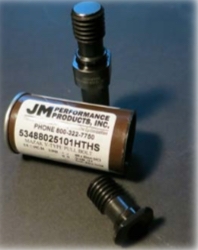
Coupling bolts used for live tooling on lathes are subject to relaxation, which occurs as a result of inadequate pre-loading of the bolts during installation, or to rough or inaccurately machined coupling faces–resulting in misalignment. This misalignment causes excessive vibration, which puts an unnecessary load on bearings, and curtails operation at full power.
In response to a special order request, JM Performance Products, Inc. (JMPP: Fairport Harbor, OH), a leading manufacturing innovator of CNC mill spindle optimization products since 2009, has recently expanded their product offering to include coupling bolts for live tooling on Mazak Corporation (Florence, KY) CNC lathes. These new pull bolts fully incorporate Mazak’s specifications and are uniquely manufactured to implement JMPP’s patented High Torque retention knob standards from 9310H material.
JMPP’s coupling bolts are now available for immediate shipment–eliminating the traditional long lead times for comparable imported coupling bolts for Mazak CNC lathes. Notably, the bolts are aggressively implemented in production across a myriad of industries including; automotive, medical, and aerospace, etc.
COUPLING BOLT ORIGIN / HIGH-TORQUE SOLUTION:
Mazak is a leading manufacturer of CNC lathe and CNC turning centers, and their coupling bolts are an essential part of a work holding system–as live tooling in the lathe workpiece moves their 5-10 Axis Multi-Tasking Machining Centers. Given their essential usage in these centers, they are typically very expensive and also have lengthy lead times from overseas. This issue was addressed by a key Mazak dealer who asked JMPP Plant Manager, Craig Fischer, if it was possible for them to provide a customized solution that would meet the Mazak specifications.
Fischer, and JMPP’s engineering team, noted that the coupling bolts shared a lot of engineering characteristics of their High Torque retention knobs for V-Flange tooling. Given that JMPP currently manufactures and stocks over 400 different styles of retention knobs, the ‘coupling bolt challenge’ was a good fit and melded with their production processes nicely.
According to Fischer, “We quickly implemented our High Torque design into the coupling bolt design specific to the Mazak multi-tasking machines. It’s essentially the same type of holder, so it was just a matter of how the machine holds it in and works with it. On the Mazak machine, you bolt it in via a manual process by putting the screw into the back of it and tightening it. Ultimately, the High Torque design solution solves the same problem of allowing the toolholder to be in the machine without bulging and creating better taper contact. Our 9310H material also delivers higher strength.”
While other machine tool builders require similar bolts for their lathes using live tooling, the Mazak style will be JMPP’s first offering. Fischer said that JMPP is the only retention knob manufacturer of record to progressively respond to the unique modification challenge of the Mazak coupling bolt with a customized solution (based on Mazak’s specs and material)–while incorporating JMPP’s High Torque standard tolerances and design features.
COUPLING BOLT / HIGHT TORQUE CONCLUSION:
The fact is, in the demanding COVID-19 climate, all US manufacturers will have to bundle more technology in their products to compete–at home and globally. By implementing their patented High Torque retention knob design into coupling bolts for live tooling in Mazak’s multi-tasking machining center lathe workpieces, JMPP provides Mazak machine distributors with a distinct Made-in-the-USA option with competitive advantages–quicker response times, advanced production, and better pricing to their customers.
JMPP President, John Stoneback, emphasized that, “We regularly respond to requests for custom retention knobs. Ultimately, the Mazak coupling bolt customization project presented us with an opportunity to expand our line of retention knobs and other spindle maintenance products. Customers for these coupling bolts can now realize added machining savings in the form of better finishes, less runout, increased speeds and feeds, reduced machine idle-time, and improved production rates.”
JM Performance Products now stocks Mazak part 53488025001 as JM53488025001HTHS, and Mazak part 53488025101 as JM53488025101HTHS–for immediate shipment.
Contact Details
Related Glossary Terms
- centers
centers
Cone-shaped pins that support a workpiece by one or two ends during machining. The centers fit into holes drilled in the workpiece ends. Centers that turn with the workpiece are called “live” centers; those that do not are called “dead” centers.
- computer numerical control ( CNC)
computer numerical control ( CNC)
Microprocessor-based controller dedicated to a machine tool that permits the creation or modification of parts. Programmed numerical control activates the machine’s servos and spindle drives and controls the various machining operations. See DNC, direct numerical control; NC, numerical control.
- lathe
lathe
Turning machine capable of sawing, milling, grinding, gear-cutting, drilling, reaming, boring, threading, facing, chamfering, grooving, knurling, spinning, parting, necking, taper-cutting, and cam- and eccentric-cutting, as well as step- and straight-turning. Comes in a variety of forms, ranging from manual to semiautomatic to fully automatic, with major types being engine lathes, turning and contouring lathes, turret lathes and numerical-control lathes. The engine lathe consists of a headstock and spindle, tailstock, bed, carriage (complete with apron) and cross slides. Features include gear- (speed) and feed-selector levers, toolpost, compound rest, lead screw and reversing lead screw, threading dial and rapid-traverse lever. Special lathe types include through-the-spindle, camshaft and crankshaft, brake drum and rotor, spinning and gun-barrel machines. Toolroom and bench lathes are used for precision work; the former for tool-and-die work and similar tasks, the latter for small workpieces (instruments, watches), normally without a power feed. Models are typically designated according to their “swing,” or the largest-diameter workpiece that can be rotated; bed length, or the distance between centers; and horsepower generated. See turning machine.
- machining center
machining center
CNC machine tool capable of drilling, reaming, tapping, milling and boring. Normally comes with an automatic toolchanger. See automatic toolchanger.
- milling machine ( mill)
milling machine ( mill)
Runs endmills and arbor-mounted milling cutters. Features include a head with a spindle that drives the cutters; a column, knee and table that provide motion in the three Cartesian axes; and a base that supports the components and houses the cutting-fluid pump and reservoir. The work is mounted on the table and fed into the rotating cutter or endmill to accomplish the milling steps; vertical milling machines also feed endmills into the work by means of a spindle-mounted quill. Models range from small manual machines to big bed-type and duplex mills. All take one of three basic forms: vertical, horizontal or convertible horizontal/vertical. Vertical machines may be knee-type (the table is mounted on a knee that can be elevated) or bed-type (the table is securely supported and only moves horizontally). In general, horizontal machines are bigger and more powerful, while vertical machines are lighter but more versatile and easier to set up and operate.
- toolholder
toolholder
Secures a cutting tool during a machining operation. Basic types include block, cartridge, chuck, collet, fixed, modular, quick-change and rotating.
- turning
turning
Workpiece is held in a chuck, mounted on a face plate or secured between centers and rotated while a cutting tool, normally a single-point tool, is fed into it along its periphery or across its end or face. Takes the form of straight turning (cutting along the periphery of the workpiece); taper turning (creating a taper); step turning (turning different-size diameters on the same work); chamfering (beveling an edge or shoulder); facing (cutting on an end); turning threads (usually external but can be internal); roughing (high-volume metal removal); and finishing (final light cuts). Performed on lathes, turning centers, chucking machines, automatic screw machines and similar machines.