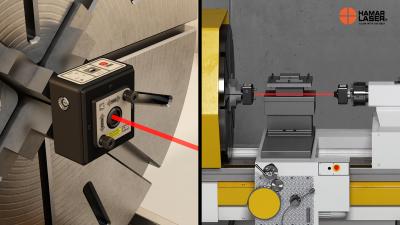
Hamar Laser Instruments, Inc., a world leader in laser alignment, announces the release of their new L-703S 4-Axis Lathe & Turning-Center Spindle Alignment System. Featuring the “S” variant of Hamar Laser’s compact and versatile next-generation L-703 Laser, the new system is the latest in a growing family of alignment packages designed for specific applications.
The new L-703S Laser mounts directly into spindle chucks and collets for aligning headstock spindle axes to guideways and sub-spindles and tailstocks on lathes, OD/ID grinders, turning centers, and similar machines. The L-703S may also be used for guideway straightness checks during preventive maintenance and assembly, and for checking surface plates.
“Hamar Laser’s next-generation L-703 Laser design features significantly higher accuracy and several notable improvements over earlier models,” said Rod Hamar, President of Hamar Laser Instruments. “Our team’s design allowed us to reduce size, cost and complexity, increase accuracy and get rid of annoying wires by adding Bluetooth communications. With a 40% reduction in axial space over our previous L-700 model, the L-703S is much better suited for smaller lathes and turning centers. To top it off, the price of the new system is significantly less than our older L-700 spindle kit.”
Small and lightweight, the L-703S Laser is ideally suited for all kinds of turning applications, from small CNC turning centers and Swiss-type machines to large-bed lathes. With a range of up to 50 ft. (15 m), the laser can also quickly and easily check the alignment of even very large lathes.
The L-703S System features Hamar’s next-gen T-1296 5-Axis Wireless Spindle & Scan Target, which can easily check all four alignment axes of a headstock spindle relative to the tailstock. The T-1296 offers a center resolution of .00001 in. (0.00025 mm) and angular resolution of up to .00002 in/ft (0.002 mm/m). This extremely high level of accuracy can significantly improve machine performance, reduce scrap rates and increase productivity.
The T-1296 Target’s data updates in real time, so alignment errors can be fixed easily and quickly without changing the setup. The new system aligns machines up to 70% faster than conventional methods, such as use indicators and alignment bars. Setup is simple and only minimal training is required.
The L-703S System package typically includes Hamar Laser’s T-1296 Target with 3 in. (75 mm) angular lens and new S-1408 Lathe10 Alignment Software for Lathes and Turning Centers. Windows-based Lathe10 uses an Easy-Guide™ system that walks users through spindle alignments in six steps and has a 4-axis spindle alignment screen to re-align spindles in real time. L-703S kits can be customized for users’ unique requirements with a variety of accessories and fixtures.
Contact Details
Related Glossary Terms
- centers
centers
Cone-shaped pins that support a workpiece by one or two ends during machining. The centers fit into holes drilled in the workpiece ends. Centers that turn with the workpiece are called “live” centers; those that do not are called “dead” centers.
- computer numerical control ( CNC)
computer numerical control ( CNC)
Microprocessor-based controller dedicated to a machine tool that permits the creation or modification of parts. Programmed numerical control activates the machine’s servos and spindle drives and controls the various machining operations. See DNC, direct numerical control; NC, numerical control.
- lathe
lathe
Turning machine capable of sawing, milling, grinding, gear-cutting, drilling, reaming, boring, threading, facing, chamfering, grooving, knurling, spinning, parting, necking, taper-cutting, and cam- and eccentric-cutting, as well as step- and straight-turning. Comes in a variety of forms, ranging from manual to semiautomatic to fully automatic, with major types being engine lathes, turning and contouring lathes, turret lathes and numerical-control lathes. The engine lathe consists of a headstock and spindle, tailstock, bed, carriage (complete with apron) and cross slides. Features include gear- (speed) and feed-selector levers, toolpost, compound rest, lead screw and reversing lead screw, threading dial and rapid-traverse lever. Special lathe types include through-the-spindle, camshaft and crankshaft, brake drum and rotor, spinning and gun-barrel machines. Toolroom and bench lathes are used for precision work; the former for tool-and-die work and similar tasks, the latter for small workpieces (instruments, watches), normally without a power feed. Models are typically designated according to their “swing,” or the largest-diameter workpiece that can be rotated; bed length, or the distance between centers; and horsepower generated. See turning machine.
- turning
turning
Workpiece is held in a chuck, mounted on a face plate or secured between centers and rotated while a cutting tool, normally a single-point tool, is fed into it along its periphery or across its end or face. Takes the form of straight turning (cutting along the periphery of the workpiece); taper turning (creating a taper); step turning (turning different-size diameters on the same work); chamfering (beveling an edge or shoulder); facing (cutting on an end); turning threads (usually external but can be internal); roughing (high-volume metal removal); and finishing (final light cuts). Performed on lathes, turning centers, chucking machines, automatic screw machines and similar machines.