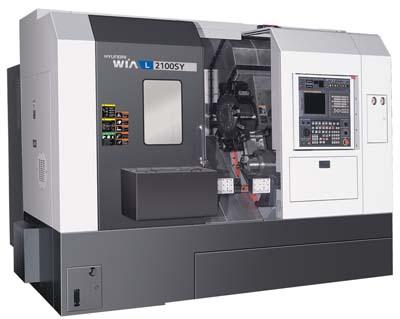
Hyundai WIA announces an all-new Series of CNC multitasking turning centers, the L2100Y/SY, developed with a wedge-type Y-axis and BMT 65 (VDI 140) turret for completing complex milling and turning operations in a single setup. The synchronized 8" main spindle and 6" sub spindle (S-configured machines) enable high precision turning of both front and back of cylindrical parts. Swing over the bed: 630mm. Swing over the carriage: 300mm. Maximum turning diameter: 335mm. Maximum turning length: 468mm (455mm for SY).
The critical structural components of Hyundai WIA's new L2100Y/SY multitasking turning centers are designed using finite element analysis (FEA) to ensure powerful cutting and agility and are composed of meehanite cast iron to minimize deformation when performing heavy-duty cuts. The rigid bed is designed to absorb vibration for stable machining. To eliminate thermal growth during machining, all axes are driven by high precision double-nut ballscrews. The double pretension design provides outstanding positioning and repeatability with virtually no thermal growth. All ballscrews are connected directly to the servo drive motors without gears or belts, eliminating backlash.
Precision axis movement with heavy loads is achieved by the use of hardened and ground wide box guide ways in all three axes. The wedge-type Y-axis design offers superior positional accuracy and is easy to program, which ensures increased productivity. X- and Y-axis travels are 8.3"/3.9" (210/100mm); Z-axis travel is 22.8"/19.7" (580/500mm). Rapid traverse: 709 ipm (18/12 m/min) in X- and Y-axis and 945 ipm (24/24 m/min) in Z-axis.
The L2100Y/SY is configured with a 4,500 rpm main spindle. The gearless 8" spindle has been designed for high-precision applications with features that ensure minimal thermal growth at high speeds or under heavy cutting loads. Furthermore, by enlarging the spindle's diameter and thickness and using only ultra precision class angular bearings, high speed accel/decel is achieved for smooth machining at high rpm. The main spindle delivers minimal noise and vibration even at the highest cutting speeds, guaranteeing extremely stable machining and minimizing thermal transmission to the main spindle. This contributes to improved durability and provides a high quality surface finish on every completed part.
The 6" sub spindle with C-axis offers 0.001 degree indexing and is driven by the B-axis ballscrew and servomotor to ensure high precision and accuracy. Movement of the workpiece between the two spindles is performed in the rotating state by a synchronized control to reduce cycle times and increase productivity. Main and sub spindles are controlled with the C-axis. Contour machining with the C-axis is also possible, enabling the user to machine outer shapes and pockets, of complex parts, using live tools and the Y-axis.
Hyundai WIA's L2100Y/SY turning centers are outfitted with a large 12-station BMT turret enabling the L2100Y/SY Series multitasking machines to perform high accuracy milling operations in a single setup. A high torque servomotor drives the BMT turret with a 0.4 sec indexing time in either direction. The latest generation BMT top plate increases tool performance and rigidity by securing each tool with four screws. Overall cutting power and capability have been improved for all applications, including milling, drilling and tapping. Machining capabilities have been increased with the addition of a Straight milling head, which removes material from the side of the workpiece, and an angular milling head, which allows ID operations.
The all new L2100Y/SY Series is easy to program and operate with its start-of-the-art Fanuc 32i-A Series CNC control featuring a 10.4" color LCD with Manual Guide i.
Contact Details
Related Glossary Terms
- backlash
backlash
Reaction in dynamic motion systems where potential energy that was created while the object was in motion is released when the object stops. Release of this potential energy or inertia causes the device to quickly snap backward relative to the last direction of motion. Backlash can cause a system’s final resting position to be different from what was intended and from where the control system intended to stop the device.
- centers
centers
Cone-shaped pins that support a workpiece by one or two ends during machining. The centers fit into holes drilled in the workpiece ends. Centers that turn with the workpiece are called “live” centers; those that do not are called “dead” centers.
- computer numerical control ( CNC)
computer numerical control ( CNC)
Microprocessor-based controller dedicated to a machine tool that permits the creation or modification of parts. Programmed numerical control activates the machine’s servos and spindle drives and controls the various machining operations. See DNC, direct numerical control; NC, numerical control.
- gang cutting ( milling)
gang cutting ( milling)
Machining with several cutters mounted on a single arbor, generally for simultaneous cutting.
- inches per minute ( ipm)
inches per minute ( ipm)
Value that refers to how far the workpiece or cutter advances linearly in 1 minute, defined as: ipm = ipt 5 number of effective teeth 5 rpm. Also known as the table feed or machine feed.
- inner diameter ( ID)
inner diameter ( ID)
Dimension that defines the inside diameter of a cavity or hole. See OD, outer diameter.
- milling
milling
Machining operation in which metal or other material is removed by applying power to a rotating cutter. In vertical milling, the cutting tool is mounted vertically on the spindle. In horizontal milling, the cutting tool is mounted horizontally, either directly on the spindle or on an arbor. Horizontal milling is further broken down into conventional milling, where the cutter rotates opposite the direction of feed, or “up” into the workpiece; and climb milling, where the cutter rotates in the direction of feed, or “down” into the workpiece. Milling operations include plane or surface milling, endmilling, facemilling, angle milling, form milling and profiling.
- multifunction machines ( multitasking machines)
multifunction machines ( multitasking machines)
Machines and machining/turning centers capable of performing a variety of tasks, including milling, drilling, grinding boring, turning and cutoff, usually in just one setup.
- tapping
tapping
Machining operation in which a tap, with teeth on its periphery, cuts internal threads in a predrilled hole having a smaller diameter than the tap diameter. Threads are formed by a combined rotary and axial-relative motion between tap and workpiece. See tap.
- turning
turning
Workpiece is held in a chuck, mounted on a face plate or secured between centers and rotated while a cutting tool, normally a single-point tool, is fed into it along its periphery or across its end or face. Takes the form of straight turning (cutting along the periphery of the workpiece); taper turning (creating a taper); step turning (turning different-size diameters on the same work); chamfering (beveling an edge or shoulder); facing (cutting on an end); turning threads (usually external but can be internal); roughing (high-volume metal removal); and finishing (final light cuts). Performed on lathes, turning centers, chucking machines, automatic screw machines and similar machines.