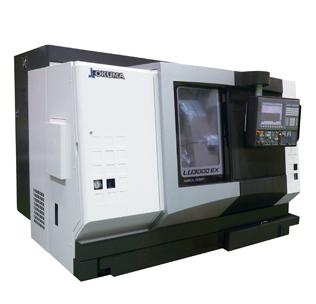
Okuma says its new LU3000 EX-M turning center is known for excellence in manufacturing precision parts in high production environments and is designed for reliability, longevity and maximized up-time. The LU3000 EX-M is built as an integrated production system with one goal in mind: to provide the customer with a machine that makes precision parts with the highest level of efficiency for years of trouble free production. This machine features a compact design, heavy duty, cast iron base, in addition to optimized CNC, motors and drive systems that are specifically designed to work together for maximum machine performance.
With a powerful main spindle and dual-servo turrets capable of simultaneous, synchronized control, the LU3000 EX-M has the power and flexibility to produce parts with the highest level of efficiency - two tools in the cut maximize production. Additionally, Okuma offers a series of functions specifically designed to enhance and simplify simultaneous 4-axis turning, including a single programming file for both turrets, and the ability to program both turrets as if they were the upper turret operating on the left spindle.
Consistent quality is a key requirement for automotive production. The LU3000 EX-M, designed and built around Okuma’s Thermal Friendly Concept, is capable of producing high quality parts across multiple shifts despite changing environmental temperatures. With its box-slant bed design the LU3000 EX-M experiences minimal thermal growth over time.
Contact Details
Related Glossary Terms
- computer numerical control ( CNC)
computer numerical control ( CNC)
Microprocessor-based controller dedicated to a machine tool that permits the creation or modification of parts. Programmed numerical control activates the machine’s servos and spindle drives and controls the various machining operations. See DNC, direct numerical control; NC, numerical control.
- turning
turning
Workpiece is held in a chuck, mounted on a face plate or secured between centers and rotated while a cutting tool, normally a single-point tool, is fed into it along its periphery or across its end or face. Takes the form of straight turning (cutting along the periphery of the workpiece); taper turning (creating a taper); step turning (turning different-size diameters on the same work); chamfering (beveling an edge or shoulder); facing (cutting on an end); turning threads (usually external but can be internal); roughing (high-volume metal removal); and finishing (final light cuts). Performed on lathes, turning centers, chucking machines, automatic screw machines and similar machines.