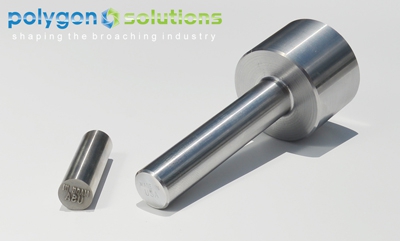
Polygon Solution Inc.'s new "Made in USA" broach is a rotary broach with multiple text letters allowing machinists to stamp or mark their part in a lathe or milling machine without removing the part from the machine. Polygon's rotary broaching system is usually used for making hexagon or square holes in precision machined products.
Polygon Solutions first introduced an innovative and award winning adjustment free Rotary Broach Tool Holder in 2010, ideal for CNC machines because of maintenance free sealed bearings and a new pressure relief system. The company later announced a series of letter broaches in 2012. The broaches have letters or numbers and are inserted into Polygon's broach holder to mark parts. The different identifying marks improve quality to distinguish between mixed lots of parts made in the same machines.
The "Made in USA" broach was first tested during Polygon's annual National Association of Manufacturers Manufacturing Day tour in 2013. Lee Virtual School students in Fort Myers, FL were taught about product development and how the new rotary broach ‘wobbles' or displaces material to create the text. Polygon showcases new products to students in hopes of promoting the desire for STEM education in a new generation of engineers and machinists.
"Made in America is one of the strongest selling points we have, even for our U.S. customers," says Matt Chambers of Marine Concepts in Cape Coral, Fla. "The quality of the overseas product has been from the start an inferior product, and as the cost of quality is more than ever being taken into account, not only are we sought after for quality but our total cost for our customer is less."
Marine Concepts and Polygon Solutions Inc. actively work together as members of the Florida's Southwest Regional Manufacturing Association.
Polygon's new broach is not limited to the "Made in USA" mark. The company sells its tools worldwide and is also developing the system to mark logos, slogans and symbols. "We've had a few challenges to get it to work perfectly," says Peter Bagwell, product engineer at Polygon. "But we keep working with our customers and our partners to get it right. Customers re-shoring their parts want to show they are now made in the United States."
Partners include the Precision Machined Product Association and National Tooling & Machining Association. Bagwell adds, "We've learned from our customers that our rotary broach holder is very easy to set up in the machine and very easy to use for making small hexagon and square holes. We hope the new 'Made in USA' broach helps them achieve an even higher level of satisfaction in both their parts and ours."
Contact Details
Related Glossary Terms
- broach
broach
Tapered tool, with a series of teeth of increasing length, that is pushed or pulled into a workpiece, successively removing small amounts of metal to enlarge a hole, slot or other opening to final size.
- broaching
broaching
Operation in which a cutter progressively enlarges a slot or hole or shapes a workpiece exterior. Low teeth start the cut, intermediate teeth remove the majority of the material and high teeth finish the task. Broaching can be a one-step operation, as opposed to milling and slotting, which require repeated passes. Typically, however, broaching also involves multiple passes.
- computer numerical control ( CNC)
computer numerical control ( CNC)
Microprocessor-based controller dedicated to a machine tool that permits the creation or modification of parts. Programmed numerical control activates the machine’s servos and spindle drives and controls the various machining operations. See DNC, direct numerical control; NC, numerical control.
- gang cutting ( milling)
gang cutting ( milling)
Machining with several cutters mounted on a single arbor, generally for simultaneous cutting.
- lathe
lathe
Turning machine capable of sawing, milling, grinding, gear-cutting, drilling, reaming, boring, threading, facing, chamfering, grooving, knurling, spinning, parting, necking, taper-cutting, and cam- and eccentric-cutting, as well as step- and straight-turning. Comes in a variety of forms, ranging from manual to semiautomatic to fully automatic, with major types being engine lathes, turning and contouring lathes, turret lathes and numerical-control lathes. The engine lathe consists of a headstock and spindle, tailstock, bed, carriage (complete with apron) and cross slides. Features include gear- (speed) and feed-selector levers, toolpost, compound rest, lead screw and reversing lead screw, threading dial and rapid-traverse lever. Special lathe types include through-the-spindle, camshaft and crankshaft, brake drum and rotor, spinning and gun-barrel machines. Toolroom and bench lathes are used for precision work; the former for tool-and-die work and similar tasks, the latter for small workpieces (instruments, watches), normally without a power feed. Models are typically designated according to their “swing,” or the largest-diameter workpiece that can be rotated; bed length, or the distance between centers; and horsepower generated. See turning machine.
- milling
milling
Machining operation in which metal or other material is removed by applying power to a rotating cutter. In vertical milling, the cutting tool is mounted vertically on the spindle. In horizontal milling, the cutting tool is mounted horizontally, either directly on the spindle or on an arbor. Horizontal milling is further broken down into conventional milling, where the cutter rotates opposite the direction of feed, or “up” into the workpiece; and climb milling, where the cutter rotates in the direction of feed, or “down” into the workpiece. Milling operations include plane or surface milling, endmilling, facemilling, angle milling, form milling and profiling.
- milling machine ( mill)
milling machine ( mill)
Runs endmills and arbor-mounted milling cutters. Features include a head with a spindle that drives the cutters; a column, knee and table that provide motion in the three Cartesian axes; and a base that supports the components and houses the cutting-fluid pump and reservoir. The work is mounted on the table and fed into the rotating cutter or endmill to accomplish the milling steps; vertical milling machines also feed endmills into the work by means of a spindle-mounted quill. Models range from small manual machines to big bed-type and duplex mills. All take one of three basic forms: vertical, horizontal or convertible horizontal/vertical. Vertical machines may be knee-type (the table is mounted on a knee that can be elevated) or bed-type (the table is securely supported and only moves horizontally). In general, horizontal machines are bigger and more powerful, while vertical machines are lighter but more versatile and easier to set up and operate.
- relief
relief
Space provided behind the cutting edges to prevent rubbing. Sometimes called primary relief. Secondary relief provides additional space behind primary relief. Relief on end teeth is axial relief; relief on side teeth is peripheral relief.