Contact Details
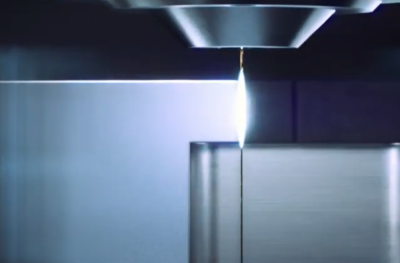
As the first of its kind in the industry, the new iWire function from GF Machining Solutions automatically identifies and adapts wire speed to changing erosion height conditions during the wire EDM process. This capability eliminates wire breakage while reducing overall wire consumption per job, in some instances by as much as 29%.
Featured on new GF Machining Solutions’ CUT P Pro Series wire EDMs, the iWire function works in tandem with the company’s Intelligent Spark Protection System (ISPS), both of which are part of the company’s Uniqua control.
What started with GF Machining Solutions Spark Track technology four years ago has advanced to the company’s ISPS and now iWire technologies. Building on its amassed technological knowledge from decades of experience in EDM, the company can not only recognize exactly where the sparks of a wire EDM are happening during the process, it can also measure and identify the position of each spark along the length of an EDM’s wire.
Knowing the exact location of a spark allows iWire to automatically adapt the wire spool speed accordingly. Such capability reduces the chances of wire breakage during unattended operations when EDMing parts with steps and other features that vary the erosion height – the length of the actual surface areas where the wire is eroding/cutting.
Both ISPS and iWire help prevent wire breakage in any conditions while also lowering wire usage to reduce consumables costs and increase EDM productivity. In testing, iWire working with ISPS prevented wire breakage on a part with numerous features with varying erosion heights. The cut started at a standard spool speed, then when the cutting height lessened, the speed slowed. As a result, wire savings equated to about 480m or 0.2kg, and overall process time savings amounted to 28 minutes for a 30% overall reduction.
In another customer test, ISPS and iWire reduced wire break areas from nine to zero. The customer reduced wire consumption by 29% and eliminated machine stoppages due to wire breakage.
Related Glossary Terms
- electrical-discharge machining ( EDM)
electrical-discharge machining ( EDM)
Process that vaporizes conductive materials by controlled application of pulsed electrical current that flows between a workpiece and electrode (tool) in a dielectric fluid. Permits machining shapes to tight accuracies without the internal stresses conventional machining often generates. Useful in diemaking.
- wire EDM
wire EDM
Process similar to ram electrical-discharge machining except a small-diameter copper or brass wire is used as a traveling electrode. Usually used in conjunction with a CNC and only works when a part is to be cut completely through. A common analogy is wire electrical-discharge machining is like an ultraprecise, electrical, contour-sawing operation.