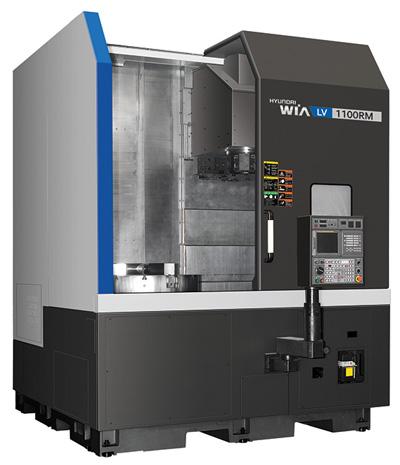
Hyundai WIA announces an all new heavy-duty, high production vertical CNC turning center, the LV1100RM. This new vertical turning center feature a rigid and stable platform for heavy-duty cutting, a single piece and a square type column that offers the ultimate stability. Vertical configuration offers superior chip flow and is ideal for in-line production applications with automation.
The LV11100RM features a traveling column to maintain superior accuracy when turning larger work pieces. Each axis is directly connected to a highly reliable digital servo motor to provide high rigidity and minimal thermal distortion. All axes are driven by large diameter, high precision double-nut ball screws. The double pretension design provides outstanding positioning and repeatability with virtually no thermal growth. All ball screws are connected directly to the servo drive motors without gears or belts, eliminating backlash.
The LV 1100 RM bed contributes production improvements with maximum processing area of equivalent machines in this class. Maximum swing: 1,355mm. Maximum cutting diameter: 1,160mm. The single piece, square type column offers the ultimate stability by absorbing vibration and eliminating twisting. This delivers superior precision even in heavy cuts. All axes of the LV1100RM feature box guideways. With the counterbalance cylinder installed, the impact of the vertically moving Z-axis is minimized during rapid traverse. The slope type bed improves chip flow and disposal of cutting fluids and minimizes thermal growth in the machine base. X-axis travel: 620mm. Z-axis travel: 1000mm. X-axis rapid travel: 24 m/min. Z-axis rapid travel: 24 m/min.
The main spindle is designed to minimize heat distortion and vibration. High precision cutting is possible and prevents foreign material from entering into the main spindle. Heavy-duty cutting is possible from the servo motor's stable division and curvic coupling's powerful clamp pressure. The ideal shape and the arrangement of the tool holder enable effective cutting.
The spindle of the LV1100RM has been designed with the structure that simultaneously improves rigidity and precision using highly rigid, multiple rows of roller bearings. The optional Hi-Low Chuck pressure system allows the operator to control the pressure setting (high or low), based on each specific cutting situation. Contour machining is capable with BC axis, enabling the operator to machine outer shapes and pockets using rotating tools. The LV1100RM lathe has protective measures in place to keep chips and other foreign matter from entering the main spindle, ensuring long-term high precision performance. This new lathe incorporate a belt driven spindle, which minimizes noise and vibration during both heavy cutting as well as high-speed machining.
Hyundai WIA's servo driven turret, available with live tooling M-type features a large diameter coupling for powerful clamping, which enables heavy cuts and increased tool life. A large 12 station BMT turret is a standard feature, enabling high accuracy turning and milling operations in one set up. The turret is driven by high torque servo motor with a 0.4 sec indexing time in either direction.
The latest generation BMT top plate increases tool performance and ridity by securing each tool with 4 screws. Overall cutting power and capability have been improved for all applications, including milling, drilling and tapping. A number of tools: 12 each. Tool size: OD, 32 x 32mm. ID, 80mm. Indexing time: 0.6 sec/step. Mill Turret. Output: 11⁄7.5 kW. Speed: 3,000 RPM. Torque: 70/47.8 Nm. Collet Size: 34 (ER 50)mm. Type: BMT 85P.
Machining capabilities have been increased with the addition of a straight milling head, which can remove material from the side of the workpiece, and angular milling head, which can perform ID operations. A wide variety of additional tool holders can further enhance the machines with capabilities that include drilling and tapping, among others.
The LV heavy duty, CNC vertical turning center features the latest generation FANUC i CNC for performance and accuracy. This control makes available a multitude of post processor technologies available through a large network of CAM vendors. Networking capabilities allow programs to be loaded directly to the shop floor from the CAM workstation and the optional Manual Guide i conversational programming system, fast program creation is possible right at the machine tool control panel.
Contact Details
Related Glossary Terms
- backlash
backlash
Reaction in dynamic motion systems where potential energy that was created while the object was in motion is released when the object stops. Release of this potential energy or inertia causes the device to quickly snap backward relative to the last direction of motion. Backlash can cause a system’s final resting position to be different from what was intended and from where the control system intended to stop the device.
- chuck
chuck
Workholding device that affixes to a mill, lathe or drill-press spindle. It holds a tool or workpiece by one end, allowing it to be rotated. May also be fitted to the machine table to hold a workpiece. Two or more adjustable jaws actually hold the tool or part. May be actuated manually, pneumatically, hydraulically or electrically. See collet.
- collet
collet
Flexible-sided device that secures a tool or workpiece. Similar in function to a chuck, but can accommodate only a narrow size range. Typically provides greater gripping force and precision than a chuck. See chuck.
- computer numerical control ( CNC)
computer numerical control ( CNC)
Microprocessor-based controller dedicated to a machine tool that permits the creation or modification of parts. Programmed numerical control activates the machine’s servos and spindle drives and controls the various machining operations. See DNC, direct numerical control; NC, numerical control.
- computer-aided manufacturing ( CAM)
computer-aided manufacturing ( CAM)
Use of computers to control machining and manufacturing processes.
- conversational programming
conversational programming
Method for using plain English to produce G-code file without knowing G-code in order to program CNC machines.
- gang cutting ( milling)
gang cutting ( milling)
Machining with several cutters mounted on a single arbor, generally for simultaneous cutting.
- inner diameter ( ID)
inner diameter ( ID)
Dimension that defines the inside diameter of a cavity or hole. See OD, outer diameter.
- lathe
lathe
Turning machine capable of sawing, milling, grinding, gear-cutting, drilling, reaming, boring, threading, facing, chamfering, grooving, knurling, spinning, parting, necking, taper-cutting, and cam- and eccentric-cutting, as well as step- and straight-turning. Comes in a variety of forms, ranging from manual to semiautomatic to fully automatic, with major types being engine lathes, turning and contouring lathes, turret lathes and numerical-control lathes. The engine lathe consists of a headstock and spindle, tailstock, bed, carriage (complete with apron) and cross slides. Features include gear- (speed) and feed-selector levers, toolpost, compound rest, lead screw and reversing lead screw, threading dial and rapid-traverse lever. Special lathe types include through-the-spindle, camshaft and crankshaft, brake drum and rotor, spinning and gun-barrel machines. Toolroom and bench lathes are used for precision work; the former for tool-and-die work and similar tasks, the latter for small workpieces (instruments, watches), normally without a power feed. Models are typically designated according to their “swing,” or the largest-diameter workpiece that can be rotated; bed length, or the distance between centers; and horsepower generated. See turning machine.
- milling
milling
Machining operation in which metal or other material is removed by applying power to a rotating cutter. In vertical milling, the cutting tool is mounted vertically on the spindle. In horizontal milling, the cutting tool is mounted horizontally, either directly on the spindle or on an arbor. Horizontal milling is further broken down into conventional milling, where the cutter rotates opposite the direction of feed, or “up” into the workpiece; and climb milling, where the cutter rotates in the direction of feed, or “down” into the workpiece. Milling operations include plane or surface milling, endmilling, facemilling, angle milling, form milling and profiling.
- milling machine ( mill)
milling machine ( mill)
Runs endmills and arbor-mounted milling cutters. Features include a head with a spindle that drives the cutters; a column, knee and table that provide motion in the three Cartesian axes; and a base that supports the components and houses the cutting-fluid pump and reservoir. The work is mounted on the table and fed into the rotating cutter or endmill to accomplish the milling steps; vertical milling machines also feed endmills into the work by means of a spindle-mounted quill. Models range from small manual machines to big bed-type and duplex mills. All take one of three basic forms: vertical, horizontal or convertible horizontal/vertical. Vertical machines may be knee-type (the table is mounted on a knee that can be elevated) or bed-type (the table is securely supported and only moves horizontally). In general, horizontal machines are bigger and more powerful, while vertical machines are lighter but more versatile and easier to set up and operate.
- outer diameter ( OD)
outer diameter ( OD)
Dimension that defines the exterior diameter of a cylindrical or round part. See ID, inner diameter.
- rapid traverse
rapid traverse
Movement on a CNC mill or lathe that is from point to point at full speed but, usually, without linear interpolation.
- tapping
tapping
Machining operation in which a tap, with teeth on its periphery, cuts internal threads in a predrilled hole having a smaller diameter than the tap diameter. Threads are formed by a combined rotary and axial-relative motion between tap and workpiece. See tap.
- turning
turning
Workpiece is held in a chuck, mounted on a face plate or secured between centers and rotated while a cutting tool, normally a single-point tool, is fed into it along its periphery or across its end or face. Takes the form of straight turning (cutting along the periphery of the workpiece); taper turning (creating a taper); step turning (turning different-size diameters on the same work); chamfering (beveling an edge or shoulder); facing (cutting on an end); turning threads (usually external but can be internal); roughing (high-volume metal removal); and finishing (final light cuts). Performed on lathes, turning centers, chucking machines, automatic screw machines and similar machines.