Contact Details
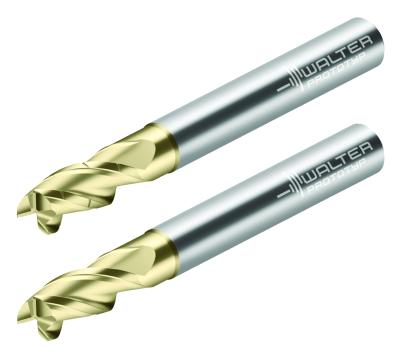
Walter takes the lead in solid carbide milling with the introduction of more than 3,000 new cutting tools in inch sizes. The expansion includes the MA267/MA263 Advance milling tools with straight-forward proven geometries for a cost-effective and reliable milling process at an extremely high metal removal rate and the MA268 for high-velocity rough machining.
Available in diameters from 1/8" to 1", the MA267/MA263 Advance tools are excellent for machining all other ISO N materials, such as copper, brass, bronze and magnesium-based alloys, in addition to aluminum. With a cylindrical shank, these tools are available with or without chip-splitters.
The WJ30UU grade for the MA267/MA263 tools is uncoated, and the WJ30CD grade features a wear-resistant zirconium nitride (ZrN) coating to achieve maximum productivity and tool life. The MA263 with chip breaker geometry reduces cutting pressure and vibration at high feed rates. Both versions offer end geometry that is designed for aggressive ramping.
Benefits include imparting consistently fine surface finishes throughout the entire tool life, polish grinds to generate superior surface finishes on both walls and floors, and a polished flute face that optimizes chip evacuation.
Walter also developed the MA268 to machine all ISO N materials at the highest level. The solid carbide milling cutter has a 39° helix and is available from 1/4" to 1" in diameter. The tool has a cylindrical shank and is available with a standard or reduced neck. The MA268 is also offered in the uncoated WJ30UU grade and the WJ30CD grade with the reliable ZrN coating. The cutter’s unique geometry reduces cutting pressures and vibration at high feed rates. The highly polished OD and flute face prevents chip build-up. Knuckles, or the serrated cutting edges, shorten the chip length to aid chip evacuation and reduce tool pressure.
The Walter lineup of products consists of three categories of tools. Supreme tools indicate the highest level of technology and performance available. Advance tools indicate products efficiently balanced between price and performance and Perform tools are products that provide an economical solution with focused importance on price.
Related Glossary Terms
- alloys
alloys
Substances having metallic properties and being composed of two or more chemical elements of which at least one is a metal.
- feed
feed
Rate of change of position of the tool as a whole, relative to the workpiece while cutting.
- gang cutting ( milling)
gang cutting ( milling)
Machining with several cutters mounted on a single arbor, generally for simultaneous cutting.
- milling
milling
Machining operation in which metal or other material is removed by applying power to a rotating cutter. In vertical milling, the cutting tool is mounted vertically on the spindle. In horizontal milling, the cutting tool is mounted horizontally, either directly on the spindle or on an arbor. Horizontal milling is further broken down into conventional milling, where the cutter rotates opposite the direction of feed, or “up” into the workpiece; and climb milling, where the cutter rotates in the direction of feed, or “down” into the workpiece. Milling operations include plane or surface milling, endmilling, facemilling, angle milling, form milling and profiling.
- milling cutter
milling cutter
Loosely, any milling tool. Horizontal cutters take the form of plain milling cutters, plain spiral-tooth cutters, helical cutters, side-milling cutters, staggered-tooth side-milling cutters, facemilling cutters, angular cutters, double-angle cutters, convex and concave form-milling cutters, straddle-sprocket cutters, spur-gear cutters, corner-rounding cutters and slitting saws. Vertical cutters use shank-mounted cutting tools, including endmills, T-slot cutters, Woodruff keyseat cutters and dovetail cutters; these may also be used on horizontal mills. See milling.
- outer diameter ( OD)
outer diameter ( OD)
Dimension that defines the exterior diameter of a cylindrical or round part. See ID, inner diameter.
- shank
shank
Main body of a tool; the portion of a drill or similar end-held tool that fits into a collet, chuck or similar mounting device.