NC)
numerical control ( NC)
Any controlled equipment that allows an operator to program its movement by entering a series of coded numbers and symbols. See CNC, computer numerical control; DNC, direct numerical control.
- relief
relief
Space provided behind the cutting edges to prevent rubbing. Sometimes called primary relief. Secondary relief provides additional space behind primary relief. Relief on end teeth is axial relief; relief on side teeth is peripheral relief.