Contact Details
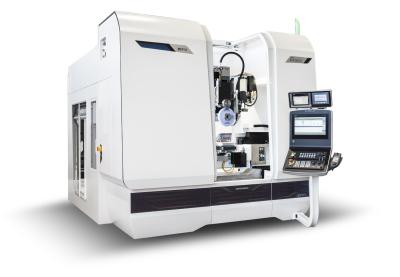
UNITED GRINDING offers the MÄGERLE MFP 51, which combines grinding with conventional machining operations within one production system. This flexible machine comes equipped with either 5 or 6 axes for grinding, milling and drilling operations to process parts in single clampings for improved accuracy and output.
In its standard configuration, the MÄGERLE MFP 51 includes a high-precision 12,000-rpm spindle and an integrated 66-position toolchanger for efficient machining of multiple workpieces without the need for complete tooling changes. The machine’s coolant nozzle features 2-axis control for full freedom of movement and precise positioning of coolant delivery to the tool and/or workpiece. Through-the-spindle coolant delivery, along with nozzles on the grinding support, optimize coolant delivery. An optional nozzle changer allows for further adaptation of the coolant supply delivery to individual jobs.
An overhead grinding wheel dresser on the MÄGERLE MFP 51 is integrated into the machine’s grinding support to shorten process times. Options include an RFID-based identification system for grinding wheels and tools to eliminate errors when entering tool data in the machine.
Related Glossary Terms
- coolant
coolant
Fluid that reduces temperature buildup at the tool/workpiece interface during machining. Normally takes the form of a liquid such as soluble or chemical mixtures (semisynthetic, synthetic) but can be pressurized air or other gas. Because of water’s ability to absorb great quantities of heat, it is widely used as a coolant and vehicle for various cutting compounds, with the water-to-compound ratio varying with the machining task. See cutting fluid; semisynthetic cutting fluid; soluble-oil cutting fluid; synthetic cutting fluid.
- gang cutting ( milling)
gang cutting ( milling)
Machining with several cutters mounted on a single arbor, generally for simultaneous cutting.
- grinding
grinding
Machining operation in which material is removed from the workpiece by a powered abrasive wheel, stone, belt, paste, sheet, compound, slurry, etc. Takes various forms: surface grinding (creates flat and/or squared surfaces); cylindrical grinding (for external cylindrical and tapered shapes, fillets, undercuts, etc.); centerless grinding; chamfering; thread and form grinding; tool and cutter grinding; offhand grinding; lapping and polishing (grinding with extremely fine grits to create ultrasmooth surfaces); honing; and disc grinding.
- grinding wheel
grinding wheel
Wheel formed from abrasive material mixed in a suitable matrix. Takes a variety of shapes but falls into two basic categories: one that cuts on its periphery, as in reciprocating grinding, and one that cuts on its side or face, as in tool and cutter grinding.
- milling
milling
Machining operation in which metal or other material is removed by applying power to a rotating cutter. In vertical milling, the cutting tool is mounted vertically on the spindle. In horizontal milling, the cutting tool is mounted horizontally, either directly on the spindle or on an arbor. Horizontal milling is further broken down into conventional milling, where the cutter rotates opposite the direction of feed, or “up” into the workpiece; and climb milling, where the cutter rotates in the direction of feed, or “down” into the workpiece. Milling operations include plane or surface milling, endmilling, facemilling, angle milling, form milling and profiling.
- toolchanger
toolchanger
Carriage or drum attached to a machining center that holds tools until needed; when a tool is needed, the toolchanger inserts the tool into the machine spindle. See automatic toolchanger.