Contact Details
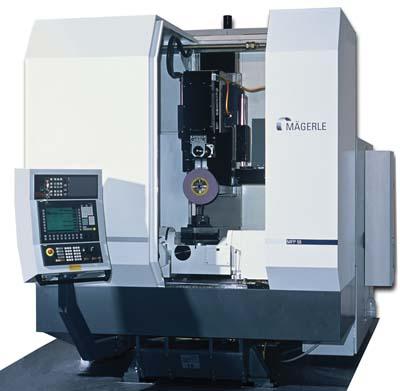
United Grinding Technologies offers the new Magerle MFP 50 5-axis CD Grinding Center featuring automatic grinding wheel and tool changer, representing one of the most flexible, multi-tasking CD grinders in the Magerle family.
The MFP 50 is the smallest in the Magerle machine line and offers a great number of various configurations, depending on the application. The compact and symmetrical traversing sliding column design, together with precision pre-loaded ball screws and wide hydrostatic guideway bearings, ensures high static, dynamic and thermal stability.
The MFP 50 includes an integrated automatic tool changer which can switch wheels in eight seconds using a swing arm configuration. Maximum tool dimensions are 300mm x 60mm x 76.2mm, and wheel/tool changer capacity, depending on the diameter, is 10 to 30 conventional grinding wheels, plated or ceramic bonded CBN wheels as well as drilling and milling tools. A reliable HSK-80 wheel flange system offers rigidity and precision needed for close tolerance parts with high surface finish requirements. Tool options include vitrified CBN, plated CBN, conventional grinding wheels and various other metal cutting options.
The machine is equipped with a proven overhead mounted two axes CD diamond dresser with horizontal and vertical NC axis for the accommodation of several diamond rolls with various profiles for CD or non-CD, as well as for CNC dressing with a disc. The grinding wheels with different profiles are always on the same spindle position.
An important feature of the MFP 50 are its guideways. Magerle developed hydrostatic wrap-around guideways utilized in the Y-axis. These are 100 percent wear-free and offer high rigidity and load capacity, optimum smoothness and vibration dampening and maximum precision and process reliability. All main axes of the MFP 50 can rapid traverse at 20,000mm/min (790 ipm). X-axis travel is 500mm, Y-axis spindle travel is 660mm and Z-axis travel is 660mm.
The MFP 50 features state-of-the-art Siemens Sinumerik 840D digital controls. Machine operation, setup, changeover, dressing and programming of even complex parts are easily accomplished through the operator-friendly control. Typical applications include turbine vanes and blades, small turbine and compressor blades, machining both sides of fir tree and root shank faces, shroud and z-notch profiles, both sides and slots if required. The automatic tool changer allows the use of the right abrasive for each feature plated CBN for radial slots, vitrified CBN for blade W-forms, conventional abrasives for radial slots and blade fir trees.
Related Glossary Terms
- abrasive
abrasive
Substance used for grinding, honing, lapping, superfinishing and polishing. Examples include garnet, emery, corundum, silicon carbide, cubic boron nitride and diamond in various grit sizes.
- computer numerical control ( CNC)
computer numerical control ( CNC)
Microprocessor-based controller dedicated to a machine tool that permits the creation or modification of parts. Programmed numerical control activates the machine’s servos and spindle drives and controls the various machining operations. See DNC, direct numerical control; NC, numerical control.
- cubic boron nitride ( CBN)
cubic boron nitride ( CBN)
Crystal manufactured from boron nitride under high pressure and temperature. Used to cut hard-to-machine ferrous and nickel-base materials up to 70 HRC. Second hardest material after diamond. See superabrasive tools.
- dressing
dressing
Removal of undesirable materials from “loaded” grinding wheels using a single- or multi-point diamond or other tool. The process also exposes unused, sharp abrasive points. See loading; truing.
- gang cutting ( milling)
gang cutting ( milling)
Machining with several cutters mounted on a single arbor, generally for simultaneous cutting.
- grinding
grinding
Machining operation in which material is removed from the workpiece by a powered abrasive wheel, stone, belt, paste, sheet, compound, slurry, etc. Takes various forms: surface grinding (creates flat and/or squared surfaces); cylindrical grinding (for external cylindrical and tapered shapes, fillets, undercuts, etc.); centerless grinding; chamfering; thread and form grinding; tool and cutter grinding; offhand grinding; lapping and polishing (grinding with extremely fine grits to create ultrasmooth surfaces); honing; and disc grinding.
- grinding wheel
grinding wheel
Wheel formed from abrasive material mixed in a suitable matrix. Takes a variety of shapes but falls into two basic categories: one that cuts on its periphery, as in reciprocating grinding, and one that cuts on its side or face, as in tool and cutter grinding.
- milling
milling
Machining operation in which metal or other material is removed by applying power to a rotating cutter. In vertical milling, the cutting tool is mounted vertically on the spindle. In horizontal milling, the cutting tool is mounted horizontally, either directly on the spindle or on an arbor. Horizontal milling is further broken down into conventional milling, where the cutter rotates opposite the direction of feed, or “up” into the workpiece; and climb milling, where the cutter rotates in the direction of feed, or “down” into the workpiece. Milling operations include plane or surface milling, endmilling, facemilling, angle milling, form milling and profiling.
- numerical control ( NC)
numerical control ( NC)
Any controlled equipment that allows an operator to program its movement by entering a series of coded numbers and symbols. See CNC, computer numerical control; DNC, direct numerical control.
- rapid traverse
rapid traverse
Movement on a CNC mill or lathe that is from point to point at full speed but, usually, without linear interpolation.
- shank
shank
Main body of a tool; the portion of a drill or similar end-held tool that fits into a collet, chuck or similar mounting device.
- tolerance
tolerance
Minimum and maximum amount a workpiece dimension is allowed to vary from a set standard and still be acceptable.
- wheel flange
wheel flange
Metal plate inside the grinding-wheel hole that allows the wheel to be mounted on a spindle.