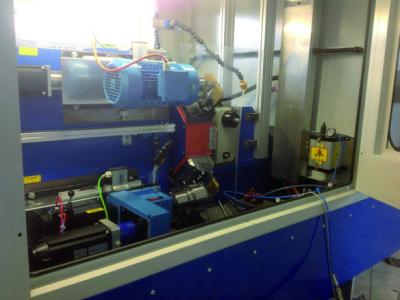
Operations for the prep on tubings and pipes generally require multiple manufacturing steps such as cutting, chamfering, face-off, turning and tapping including thread milling or thread forming. Higher part quantities usually combined with the need for different manufacturing steps demand efficient and time saving production methods to help reduce time and cost. Special purpose machines such as rotary and linear transfer machines, offer the best solutions to help obtain shorter overall part cycle times.
An extensive background of experience with operations on transfer machines allows Suhner to optimize a manufacturing process with standard or custom solutions for each machining application. One specific application is for large and long OD threads. These operations are extremely difficult and challenging for manufacturers, when trying to obtain shorter cycle times, simply because an OD threading operation by itself will dictate the overall machine cycle time.
Suhner, in cooperation with Wagner, a German manufacturer for OD thread rolling heads, has developed a special process, which allows threading operations in very short cycle times. A pneumatic cylinder-activated system is used to open and close the thread rolling head, which is equipped with multiple thread cutting or forming inserts.
The workpiece is fed from bar stock material. After a cut to length operation, it is machined by (3) Suhner BEX15 machining units with special Weldon toolholders. Operations include OD and ID and face turning. All units are equipped with a 1.5kW motor and high precision angular contact spindle bearings.
The most interesting station on this machine is the one for an OD threading operation, which is accomplished with a BEX35-ISO40 machining unit equipped with a Wagner thread rolling head type Z27-2. In this operation, the thread rolling head is rotating and the workpiece is stationary. The feed motion for this station is done with a CNC slide unit. To synchronize the thread pitch, both the BEX35 spindle and CNC slide are servomotor driven.
As soon as the threading operation is finished, the Wagner thread rolling head with integrated inserts opens quickly to allow a fast return to the home position.
Opening and closing action of the head is accomplished by an internal BEX35 drawbar, controlled by a three-position pneumatic cylinder.
This pneumatic cylinder is designed to make an additional stroke of 10mm. This allows for head and insert adjustments or replacements, depending on thread size.
Depending on length, a typical OD thread rolling cycle time ranges between 6 to10 seconds. Thanks to the application of CNC servo driven spindle and slide components, customers can achieve very short changeover time, as well.
Contact Details
Related Glossary Terms
- chamfering
chamfering
Machining a bevel on a workpiece or tool; improves a tool’s entrance into the cut.
- computer numerical control ( CNC)
computer numerical control ( CNC)
Microprocessor-based controller dedicated to a machine tool that permits the creation or modification of parts. Programmed numerical control activates the machine’s servos and spindle drives and controls the various machining operations. See DNC, direct numerical control; NC, numerical control.
- feed
feed
Rate of change of position of the tool as a whole, relative to the workpiece while cutting.
- gang cutting ( milling)
gang cutting ( milling)
Machining with several cutters mounted on a single arbor, generally for simultaneous cutting.
- inner diameter ( ID)
inner diameter ( ID)
Dimension that defines the inside diameter of a cavity or hole. See OD, outer diameter.
- milling
milling
Machining operation in which metal or other material is removed by applying power to a rotating cutter. In vertical milling, the cutting tool is mounted vertically on the spindle. In horizontal milling, the cutting tool is mounted horizontally, either directly on the spindle or on an arbor. Horizontal milling is further broken down into conventional milling, where the cutter rotates opposite the direction of feed, or “up” into the workpiece; and climb milling, where the cutter rotates in the direction of feed, or “down” into the workpiece. Milling operations include plane or surface milling, endmilling, facemilling, angle milling, form milling and profiling.
- outer diameter ( OD)
outer diameter ( OD)
Dimension that defines the exterior diameter of a cylindrical or round part. See ID, inner diameter.
- pitch
pitch
1. On a saw blade, the number of teeth per inch. 2. In threading, the number of threads per inch.
- tapping
tapping
Machining operation in which a tap, with teeth on its periphery, cuts internal threads in a predrilled hole having a smaller diameter than the tap diameter. Threads are formed by a combined rotary and axial-relative motion between tap and workpiece. See tap.
- thread rolling
thread rolling
Chipless, cold-forming material-displacement process where a rolling head is pressed into the workpiece to create threads. The material is stressed beyond its yield point, which causes it to be deformed platically and permanently. There are three basic types of rolling heads: axial, radial and tangential.
- threading
threading
Process of both external (e.g., thread milling) and internal (e.g., tapping, thread milling) cutting, turning and rolling of threads into particular material. Standardized specifications are available to determine the desired results of the threading process. Numerous thread-series designations are written for specific applications. Threading often is performed on a lathe. Specifications such as thread height are critical in determining the strength of the threads. The material used is taken into consideration in determining the expected results of any particular application for that threaded piece. In external threading, a calculated depth is required as well as a particular angle to the cut. To perform internal threading, the exact diameter to bore the hole is critical before threading. The threads are distinguished from one another by the amount of tolerance and/or allowance that is specified. See turning.
- turning
turning
Workpiece is held in a chuck, mounted on a face plate or secured between centers and rotated while a cutting tool, normally a single-point tool, is fed into it along its periphery or across its end or face. Takes the form of straight turning (cutting along the periphery of the workpiece); taper turning (creating a taper); step turning (turning different-size diameters on the same work); chamfering (beveling an edge or shoulder); facing (cutting on an end); turning threads (usually external but can be internal); roughing (high-volume metal removal); and finishing (final light cuts). Performed on lathes, turning centers, chucking machines, automatic screw machines and similar machines.